Today, the demands on manufacturers are driving an unprecedented rate of change, innovation and agility. Organizations must seek new ways to unleash the power of data that has traditionally been locked up in silos. Many manufacturers are turning to the industrial Internet to transform their operations through the use of data and analytics, but their ability to access data in a consistent and meaningful way has been a challenge.
By leveraging the industrial Internet, manufacturers can use the real-time production data they collect, analyze it, gather insight and make adjustments to increase uptime and efficiency in operations.
Get Connected to Critical Data and Information
Consistent and accurate data collection is the most critical first step of improving overall performance. You cannot monitor what you cannot measure, and you cannot compare and improve if you do not get started.
For manufacturers, the initial phase is to connect their assets and begin creating the digital thread they need to pull data throughout their organization. For example, a manufacturer can start monitoring the operational issues that affect production efficiency. This digital thread will show them how many products they actually produced versus how many products they should be producing in order to meet customer demand. Just as important is a simple and consistent way of viewing the data. The data must be organized in a manner that is simple and straightforward to understand and visualize.
Get Insights to Make Intelligent Decisions and Take Positive Actions
With high-level connectivity and visibility, you can then analyze and interpret the data by drilling down to see trends or patterns of incremental improvement or identify issues that might not be noticeable in isolation but are magnified in aggregate.
It is not about gathering data that optimizes one particular machine, but rather the connectivity of the manufacturing process to gather insights across a production line or plant. This enables plant leaders to correlate disparate types of data and use out-of-the-box technology solutions to display and report on that relevant data in real time. Then, manufacturers can make the right decisions to increase throughput, minimize waste or reduce disruption in their operations.
Get Optimized to Achieve Operational Excellence
Next, it’s time to utilize the insight gained from the data to achieve the best possible results. This includes uncovering areas for improvement and prioritizing and mapping those to larger goals or key initiatives. Optimization is realized when you can perform most efficiently and effectively using minimal resources and ensuring more reliability and predictability in meeting goals.
This is where the cloud, manufacturing intelligence systems and software as a service (SaaS) come in to analyze the data in order to make decisions and improvements so operations can be more efficient. For example, a plant leader may notice that employees are working a lot of overtime and discover the problem is not that the people are slow or inefficient workers but that the machines or materials they need to do their jobs are not available when they need them.
Empowerment is Key to Machine Health
Fitbits have gained in popularity because they enable consumers to easily monitor, measure and compare personalized health information. They empower users to take control of their health. Similarly, the industrial Internet is enabling plant leaders that same opportunity to gain intelligence, connectivity and empowerment to achieve manufacturing excellence.
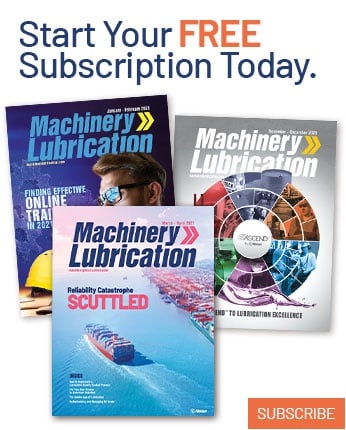