Around the world, the aim is the same — to produce a product as cost effectively as possible, to deliver it to the customer as quickly as possible and to do it with as few impediments as possible. Often, the weak link in the chain is the same as the strength: people.
In order to increase the productivity of the people involved and to minimize risk, business has turned to process. One such process, lean manufacturing, is a methodology originally developed by Toyota to increase efficiency within its plants. Since then, lean production philosophies have worked their way into many facets of management through lean thinking principles. Lean thinking can now be found in fields as diverse as software houses and the building industry.
Branching Out
In the same time frame that Toyota was developing lean, Motorola was creating a methodology that became known as Six Sigma. It found wider acclaim in the 1990s when Jack Welsh's guardianship of General Electric saw it become a cornerstone of the business. Like Toyota, General Electric needed to combine the efficiency of its people with a requirement to cut waste. The two are now indelibly linked.
Whereas Six Sigma looks to improve process by means of statistical analysis of production metrics, lean seeks to improve the flow, eliminating unevenness. Like many of the terms used in business, flow crosses many boundaries. Sportsmen, artists and programmers all seek the Zen-like state of being "in the zone." With the workforce in aggregation working in a state of flow, the process will almost look after itself.
Just in time (JIT) is another manufacturing approach that emanated from Japan and caught the world's interest. Lean, Six Sigma and JIT are companionable bedfellows.
Where Manufacturing Leads, Others Follow
If something is good in one industry, it will be adapted by another. Hence, both lean and JIT make use of Kanban, another innovation from the east that has inculcated its presence the world over. Kanban, again with its nascence in Toyota, is best translated as a signboard or billboard. In software, Kanban is the latest iteration of thinking in the agile methodology process suite. Dig a little deeper though and agile (lightweight, flexible and responsive) development of usable software in as short a time as possible is not so far removed from lean practices.
Although Six Sigma is ostensibly about statistics, lean about flow, and JIT about the elimination of waste, they all have one thing in common. From Abraham Maslow's study of the hierarchy of needs to Frederick Herzberg's motivation and hygiene factors, all of these theories and practices become the bedrock of management teaching practices because they all have one common factor: people. Get the people part of your process right and the rest will follow. People the world over respond to the same principles, whatever the language and wherever the birthplace of the process.
Limiting the Dangers and Recovering
There is one significant difference between manufacturing and the more office-bound industries like software houses. If things go wrong during the operation of large pieces of manufacturing machinery, people can get hurt. It is no surprise then that the practice of health and safety is paramount within heavy manufacturing. However, if things do go wrong, all is not lost. Every process builds in space for feedback, for the ability to extract the lessons learned from every iteration of the process that went before. If lessons are not learned, information is wasted just as much as the physical assets. Keeping all production within the standard normal beloved by Six Sigma should be every process's goal.
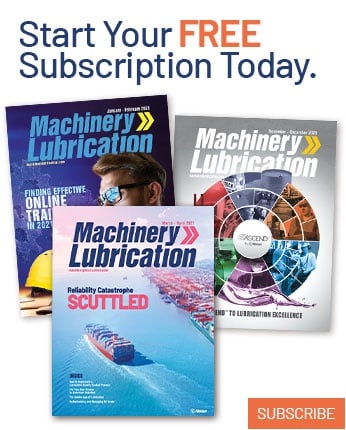