Industrial equipment is the backbone of manufacturing and production across numerous sectors. While these machines are designed for robust performance and longevity, certain factors can drastically reduce operating efficiency and lifespan of equipment. Lubricant contamination is the most common detrimental factor for industrial equipment. Water is often the most destructive contaminant.
The negative effects of water contamination are many, and the most significant ones are described below.
Corrosion: Water contamination is the primary cause of rust and corrosion in machinery, causing component damage and potentially equipment failure.
Cavitation and Erosion: Water contamination in lubricating oil can lead to cavitation in fluid systems like hydraulics. In low-pressure areas, microscopic water vapor bubbles form and then collapse under high pressure. The collapsing vapor bubbles create damaging shock waves that cause microcracks and surface erosion in equipment components.
Lubricant Degradation: Water contamination accelerates the oxidation process in lubricating oils, leading to the formation of sludge and varnish. These deposits can clog filters and restrict oil flow. The premature oxidation also reduces the useful life of the lubricant, requiring more frequent oil changes.
Decreased Viscosity: The viscosity of water is much lower than virtually all lubricants. If a significant amount of water is mixed into a lubricating oil, the overall viscosity of the oil will be lower. The reduced viscosity can result in reduced load-carrying capability of the lubricating oil, leading to more metal-to-metal contact, more friction and more wear.
Hydrolysis: Water can react with additives in oil, causing them to break down. This reduces its effectiveness. It can lead to the formation of acidic byproducts that can further damage seals and metal components. Some base oils used to make lubricants will also hydrolyze in the presence of water, further degrading the lubricant.
Microbial Growth: Water in oil can promote the growth of bacteria and fungi. These microorganisms can produce acids and other corrosive substances, as well as lead to clogged oil filters and restricted oil flow.
Minimize Dielectric Strength: In electrical systems that use lubricating oil as an insulating fluid, water contamination can reduce the oils’ dielectric strength, leading to electrical failures and potential short circuits.
There are three main forms of water in oil: dissolved, emulsified and free water. All lubricating oils contain some amount of dissolved water. New and unused lubricating oils commonly have between 50 ppm (parts per million) and 250 ppm of dissolved water content. The amount of water in new oil is a function of raw material and production quality, as well as the types of base oils used in the lubricant manufacturing.
Dissolved water is commonly not observable with the naked eye. As the water content in the lubricant increases, the oil will appear cloudy due to water droplets suspended in the oil. As water contamination of the oil increases, excess water beyond the oil’s saturation point will separate from the oil and become free water. If the lubricant is hydrocarbon (mineral or synthetic) oil or ester, the free water will drop to the bottom because the water is denser than the oil. Temperature also plays a key role in the amount of dissolved and emulsified water in the lubricating oil. At higher temperatures, more water can be dissolved and suspended in the oil. An oil sample pulled from a machine that was recently running and still hot may appear clear or normal. If left for several hours to cool, the oil may become cloudy and/or separate from the water. Best practice would be to utilize a high-quality oil site gauge such as the BOSS™ site gauge from P-K Machine and allow the oil to cool. Then, drain off the water.
More often, customers complain that an oil and water emulsion has occurred where the operational oil is now hazy to a creamy white color. Many times, this occurs due to a contaminant in the oil or from an additive that will promote the formation of an emulsion. To obtain the best separation of the water from the oil, a high-quality synthetic oil with a high-quality additive system is best to employ.
Although most all applications are affected by water infiltration, rolling element bearings are very negatively affected by even small amounts of water contamination. Roller bearings are under extreme pressures. They operate in elastohydrodynamic lubrication regime where the bearings deform under the load zone and see tremendous pressures, sometimes up to 500,000 psi! Under these conditions, water molecules may cause hydrogen embrittlement of any steel or ferrous alloy components like rolling elements and bearing races, causing increased fatigue wear and corrosive wear.
In the graph below, an oil with 500 ppm of water that has shed water down to 45 ppm will increase the machine life by 400%.
Which synthetic lubricants are best to choose to shed water?
Generally speaking and with all else being equal (additive performance, manufacture quality, etc.), a synthetic lubricant will provide better performance and protection than a mineral lubricant. When considering water contamination and the lubricant’s ability to mitigate damage caused by water contamination, not all synthetic lubricants perform the same. High-quality synthetic base stocks have much better demulsibility (water-separation ability) than other common types of lubricant base stocks. Polyalphaolefins (PAOs) are the most common synthetic hydrocarbon base oils and perform excellently, allowing water to separate quickly from the oil. This allows the water to be left in the bottom of the oil reservoir rather than being circulated throughout the equipment. Many ester base stocks can also separate from water, but to varying degrees based on the particular ester oil in question. For example: Simpler, smaller-molecule esters like monoesters and diesters tend to be more soluble with water. More complex polyol esters are less soluble with water and have better separability. Polyalkylene glycols (PAGs) and other glycol fluids are completely soluble and miscible with water. They will not separate. This means an almost unlimited potential for dilution of PAG lubricating fluid compared to comparable hydrocarbon and ester lubricants.
What test is used to determine a product’s demulsibility?
One of the most popular tests is the ASTM D1401 method. A 40 mL sample of a test oil and 40 mL of distilled water are stirred for 5 minutes in a graduated cylinder at 54° C or 82° C. The time required for the separation of the emulsion is recorded either after every 5 minutes or at the specification time limit. If complete separation or emulsion reduction to 3 mL or less does not occur after standing for 30 minutes or some other specification time limit, the volumes of oil (or fluid), water and emulsion remaining at the time are reported. For example: Royal Purple® Synfilm® GT has excellent water separation. It has been reported on their ISO 68 as 40/38/2 (5).
Ultimately, the most effective remedies for water infiltration into oils center around prevention, detection and removal. Key preventive measures include maintaining high-quality seals, conducting regular maintenance and using superior desiccant breathers to control moisture entry. These steps help limit oil degradation, ensuring it can be used for its intended lifespan. By implementing these strategies, you not only preserve oil quality. You also extend machinery life, reduce downtime and minimize the risk of expensive rebuilds.
In conclusion, proactive management of water infiltration is crucial for maintaining oil performance and machinery efficiency. By focusing on prevention and early detection, you can protect your equipment, save on repair costs and ensure long-term operational success.
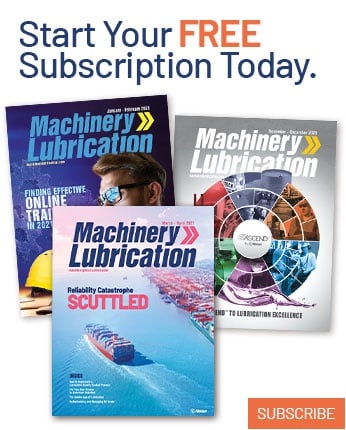