In today's rapidly evolving industrial landscape, the importance of workforce development cannot be overstated. As industries become more complex and technology-driven, a skilled and adaptable workforce in the industrial maintenance and reliability sector is paramount. This article explores the critical role of workforce development, the challenges faced, and the strategies that can be employed to build a robust, future-ready workforce.
The Importance of Workforce Development
Workforce development is a comprehensive approach aimed at improving employees' skills, competencies, and capabilities within an organization. In the context of industrial maintenance and reliability, workforce development is essential for several reasons:
- Ensuring Operational Efficiency: Skilled maintenance and reliability professionals are crucial for the smooth operation of industrial machinery and equipment. Properly trained staff can prevent unexpected downtimes, reduce maintenance costs, and improve operational efficiency.
- Adapting to Technological Advancements: The industrial sector is witnessing rapid technological advancements, from automation and robotics to the Industrial Internet of Things (IIoT) and predictive maintenance. A well-developed workforce is better equipped to adapt to these changes, ensuring the industry remains competitive.
- Enhancing Safety and Compliance: Workforce development programs ensure that employees are well-versed in safety protocols and compliance standards, reducing the risk of accidents and ensuring adherence to regulatory requirements.
- Addressing the Skills Gap: The industrial maintenance and reliability sector faces a significant skills gap, exacerbated by the retirement of experienced professionals and insufficient new talent. Workforce development initiatives are essential to bridge this gap and ensure a steady supply of skilled workers.
Challenges in Workforce Development
While the importance of workforce development is clear, the industry faces several challenges in implementing effective programs:
- Aging Workforce: Many experienced professionals in the industrial maintenance and reliability sector are nearing retirement, losing valuable knowledge and skills. This generational shift creates a pressing need for succession planning and knowledge transfer.
- Rapid Technological Changes: The pace of technological advancements can outstrip the ability of workforce development programs to keep up. Continuous training and upskilling are required to ensure that employees can effectively utilize new technologies.
- Attracting Young Talent: The industrial sector often struggles to attract younger generations who may perceive the industry as less glamorous than tech-driven fields. This perception challenge makes it difficult to recruit fresh talent.
- Resource Constraints: Developing and implementing workforce development programs require significant time, money, and resources investment. Many organizations, especially smaller ones, may struggle to allocate these resources effectively.
Strategies for Effective Workforce Development
To overcome these challenges and build a strong, future-ready workforce, the industrial maintenance and reliability industry can adopt several strategies:
- Invest in Training and Education: Continuous training and education are crucial for keeping the workforce updated with the latest technologies and best practices. Organizations should partner with educational institutions and industry associations to develop comprehensive training programs.
- Leverage Technology: Utilize digital tools and platforms to deliver training and development programs. E-learning modules, virtual reality (VR) simulations, and augmented reality (AR) applications can provide immersive and effective training experiences.
- Mentorship and Knowledge Transfer: Establish mentorship programs where experienced professionals can pass on their knowledge and skills to younger employees. This approach ensures that valuable expertise is retained within the organization.
- Promote Career Development: Offer clear career pathways and opportunities for advancement within the organization. This not only motivates employees but also helps in retaining top talent.
- Foster a Culture of Continuous Improvement: Encourage a culture where continuous learning and improvement are valued. Recognize and reward employees who actively participate in training and development initiatives.
- Collaborate with Industry Associations: Engage with industry associations and professional bodies to stay updated on the latest trends, standards, and best practices. These associations can also provide valuable resources and support for workforce development initiatives.
- Focus on Diversity and Inclusion: A diverse and inclusive workforce brings different perspectives and ideas, fostering innovation and problem-solving. Implementing policies that promote diversity and inclusion can help attract a broader talent pool.
Conclusion
Workforce development is critical to the industrial maintenance and reliability industry's success. By investing in their employees' skills and capabilities, organizations can ensure operational efficiency, adapt to technological advancements, enhance safety and compliance, and address the looming skills gap. Despite the challenges, adopting strategic approaches to workforce development can build a resilient and future-ready workforce, ultimately driving the industry's growth and competitiveness.
As the industry continues to evolve, a well-developed workforce will remain the cornerstone of industrial excellence.
Supplier Spotlight
Bel-Ray 2780 Waterfront Pkwy. E. Dr., Indianapolis, IN 46214 317-328-5660 | BelRay.com/industry/industrial/
Bel-Ray® Total Performance Lubricants take care of your production line as well as your bottom line. Trusted for over 75 years across a wide range of industries, our high-performance industrial lubricants are formulated to reduce energy consumption, reduce wear and tear, so you cut down on maintenance and downtime, while extending the life of your equipment to help lower your Total Cost of Ownership.
LubePM 1328 E. 43rd Court, Tulsa, OK 74105 800-597-5460 | LubePM.com
As a Lubrication Management System (LMS) engineered by lubrication professionals, LubePM helps an organization create accountability to ensure that every lubrication point is carefully maintained, inspected and measured. Ready to take your facility’s Lubrication Management System to the next level with LubePM? We’re ready to help. Simply request more information or schedule a demo.
Noria Education 1328 E. 43rd Court, Tulsa, OK 74105 800-597-5460 | Noria.com/Training
Take the guesswork out of machinery lubrication with Noria's education and training. Learn precision lubrication skills for maximizing machine reliability. Most maintenance programs achieve only 10 percent of the benefits available from oil analysis. Learn how to unlock the full potential of your oil analysis program.
Noria Academy 1328 E. 43rd Court, Tulsa, OK 74105 800-597-5460 | Noria.com/Academy
Obtaining certification can be a challenge; new terms, concepts and topics can overwhelm even the most experienced reliability professionals. Training experts all agree that extending the learning beyond the classroom dramatically increases knowledge retention. To aid in this retention and create an innovative student experience, Noria is pleased to offer the Noria Academy app.
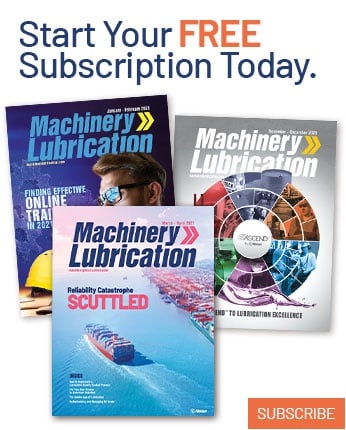