The need for skilled labor is an escalating concern for manufacturers. That concern is fueled by a low unemployment rate making it harder to find workers, as well as the reality that new skills are needed compared to the manufacturing jobs of even a decade ago. As digital tools and technology have become embedded in manufacturing – a transformation sometimes referred to as Industry 4.0 – it has necessitated a shift in the skills required to be successful.
Skills initiatives are one type of workforce training program some manufacturers are turning to as a solution. These initiatives encompass a wide range of programs but are often styled as apprenticeships and fit under the umbrella of STEM (science, technology, engineering and mathematics). Across the country, community colleges and even some high schools have developed skills initiatives that can help companies find and train the talent they need. In addition, some companies have created their own skills initiatives, sometimes in cooperation with community colleges. By working with local educational institutions and government officials and following best practices in employment law, manufacturers can maximize the benefits of these programs.
Background on Skills Initiatives
The apprenticeship model for these programs comes from Germany, Switzerland and Austria, where a vastly higher percentage of the workforce goes through apprenticeships. It is a dual education concept: workers get practical, hands-on training in the company while they also study. Students generally will be paid during the program to study and work, but if they complete the program, they also will receive a job offer. This makes it extremely valuable for both the company and the workers. The workers get a clear path to a new career, and the company gets a pipeline for the skills it needs.
Parts of the Carolinas and other Southeastern states adopted this model, as a growing concentration of German, Swiss and Austrian companies established operations in the region, and it has since spread around the United States. You can find similar skills initiative programs in New Hampshire, Michigan and Arizona, to name a few examples. Efforts are also underway in various states to expand these programs, usually in coordination with community colleges and even high schools.
Finding or Creating a Skills Initiative
The first step manufacturers can take is to reach out to their local community colleges to see what programs may already exist. If the area community colleges are not offering a suitable program, companies should talk to college officials about their interest in partnering to construct a more appropriately tailored program.
In particular, companies looking to build a new facility or expand should consider this approach. Frequently, states will provide support for a skills initiative that helps a locating or expanding company create skilled jobs. After all, two of the main goals of most state economic-development offices are to create jobs and to increase and elevate the skills of their workforce.
Companies may also consider banding together with other manufacturers who have similar needs to develop a mutually beneficial skills initiative. These efforts create a network that both demonstrates the need for the program and benefits from it.
“Networks are very useful, in particular for small- and medium-sized entities or SMEs,” says Johann Fortwengel, an assistant professor at King’s College London who studies German-style apprenticeships in the United States. “But even for big companies, it might make sense to use such a network approach with their smaller sites where they do not need as many apprentices.”
According to Fortwengel, the next question is: how do you organize and manage it? His research shows the importance of maintaining some flexibility in the model and adapting it to each company’s needs at its U.S. facilities.
Employment Law Considerations
Manufacturers must be mindful of federal and state wage and hour laws that may impact skills initiatives. There can be a misconception that if it is just training, a company doesn’t have to pay for it. But the rules aren’t black and white, and they vary from state to state. Accordingly, companies should seek legal guidance before deciding how to structure pay and benefits for these programs.
Companies should also think about skills initiatives as tools for attracting not just better talent but also more diverse talent. Hand in hand with that, manufacturers should ensure they are providing these initiatives on an equal opportunity basis. The broader the pool of potential candidates, the better.
Avoid undue reliance on “word of mouth” to find candidates and don’t limit the pool of potential candidates solely to those just beginning their working career. Community colleges are a natural fit in this regard, as they retrain many people who are seeking a second or even third career. Likewise, in deciding which community colleges or high schools to partner with, consider their demographics in addition to their technical expertise.
More Than Manufacturing Skills
Lastly, companies should not limit themselves solely to the nuts and bolts of their manufacturing operations when they think about skills initiatives. Manufacturers also commonly mention “soft skills” as a challenge for their workforce, and some programs incorporate aspects such as problem-solving and creative collaboration. These often fit under the umbrella of STEAM (science, technology, engineering, arts and mathematics.) There also is a small but growing trend toward other skills training programs that move beyond the technical manufacturing skills to include areas like finance or information technology (IT). These types of programs can be a beneficial tool to help certain members of a company’s team diversify their skill set.
These are just a few of the ways manufacturers can benefit from skills initiatives. By partnering with community colleges, seeking support from state government and applying best practices in employment law, these initiatives can help companies build and maintain their workforce of the future.
About the Authors
Al Guarnieri co-leads Parker Poe’s manufacturing and distribution industry team. He is an attorney with more than 30 years of experience in international business, site selection and economic development. Al can be reached at alguarnieri@parkerpoe.com.
Stacy Wood is a partner on Parker Poe’s manufacturing and distribution industry team. She has been defending manufacturers and other employers for more than 25 years, with a focus on discrimination, harassment and Employee Retirement Income Security Act (ERISA) litigation. Stacy can be reached at stacywood@parkerpoe.com.
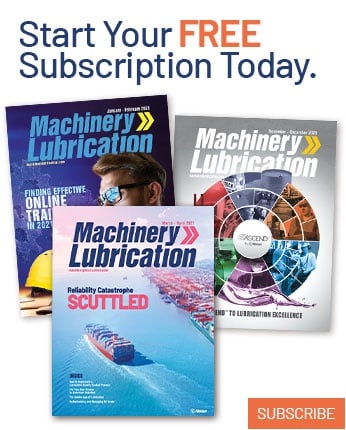