Light-emitting diode (LED) lighting is quickly becoming the new standard for industrial illumination in facilities around the world for its energy efficiency and long-life performance. With a multitude of forms to fit almost any application, including hazardous locations, thousands of plants have made the switch from conventional high-intensity discharge (HID) lighting to solid-state LED technology, racking up hundreds of thousands of dollars in savings each year.
But beyond the energy and maintenance savings, perhaps the greatest advantage of LED technology is its potential for future innovation. Unlike HID, which hasn’t evolved substantially in more than 10 years, LED technology is evolving rapidly, with continuously improving lumen output, lifespan and performance. In addition to these advances, LEDs offer a technology platform suitable for a multitude of other innovations beyond lighting alone, which can contribute substantially to overall plant productivity and efficiency.
For any facility that has not yet made the switch, the following innovations may convince you it’s time.
Smaller, Lighter Fixtures
LED lighting has a reputation for being a bit bulkier than conventional HID fixtures, although the light-emitting diodes and optics in most LED fixtures are fairly compact. LEDs are simply a phosphor-coated semiconductor chip packaged with some electrical connections and a dome. However, the LEDs must be combined with heat sinks, a power supply and other components to make up a complete fixture. Fortunately, design innovations are occurring in optics, thermal management, mechanical design and electronics design. As innovation continues, fixture designs will become smaller, lighter weight and easier to handle, making them much faster to install.
New Standards and Specifications
While the current LM-80 standards characterize the lifetime of LEDs, there is much more to an LED fixture than the light-emitting diodes. If the paint, finish, power supply and control circuits don’t last just as long, the fixture will still fail. New standards are emerging to characterize these other fixture elements that will streamline the purchasing process. These industry-wide standards will make it easier to compare one manufacturer’s product against another, allowing faster decision-making. For plant managers, this means less time sorting through product specifications and more time getting the lights up to start reaping the benefits.
Sensors for Granular Control
Thanks to their instant-on capability, LEDs are ideal for the application of lighting controls, such as occupancy sensors and dimmer switches, which adjust the light automatically for maximum efficiency. Daylight harvesting sensors are also emerging. These sensors adjust the light automatically as ambient daylight changes, using only as much artificial light (and energy) as necessary to maintain required lumen levels. The ability to integrate these controls into existing industrial automation solutions means facility managers can adjust and optimize lighting behavior and performance within a single dashboard, saving time and providing a simpler, more convenient user interface.
Monitoring Performance
The most advanced LED systems come with enterprise monitoring software to help plant managers stay on top of every fixture’s performance, remaining life and maintenance needs. This total visibility eliminates surprises, enabling preventive maintenance to be scheduled and performed at ideal times rather than in emergency situations that cause production impacts. The fact that LED lights can already accommodate occupancy and other sensors also makes them ideal for monitoring a host of other activities to gather vital business intelligence. For example, occupancy sensors can be used to monitor traffic patterns inside a warehouse to spot and help resolve bottlenecks. Visual sensors could easily be added to fixtures that would monitor inventory levels and other volumetric measurements. Environmental sensors can help keep tabs on temperature, humidity and other atmospheric conditions. These capabilities turn the lighting network into more than just a visual aid. It becomes a critical link in total plant operation.
Lighting as a Communication Hub
With power and wireless communication nodes available onboard every light, a lighting network can easily be transformed into a plant-wide communication network. Devices like high-definition cameras and other sensors could also be connected to improve plant security, safety and visibility. The network could even be used to backhaul data from production equipment to centralized automation systems. Eventually, an emerging technology called Li-Fi, which uses the visible light spectrum to transmit data, could make the need for wireless nodes at each fixture obsolete. All of this "double duty" being performed by the lighting network means less equipment, hard wiring and management burden for the information technology department, allowing more resources and personnel to be directed toward mission-critical or competitive advancements.
Aside from just a lighting solution, advanced LED fixture networks can become an integral part of your plant’s productivity, reliability and efficiency. So before you send out your crews for yet another routine change-out of your HID light bulbs, ask yourself if your lights are working as hard for you as you are for them. If not, perhaps it’s time to invest in lighting that adds to your bottom line.
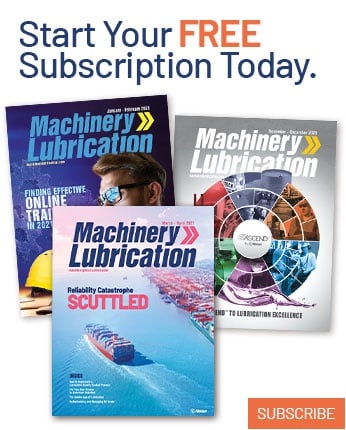