Nowadays, everyone is environmentally conscious. Across the country, recycling programs have become quite popular. Manufacturing facilities often have the greatest recycling opportunities. Statistics have proven that the bigger the facility, the bigger the payback. Indeed, most of the waste material that is generated and discarded in the manufacturing process can be recycled and reused.
Below are seven types of manufacturing waste:
Waste of Transport
Moving products from one place to another is wasteful. It adds no value to your products and takes money out of your pocket. This waste is expensive, as you need both vehicles and manpower to transport your goods.
Waste of Inventory
Any unsold product has a cost, which you must bear until it is sold. Inventory must be stored, which requires space, packaging and transportation. Your inventory also has a chance of being damaged during transport. Waste of inventory hides many other manufacturing wastes.
Waste of Motion
These are unnecessary movements by both man and machine. This would include stooping down to pick up heavy objects at floor level when they could be fed at waist level to reduce stress and retrieval time. Excessive travel between workstations and machine movements from the starting point to the work point are all wastes of motion. These motions cost you time and money, as well as cause stress to employees and machines.
Waste of Waiting
We spend a lot of precious time waiting for things in our working lives, which is an obvious waste of time. This is also one of the more serious of the seven wastes of lean manufacturing.
Waste of Overproduction
Manufacturing way too early or in excess is the most serious and wasteful type of waste. It usually occurs as a result of long lead times, oversized batches and poor supplier relations. Your goal should be to manufacture only according to the demands of your customers, which borrows from the just-in-time (JIT) philosophy. Unfortunately, most companies tend to borrow from the philosophy of just in case.
Waste of Overprocessing
This is when inappropriate techniques, oversized equipment and lack of proper skills are used in production. All of these cost time and money, as well as lead to excess production of poor-quality products. In lean manufacturing, small is preferred, so consider using smaller machines based on demand.
Waste of Defects
This is the most visible of the seven types of waste, but it is not the easiest to catch before reaching consumers. In terms of quality, defects tend to cost more, as every defective piece needs a replacement or repair, which wastes materials and time. Waste of defects should be kept to an absolute minimum. Trying to detect them afterward will be both costly and time-consuming.
8 Effective Waste Reduction Techniques
- Create regular, systematic waste-reduction audits to find all possible areas where waste can be reduced.
- Maintain your audit records diligently. Set waste-reduction goals with an allocated budget.
- Assign responsibility to individuals to correct problematic areas along with a clear hierarchy for work to be performed.
- Involve all personnel so not only will they know what's happening but also so the waste-reduction efforts are carried out collectively.
- Establish regular, ongoing training and education in waste reduction to promote awareness and understanding.
- Reward and publicize any waste-reduction efforts by employees.
- Audit vendors on a regular basis to ensure that you receive minimal defective goods and services.
- Bring in trained professionals from outside your company to review your entire system and its processes. An outsider's perspective will give you insights and suggestions that you may have missed.
Recycling in manufacturing processes can be difficult to implement, but the benefits to your business and environment are undeniable.
About the Author
Erich Lawson is passionate about saving the environment through effective recycling. He has written a wide array of articles on how modern recycling equipment can be used by industries to reduce monthly garbage bills and increase recycling revenue. To read more about environment-saving techniques, visit the Northern California Compactors blog.
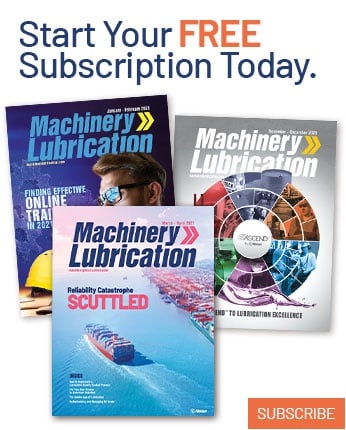