While the industrial world may be in the midst of a volatile period with much economic uncertainty, maintaining the core of its current workforce is critical for capitalizing as the economy recovers.
In previous downturns, firms such Engineering, Procurement and Construction companies that design and build complex energy and chemical plants, cut personnel deeply to quickly align costs to reduced revenues. These cuts ultimately undermined their ability to successfully pursue and execute new projects as capital spending picked back up. But these cyclical trends underlie a larger, looming issue: there is a large segment of skilled industrial workers who are close to retirement age, and the need to retain and transfer the experience and skills of those workers is on the minds of many executives.
According to McKinsey, skilled-labor shortages have become a major issue in several markets, and retirements will drain talent. For example, about 41 percent of the current US construction workforce is expected to retire by 2031.
To ensure the long-term viability of their workforce, firms need to prepare for the future by continually enhancing the skills of their employees and move forward aggressively with digital transformation programs that support knowledge transfer and re-use through the organization. Those two measures will help firms cope with future disruptions that, at this point, seem inevitable and part of the new normal.
Disruption: Good for differentiation
One of the most obvious disruptions to the workforce over the last several months is the shift to remote work as well as the way they work, with increased enforcement of social distancing measures. While, in the industrial plant, only some workers can do their jobs effectively while working remotely, the organizations that were able to quickly pivot to remote work, or adjust working conditions for plant workers not able to do their jobs at home, will come out stronger from this uncertain time.
Being agile as a business and preparing for the future are two major differentiators that can not only set an organization apart from its competitors but also can attract and retain talent. How an organization reacts to major disruption is always a good indicator of how it might handle any change, in any situation. Working for an industrial company that has the agility to adjust to an increasingly complex and uncertain world will aid in both retaining key talent and in recruiting the digital natives needed for the future.
Many of the executives now at the helm of industrial firms have accumulated significant experience in managing through previous downturns and are well positioned to provide sound leadership. Being assured that an organization will make the appropriate shifts to adjust to new realities, without compromising the firm’s core capabilities give employees confidence that they will remain competitive in the future.
Continuous Learning is Now Mandatory
If the industrial world wants skilled talent, it may have to develop that talent in-house. Technology completely revamps industrial organizations and the way they operate, but it also continually undergoes rapid change. The skills plant operators or engineers needed to possess just a few years ago might look entirely different today. This rapid pace of change is one of the reasons that the industrial world can never stop enhancing the skills of its workforce.
Modern continuing education, especially in the industrial segment, needs to encompass more blended learning to be effective. Expert-guided learning in a classroom can certainly be a good option, especially if there is a local university or college that can partner with an industrial organization to create a curriculum for workers to gain new skills and experience. In addition to that, if an industrial company’s technology vendors offer specific certification programs in leveraging their technology or processes, it is important to have workers get certified in that, to ensure the technology is being used correctly and that workers are getting the most value that they can out it.
Technology will play a key role in keeping skills sharp. For example, operator training simulation software can let workers experience real-world plant scenarios through simulation, so that their choices, decisions, and mistakes in that simulated environment do not have actual consequences. It helps them learn in ways that would not be possible in the real world.
Attracting New Talent
Younger workers have, in many cases, relied on technology to streamline many aspects of their daily lives for quite some time. They naturally have expectations that they will be able to leverage technology in their work lives, too, to streamline work where possible.
Firms that adopt new technology, like artificial intelligence and machine learnings, to reduce tedious, low value tasks for younger employees will stand out and have an edge when recruiting for the best talent. It is as much of an incentive to join or stay at a company as other more common perks.
Also, as younger generations joining the workforce place increasing focus on environmental sustainability and corporate responsibility, more than any time in history, artificial intelligence-enabled technologies that support “greener” operations within the plant lifecycle can help attract that talent – they want to work for environmentally-conscious organizations.
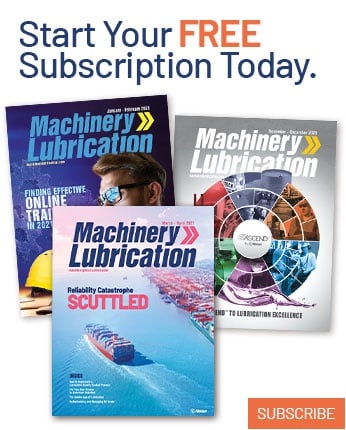