Leading reliability and maintenance improvements can be quite challenging. A behavioral change often needs to occur regarding daily work processes, preventive maintenance, materials management, root cause processes and much more.
Projects often run into the sand because the necessary structure wasn’t in place from the start. While being a part of reliability improvement projects over the years, I have noticed that there are specifically two important maintenance management pieces missing:
- No clear reliability goals
- No business case for reliability
Setting Goals for Reliability
When trying to improve reliability, it is important to have a clear view of the goals and a plan to achieve them. This may seem like a given, but I suggest that you ask yourself some questions or perhaps even do an informal self-assessment by asking people in your organization:
- Does our facility have an understandable, simple vision of what reliability is?
- Do we have clear and practical goals for improving reliability that the employees understand?
- Ask ten employees what our goals for reliability are. Will you get similar answers from everyone, including production, maintenance and construction?
- Does the goal have an execution date? Goals without dates are only a wish list.
- Is there an action plan in place to achieve the goals?
Designing a vision and goals that can easily be communicated and understood is not easy. There are many ideas on how it can be accomplished; I can share my own experiences that I’ve seen work. At IDCON, we follow some guidelines when we set up goals. They are:
- General words in missions eventually must be translated and linked to goals; that way everyone in the organization feels they can contribute.
- You must separate goals and activities. A goal may be to complete an activity, but they are different: an activity is something you do; a goal is a result.
- Goals should always have an end date and a person responsible.
- It's good if goals can be measured objectively.
How Many Reliability Goals Should I Have?
In our experience, you should not have more than two to three overarching goals. These two to three reliability goals are usually identical for all organizations that manufacture something: profit (of course), then output measured by units produced/time and cost by total cost/unit.
If you have more than three overarching goals, experience has shown us that you cannot remember what the goals are, and you lose focus on what's important. For example, if your organization has seven goals, how do you as an employee know which one is most important? What is the focus?
It is important that reliability goals fit in with the organization's overall goals. Hopefully, the overall goals are clear. If they are not, then you can fall back on the goal of generating profit.
For reliability and maintenance, the long-term goal for most organizations is to:
- Increase reliability
- Reduce total costs/production unit
Note: In my opinion, maintenance costs/production unit is not of interest as a goal. Total cost/production unit is how a company competes.
Create Reliability Goals with the Pyramid Method
The two goals we used as an example above are lagging goals (end results). How do we connect these to activities and sub-goals? A pyramid format has worked well for me. It is easiest to explain the concept through an example:
Ask these questions:
- Which processes help us increase reliability?
- What do you think will reduce downtime in the factory and reduce long-term costs?
Processes that improve reliability could be:
- Planning and Scheduling (perhaps we measure % break-in jobs)
- Preventive maintenance (perhaps we measure quality + completion %)
- Spare parts inventory (perhaps we measure value + stock-outs %)
- Root Cause Problem Elimination (perhaps we measure the value of solved problem)
- Well-trained craftspeople (perhaps we measure the number of recurring problems)
Then we have an image of the first level with overall goals and the second level with processes that will improve the overall goals. It may look like this:
Figure 1. Example of how goals can be built using pyramid thinking. The first level has the overall goals; the second level has the processes that will improve the overall goals.
Let’s continue building the next level use Preventive Maintenance (PM) as the example. PM can be effectively divided into:
- Mechanical inspections (during operation and downtime)
- Electrical inspections (during operation and downtime)
- Instrument loop inspections
- Instrument calibration
- Instrument physical inspection
- Lubrication
- Alignment
- Balancing
- Operating practices
- Cleaning
If we continue with, for example, lubrication (within PM), a goal could be:
- Goal: All equipment has the right amount and right degree of cleanliness of oil/grease.
- Measure: Can be partly measured by analyzing several randomly selected bearings and seeing how many have the proper documentation (quantity, type). Can be subjectively evaluated by evaluating lubricant storage, lubricant tools, filters and logic in the choice of cleanliness requirements.
The image now looks like this:
Reliability Goals Must be Connected to Activities and People with Deadlines
Employees typically have a review meeting with their manager. The goals and potential KPIs should be discussed in this meeting. It’s also important to connect these goals to the overall goals for the employee to understand how they contribute to the overall goal of the company. If you develop the goal with the pyramid method, you will automatically have this connection.
Working Method for Designing Reliability Goals
It is obviously important to get buy-in for the goals from the employees. One approach that has worked well for me is for management to determine initiatives down to level two or three. In short, management decides what needs to be improved. But you need to allow the employees to work out a proposal for how to do things and propose timelines and exact details of the goals. They develop a proposal for levels four and down.
Reliability KPIs
This article has discussed goals in general. Often, a goal is measured by using a KPI. Therefore, KPIs can be developed using the same approach. In our lubrication example above, the KPI may be the percent of equipment that has been reviewed for the correct lubrication. Here’s a great article about which KPIs you should consider and when to start using them.
Business Cases for Reliability
Making business cases for reliability can be done in many ways. I’ll describe a few ways to show the value of reliability below:
- Why do we need a business case?
Most plants see maintenance as a cost; it is, therefore, common for leadership to focus on maintenance cost as a separate entity. The practical consequence of this line of thought is that a maintenance manager may receive the order to reduce maintenance costs.
The problem is that maintenance cost is not a separate entity. A cost reduction without changing other work processes and/or skills often impacts production and safety. If a company uses too much electricity, do we cut the cable or try to reduce energy consumption by becoming more effective? No; a reduction of electricity supply will have other effects on equipment.
Which cost is important for a plant to improve?
- Maintenance cost/unit produced?
- Total maintenance cost?
- Total production cost/unit?
- Total production cost?
The most important cost is the total production cost/unit. All of the other examples are quite irrelevant. Total production cost/unit determines the competitiveness of a company, assuming the quality is the same for comparative companies.
Improvements in maintenance very often have an initial improvement impact on production cost and profit. Increased reliability will allow us to produce more products while fixed cost is constant, but the maintenance cost per ton may stay the same or even increase. If total production cost per ton is reduced and maintenance cost remains constant or increases, it is a win for the company.
It could be argued that maintenance cost or maintenance cost per unit produced is fairly irrelevant for a company and is only of interest if put in contrast to the total cost/ton.
If cost is reduced without any other significant improvements, we typically see the following cost development:
Figure 3. If cost is reduced without
any significant improvements in work systems,
skills or other improvements, cost is reduced,
but reliability quickly falters,
and cost will eventually go up again.
However, if the company’s focus is on improved reliability, the curve often looks as follows:
Figure 4. If a company focuses on reliability,
cost may initially go up — usually the maintenance cost,
due to the equipment needing repairs. But the cost
will be reduced once systems and practices
improve due to fewer repairs and less spare part
consumption, but mostly through increased production
with existing resources.
Many companies operate as described in figure 3. It is therefore important to be able to describe the financial impact of reliability — we will refer to this as a “business case” going forward.
IDCON has over 50 different ways of calculating the value of reliability since different companies have different production systems, sizes, cost structures and accounting methods. What follows are some of the most common ways to calculate a business case.
2.The value of reliability business case example 1 (Paper Mill 1)
This business case is easiest to use if a company operates 24/7 and can sell all the product it makes, but it can be used in other cases as well (with some slight modifications).
The goal is to calculate the value of a 1% increase in reliability from a bottleneck in the plant. Where the bottleneck is located is not necessary to know since we know the total annual production of the plant.
If we improve reliability, we will increase the output of the plant by 1% using the existing recourses available. This means that the fixed cost remains the same but that the variable cost will increase by 1% when we increase production by 1%. The profit increase of one incremental unit of sales is, therefore:
Sales price – variable cost = increase in profit (contribution to fixed cost).
For example, if we make paper and produce 1 ton more paper due to improved reliability and the sales price is $600, and the variable cost is $350, then:
$600 - $350 = $250/ ton (additional profit).
Knowing this, we can calculate how much an increase in reliability is worth for the plant.
Let’s assume total production is 500,000 tons. A 1% increase in production is 5,000 tons, meaning, we produce 5,000 tons with the same fixed cost, but we have to pay variable costs. The increase in profit from a 1% improvement in reliability, also called contribution to fixed cost, is:
5,000 * $250/ton = $1,250,000 annually
Summary of the formula:
1% * total production volume/year * (sales prices – variable cost) = increase in profit/year
Summary of the calculation
Remember to review the assumptions above and realize that some estimations of future sales prices must be made.
3. The value of reliability business case example 2 (Paper Mill 2)
Another way of calculating the value of reliability is to use the DuPont model. The DuPont model describes changes in results (and return on investment (ROI)) using a graphical interface, making it easier to visualize multiple changes. The calculations are similar to the model used above, but there are a few more variables added in order for the reader to envision how multiple changes in a calculation can be simulated.
The DuPont model (excluding the ROI portion) is shown in Figure 5 and describes a similar situation as business case 1; we use slightly different numbers for our example, and we present the numbers in the DuPont Model.
Figure 5. The partial DuPont model graphically describes the variables in a business case.
Let’s assume a paper mill produces 500,000 tons/year at a sales price of $600/ton and runs at a reliability (measured by overall production efficiency (OPE)) of 88%. The mill sells paper for $300 million per year. The variable cost is $380/ton, which adds up to a total cost of $190 million. The contribution to fixed cost is, therefore, $110 million. Let’s assume a fixed cost of $92 million. This would lead to a result of $18 million/year (profit). The starting point for paper mill 2 is represented in figure 6.
Figure 6. The partial DuPont model with numbers for paper mill 2.
In this business case (represented in figure 7), we assume we can increase reliability by 6% and that maintenance costs would go down by $5/ton after a few years due to our efforts. This means that the total sales would go up to $320 million, and our variable cost per ton would go down to $375/ton (reduction in maintenance cost), but the total variable cost would go up since we are producing more paper:
534,000 tons * $375/ton = $200,000,000
Figure 7. The partial DuPont model describes an increase of 6% in reliability and a $5/ton reduction in maintenance cost
Most companies (at least those listed on the stock exchange) would look at ROI. If we assume paper mill 2 has liquid assets (cash, liquid investments) of $75 million and fixed assets of $280 million (buildings, machines etc.), the ROI would be 8%. See figure 8.
Figure 8. The partial DuPont model calculating ROI for paper mill 2.
The DuPont model can be used to simulate many different scenarios by changing the variables in the model. To describe one more case, it may be of interest to see what happens to paper mill 2 if we increase the sales price by 10%. Figure 9 shows the change in sales price, result and ROI.
Figure 9. ROI for Paper mill 2 with an increase in sales price by 10%.
4.The Value of Reliability on a single piece of equipment/system
A single piece of equipment or a system can be maintained by three different methods.
The first method is Condition Based Maintenance (CBM), which means that the condition is monitored, and when the condition reaches an unacceptable level, the corrective maintenance action is executed. The second method is Fixed Time Maintenance (FTM), which means the equipment is overhauled or exchanged at a fixed interval, regardless of condition. The third method is Operate to Breakdown (OTB), which means we operate the equipment without any preventive action until it fails.
Adding the maintenance cost, downtime cost and the cost for damages, one can compare the cost of each of the maintenance methods. There are many other variables that can be added, such as spare parts inventory cost, the risk for injury, environmental damage etc. But for our purposes, the three most common and usually largest costs have been used.
Let’s assume we are trying to decide the most cost-effective maintenance method for the bearings in a centrifuge (Figure 10).
Figure 10. Centrifuge with two bearings.
The downtime cost (DTC) for the production line is $10,000. The cost of the bearings is $600 each. History shows (or we estimate) that the bearings fail every five years (0.2 failures/year). When the bearings fail catastrophically, the screen is damaged every other time, and the cost for the screen is $50,000. The labor cost is $50/hour. It takes 12 hours to change the bearings in an unplanned fashion and eight hours in a planned fashion. Each change requires four people. The process requires two hours of start-up time. The calculation is shown in Appendix 1, Figure 11.
The calculation does not have all possible variables and combinations; it is merely an example to show how a calculation can be made to compare different maintenance methods and their cost. As an example, it can be mentioned that the DTC may not be zero at CBM or FTM. But the use of the calculation may add estimates for those circumstances and others.
5. Conclusions
There are thousands of ways to calculate the business case for reliability — a few have been described in this article. Other examples include:
- Reduction in spare parts
- Reduction in materials
- On-time customer delivery
- Quality improvements
- Labor effectiveness
- Overtime reduction
- Contractor usage
- Etc.
Appendix 1. Consequence of break down analysis.
Figure 11. Consequence of Breakdown analysis.
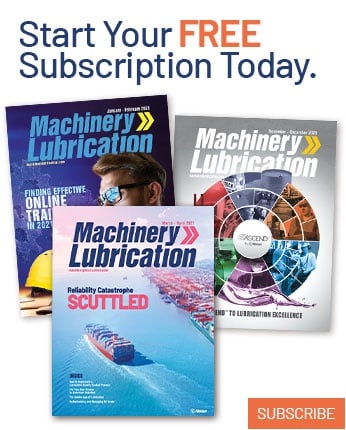