Just to survive today, companies have been forced to figure out their quality issues. Production of a consistent, high-quality product is the bare minimum just to stay in the game. However, to compete on the world stage, much more is needed than simply consistent high quality. It also requires being able to deliver the full amount ordered on time and at the lowest possible cost. That’s world-class manufacturing — quality, delivery and cost all combined to keep a facility competitive in a global marketplace.
The challenge in North America is to overcome many of the geographic differences that drive costs inherently higher. While North American companies work hard to do more with fewer resources, they need to take advantage of technology, innovation and a relentless attention to all aspects of their business in order to stay ahead and compete.
Manufacturing is a series of processes that must work together seamlessly in order to consistently produce high-quality parts on time and at the lowest cost possible. A “process” can be defined as a series of actions or steps taken in order to achieve a particular end. It’s the consistent repetition and refinement of these processes that allows a company to reach world-class status. For an efficient and ever-improving process, three critical elements are necessary: specialized expertise, robust systems and focused execution to keep the process in control and improving.
Specialized expertize relates to the process itself. This includes knowing the key performance indicators, how quickly they are changing and what their combined impact will be on process performance and total cost.
When it comes to your systems and specialized tools, keep in mind that an optimized process needs to repeat. It must be sustainable and robust over time in order to ensure it is executing on its objective consistently. It also should take advantage of the latest technologies in order to keep getting better and more cost-effective.
Finally, focused execution using data-driven, timely implementation can adjust the process to minimize variability and drive continual improvement.
Any process within a manufacturing operation that does not have one, two or all three elements is defined as “non-core.” Factories need to know their focus, the aspect of their operation that makes them significantly better than the norm. Once they understand their core competencies, it becomes easier to recognize which processes fall outside their expertise, existing systems and/or focused execution.
Combining these elements into a mindset allows companies to identify, optimize and then integrate their processes as they work to lead the race to set world-class manufacturing standards.
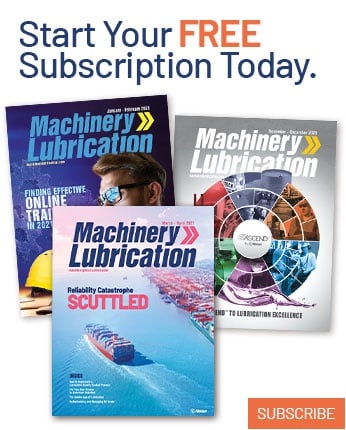