
Regardless of the work environment, there will always be some tasks that have an element of risk. Some carry an obvious risk, like working with dangerous goods and machinery. Others may not be as obvious and will require clear safety guidelines. In each situation, employees must be aware of their surroundings and know how to avoid possible hazards while performing their tasks. Employers must ensure education and compliance.
Following are four frequently overlooked practices that should be considered for every workplace safety plan.
Hydration
A dehydrated worker can result in a multitude of physical issues, including fatigue, dizziness, weakness, confusion and fainting. Even the mildest form of dehydration can affect productivity, but what's worse is that it can also lead to heat stroke or more serious cardiac implications.
If you have dehydrated employees, they not only are a danger to themselves but also to everyone on the worksite. Dehydration can result in slower reaction times, similar to someone who is inebriated.
Employers must insist that their employees take regular water breaks to rehydrate throughout the day. This includes providing access to fresh drinking water. Educate personnel on how much water they should be drinking. Those who are aware of their water intake are less likely to become dehydrated.
If your workers must be in extreme heat or conditions that require plenty of hydration, it may also be useful to supply items like water bottles.
Stress Management
Most jobs have some degree of stress, but if it becomes excessive, it can interfere with productivity and impact the staff's emotional health. Among the things that contribute to workplace stress include working long hours, not taking proper breaks, unrealistic targets or deadlines, job insecurity, conflict and bullying.
Employers can reduce stress in the workplace by identifying possible hazards, assessing the risks and implementing ongoing solutions. It's important to have a process in place for reporting work-related stress issues. Personnel should be provided with adequate training and be encouraged to report work-related issues with confidence that they will be resolved.
Manual Handling
Studies show that one in three workplace injuries is caused by improper manual handling. This can involve everything from lifting or carrying heavy loads incorrectly to pulling, pushing and holding things improperly. Risk factors include working in a static posture for too long, cramped workspaces that promote uncomfortable postures, performing the same task repeatedly and lifting heavy objects from awkward locations.
If this is an issue at your site, consider making changes to your workplace design. Walk through your plant and review potential hazards. Communicate with employees regularly to identify the risks and ensure that you are constantly monitoring and updating them.
Minimizing Distractions
Distractions are a major danger to workplace safety and one of the leading causes of injuries. The most common distractions involve fatigue, mobile phone use and headphones/listening to music. Although you can never fully eliminate workplace distractions, you can minimize them. Workers should take adequate breaks throughout the day to stretch and recharge. Implement policies for mobile phone usage, especially if employees are operating machinery. The same goes for listening to music with headphones. Music should not block you from hearing what is occurring in the workplace.
By focusing 100 percent on the job and applying these safety practices, you can make your worksite safer and more productive for everyone.
About the Author
The team at The Temporary Fencing Shop are specialists in temporary fencing products and crowd-control barriers across Australia.
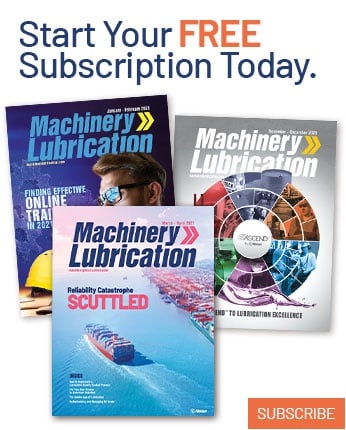