For many, the acronym IoT invokes images of cloud computing resources operating on massive quantities of data, all collected by myriads of ultra-low power wireless sensors, rendering the environment where these systems are deployed “smart” (Smart City, Smart Building, etc.).
Currently, much of the data collected as part of a comprehensive Predictive Maintenance (PdM) program is collected manually on a route, with collected measurands including vibration, oil sampling, IR or acoustic sensing information — each identifying emerging problems with industrial assets. There are many compelling reasons to deploy a wireless condition monitoring system in your facility, such as increasing the frequency of data collection for troublesome assets or monitoring assets in remote locations. Just relieving the maintenance engineer of the data collection chore saves time, freeing up the maintenance engineer to focus on more important problems. That said, industrial environments present a unique set of challenges for wireless deployment.
The biggest change to this landscape has been the proliferation of wireless vibration data collection systems, which started appearing on the market 15 years ago. There has been an explosion of options as more and more vendors bring solutions to market. Wireless data collection systems have been deployed with increasing numbers in various facilities with the promise of increased vibration measurement flexibility, remote data collection and analysis. With the increased experience deploying systems have comes an increasing awareness of system capabilities and limitations.
What is the maintenance practitioner looking for?
In a recent survey, maintenance practitioners were asked about IoT for Condition Monitoring: what you were looking for in a vendor, what problems a wireless data collection system might address in your facility and what concerns were holding you back from spending the time, energy and money on a test or pilot deployment.
Figure 1. A survey was conducted by the Mobius Institute between January and May 2022, sponsored by The Machine Instrumentation Group. There were 977 respondents worldwide representing various roles and industries within the maintenance and reliability community.
With the proliferation of systems from vendors with a variety of backgrounds and competencies, there has also been an increase in confusion, with some lingering questions and concerns about what to expect from a wireless vibration measurement system today. Networking options, vendor pedigree, diagnostic tools and data processing, the performance of the accelerometers and battery life are all questions that arise as we assess the available options — a situation that continues to change as more systems get evaluated and deployed, adding to our knowledge base of the maintenance and reliability eco-system.
Networking in the Industrial Environment
One of the first things to notice about wireless vibration systems is that although they are generally self-contained networks with complete IoT software stacks, they have numerous I/O options and destinations for the data. Sure, there are some mobile apps to present data dashboards to the maintenance professional on the go, but the interest in diagnostic tools, as well as the preference for the availability of raw vibration waveforms, complicates data analysis and presentation by a system dashboard.
Many vendors offer vibration collection and analysis as a subscription-based SaaS model. Others will deliver raw data for analysis (hopefully with your existing tools). A few systems provide traditional industrial interface connections for integration with the OT system, at field or operational level, sending processed vibration signals to a PLC or DCS, much like a traditional velocity transmitter. In all cases, the end users must decide what kind of data they require, who will use it, as well as where and how to access the data in order to select the system with the features that best fit their needs.
Figure 2. Wireless vibration data collection systems today offer a variety of communication options, signal processing, and data management. The best fit should be determined by the needs of the end user based on the existing facility networks, diagnostic tools provided, changes to workflow and existing maintenance competencies. Image source: The Machine Instrumentation Group.
Wireless CBM Vendor Positioning (and AI)
Painting with a broad brush, wireless vibration vendors fall into two broad camps: those with a PdM background who have added wireless systems to their product and service offerings, and those more oriented to software, AI and IoT, who have added vibration expertise to their competencies. For the former, wireless data collection may be an upsell; for the latter, CBM may be a new application added to an existing IoT portfolio.
Many vendors in the market are promoting an AI approach to diagnostics and automated alerts. Data-driven approaches to Predictive Maintenance (PdM) are a big subject, confused further by copious amounts of hype. It’s difficult to compare the effectiveness of automated alert generation or diagnostics for these systems, for which AI might include remote diagnostic labs (analysis by qualified SMEs) or rules-based algorithms. The latter favors OEMs or PdM service providers with a long history in the industry and possession of historical hardware or maintenance data. In any case, a pilot study to compare system results to current methods is a way to gain confidence in the system’s capabilities.
One aspect of data-driven approaches to machine health diagnostics that is not frequently discussed is the extraction of information from the data that could help expand fault coverage to anomalies not easily detected or diagnosed with existing measurement techniques. Often control process variables themselves can also be used to derive a single “Health Indicator” that is simple to trend and observe and, by training with machine learning methodologies, offers the potential for prognostics.
Figure 3. Machine Health Indicators can be modeled from various data sources to detect and trend emerging anomalies, extending asset fault coverage. In this case, factory automation (robotics) control signals were used to create new health indicator monitors to detect problems emerging with automotive manufacturing robot arms. Image courtesy of Predictronics Corp.
Enabling Sensor Technology
The vibration industry was fortunate in that the semiconductor industry that began developing MEMS accelerometers to trigger automotive airbags over 35 years ago turned its attention to industrial applications and, in particular, Condition Monitoring. The result was chip scale accelerometers designed and marketed for vibration measurement. This technology has been enabling for wireless vibration data collection systems, and for many good reasons. Chip scale MEMS accelerometers are low cost, low power and highly stable, with repeatable measurement over time and temperature. Most include a digital interface, making them easier to integrate into an IoT sensor system design, though very high-frequency response analog output accelerometers currently represent state of the art for performance.
Figure 4. The explosion in wireless vibration data collection products, particularly by enterprises new to Predictive Maintenance, has been largely enabled by MEMS accelerometers. Image source: The Machine Instrumentation Group.
One caveat is that with extensive product portfolios available from semiconductor vendors for a variety of applications, the performance of MEMS accelerometers designed into wireless vibration data collection systems varies greatly. If the maintenance professional is looking for a system capable of detecting an emerging bearing fault, the cause of the overwhelming majority of asset failures, then the system must be chosen carefully. Even if the specifications sheet shows a high-frequency accelerometer under the hood, testing is a must since many new entrants to this market have less experience with vibration measurement. In our experience, developing sensors with poor mounting techniques or mechanical design introduces resonances, limiting the linear frequency response.
Battery Life in the Industrial Environment
As the Predictive Maintenance eco-system gets experience testing or deploying wireless vibration systems, we are also getting more experience with an aspect of wireless systems that has not gotten much attention — battery life.
Battery life is a key wireless sensor specification that can be loosely specified and difficult to test. Much of the literature on this subject is focused on Electric Vehicle (EV) batteries, with less discussion of IoT sensors for industrial environments such as vibration-based Condition Monitoring.
Adding a battery change to the maintenance checklist may become significant when hundreds of sensors are deployed throughout a facility with a large footprint. The same incentives that led maintenance to consider deploying a wireless system in the first place — collecting vibration data from remote locations or hazardous environments, for example — are again considerations when the system alerts you to a dying battery. Although we expect that this trip will happen significantly less often than for the traditional data collection route, it would still be nice to schedule the “truck roll” with some confidence. Published specifications introduce uncertainties since battery life specifications often do not include necessary caveats regarding the operating conditions, such as ambient temperature and frequency of measurement or data transmission.
Why is this so — why is measuring and specifying battery life such an inaccurate science?
There are many factors making design optimization, estimation and specification of wireless sensor battery life a challenge: wireless architecture and protocol choice, environmental variables impacting battery performance, embedded signal processing, power management design, firmware efficiency and, of course, selection of battery size and technology.
Unlike other “smart” IoT applications with sensors that measure and periodically transmit a simple scalar value such as temperature or barometric pressure, vibration is a signal with an inherently wide frequency range. As such, transmitted data packets contain much larger amounts of information, which takes longer to collect, process and transmit. In addition, vibration signals are acquired at high sample rates with high digital resolution, with embedded processing that requires additional memory and power — all putting pressure on battery life.
Figure 5. Vibration measurement places demands on wireless transmission that impacts battery life. These plots are measurements of wireless sensor current consumption during transmission. On the left, a low-cost temperature sensor signals its presence and transmits a relatively small data packet via Low Energy Bluetooth protocol (BLE). On the right, a much more expensive wireless vibration data collection sensor, also using BLE, transmits a longer vibration waveform, consuming much more current from the battery during transmission. Data source: The Machine Instrumentation Group.
Of course, the selection of battery technology itself introduces complexities with variation in characteristics such as capacity, self-discharge rates, charge/discharge cycle times (if rechargeable) and optimal discharge current — all with heavy dependencies on environmental factors such as ambient temperature. The battery size (capacity) will be determined by wireless sensor definition and design to support the desired IoT features.
Figure 6. Battery capacity curves for a Li-Thionyl Chloride battery. Note the heavy dependence of the capacity, or stored charge, on both the average current draw and the operating temperature. Image Credit: Saft Batteries.
Summary
As the maintenance and reliability community gains experience deploying wireless sensors, we are collectively clarifying the many questions that arise from implementing such complex systems. With many of the technologies integrated into a wireless monitoring system relatively new to many maintenance and reliability engineers, adoption can be a slow and frustrating process. We encourage seeking the help of subject matter experts to accelerate the expansion of your wireless condition monitoring strategy.
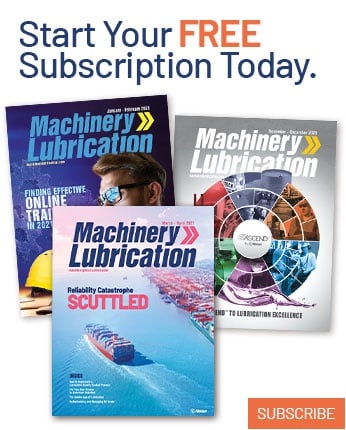