Every day warehouse workers are exposed to unique hazards, including falls from dangerous heights or varying severity of injuries caused by the misuse of heavy machinery. The list of potential accidents is many, and as a result, warehouses have come to be known as one of the most hazardous work environments.
However, adequate safety measures are available to ensure your workers steer clear of danger. Below are five crucial safety items that should be used in your warehouse.
1. Labels and Signage
Warehouse employees can more effectively protect themselves if they know exactly what they are working with. Everything in your warehouse, from machinery to crates, should be clearly identified. Labels should indicate the contents of a box, its destination and any other useful warnings. Some labels indicate appropriate storage temperatures or provide safe handling instructions.
Likewise, every area of your warehouse should be identified with proper signage. Signs should indicate who does and does not have access as well as communicate where smoking is or is not permitted. Vehicle traffic should be clearly designated along with warnings concerning flammable and/or hazardous materials. Directional signage should denote fire exits and help to locate fire extinguishers.
2. Guard Rails and Anti-Slip Tape
Falls are relatively common in a warehouse. Employees can fall from lifting equipment or from high storage ledges. With so much open space and elevated storage, workers must be protected against falls of all kinds. A warehouse should be thoroughly inspected for potentially dangerous areas that put employees at risk so those areas can be properly labeled.
Just as important are the barriers that physically prevent workers from falling. Guard rails are a primary piece of safety equipment that can save lives. They should be placed in any area of your facility where falling is a risk. A similar cause of injury is slipping. Be sure that stairs, ledges and inclines are lined with anti-slip tape. Also, use safety mats for an additional measure of safety.
3. Personal Safety Gear
Warehouse employees should be well-protected from head to toe. They should be safe from impact, and in some instances, protected against chemical burns. Personal safety equipment can and in many cases should include helmets, face shields, eyewear, ear protection, respiratory protection, gloves, vests and kneepads.
General ergonomics is also important for workers responsible for moving heavy loads and operating heavy machinery. Industrial floor mats with impact-absorbing features can reduce the strain on warehouse employees' knees, ankles and shins. All workers should also be trained in proper lifting that does not put undue pressure on their backs. Give employees the freedom to seek assistance when needed, and be alert to their endurance limits.
4. Lockout/Tagout Systems
It is becoming more common for all industrial workplaces — warehouses included — to utilize lockout/tagout systems and policies. Lockout/tagout refers to safe practices that allow a machine to be disabled when needed in order to prevent unwanted access. Various lockout/tagout products, such as group lockout devices, block access to electrical equipment.
Many devices effectively stop a machine from starting in the first place so machinery can be safely serviced. The U.S. Department of Labor's Occupational Safety and Health Administration (OSHA) outlines several steps a warehouse can take to fully comply with lockout/tagout.
5. First-Aid Kit
All workplaces should be equipped with a comprehensive first-aid kit, and warehouses certainly are no exception. Because of the greater likelihood of workplace injuries in warehouses, it is recommended that these facilities have multiple kits and that they be easily accessible. Considering the size of some warehouses, the kits should also be portable.
Your first-aid kit should include a wide range of equipment, such as bandages, adhesive tape, pads, ammonia inhalants, a cold pack, antiseptic wipes, eye wash, aspirin, burn spray, cotton applicators, gloves, scissors and tweezers. Of course, each kit should also have thorough user instructions. As a precaution, employees should familiarize themselves with the contents of the kit and know how to use it. Similarly, they should know when to alert an ambulance.
About the Author
Jerry Matos is a product specialist at Cherry's Material Handling, which offers material handling equipment from industry-leading manufacturers including machine dollies, toe jacks, pallet trucks and more.
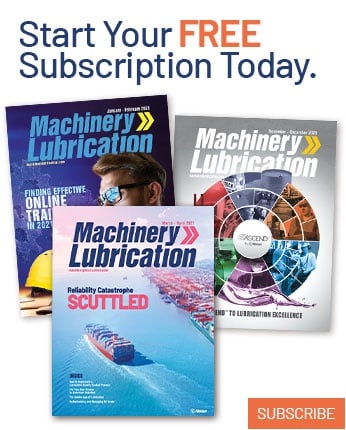