Lean manufacturing incorporates efficiency and simplicity to reduce waste from labor and materials losses while increasing profits. Lean production also requires quality production, or your business loses through product waste. While taking shortcuts may initially seem like a way to reduce costs, the savings are only temporary. In fact, the small amount of savings from poor practices can cost your company much more in the end.
Materials Shortcuts
Obviously, using low-quality materials to reduce costs will often turn out badly. You can experiment with some changes, but what is produced must still meet your clients’ quality requirements. Problems frequently occur when trying to reduce costs by ordering a minimum amount of raw materials.
For items with short lead times, you can keep your on-hand materials at a minimum. Inventory with longer leads must not be allowed to run low. Work with your suppliers to build a strong relationship. Suppliers should alert you if a particular material might suddenly be in low supply. You may even be able to work out bulk pricing with interval shipments. This keeps your on-hand materials at the correct level and helps your suppliers know how much inventory they must have available.
Production Shortcuts
Lean operation involves a balancing act of having the required number of products available for on-time delivery. Excess production costs your company money in cash flow and storage. Not having enough inventory is just as bad. Trying to run production as short as possible will backfire when quality issues or other losses develop.
The kanban approach is often recommended for managing on-hand product. To use this method successfully, you need to have accurate figures on how much product is required for a 30-, 60- or 90-day period. Options include working with your customers to establish a predictable demand rate. You can also reduce the setup time for production changeovers using Single-Minute Exchange of Die (SMED) wherever possible.
Safety Shortcuts
Safety is one area where shortcuts should never be taken. It is also extremely common for employees to skip steps to increase production or to get work done quicker. It may be faster to work with a safety guard out of the way, but the guard is there for a reason. Likewise, it may be faster to make repairs without shutting off the power, but the risk of electrocution or entrapment is too large.
Even trying to speed up conveyors or other assembly-line systems can lead to safety issues. Supervisors must be vigilant in looking at how employees are working to make sure that safety shortcuts are never taken.
Repair and Maintenance Shortcuts
Equipment failures create downtime. Maintenance schedules cannot be ignored in an effort to save time or labor. You may need to schedule an extra individual to work abnormal production hours, but the maintenance must be performed. Ignoring a worn-out belt or a small oil leak now can result in a major breakdown.
There are ways to keep your equipment operational and maintain your lean production goals. Use quality equipment and replacement parts the first time. For example, wires and cables running to your equipment should be rated at more than just the minimum specifications. High-quality wires and cables reduce downtime and increase production.
If cables require high flexibility or insulation to resist chemicals, purchase cables that include these features. Use longer-life oils and oil filters, even if you normally follow a perfect maintenance schedule. You must consider the costs of constantly replacing lower quality parts, the labor involved in replacement and the loss of the equipment during repair to realize how much this type of shortcut truly costs.
If your company can afford to have spare equipment, you can rotate use through repair cycles. For instance, if you have four drill press operators and five drill presses, one machine can always be on standby. Keep at least one set of standard replacement or repair part sets available for each type of equipment you are running. Losing a piece of equipment for several days due to a broken belt or cable will not help you meet your lean production goals.
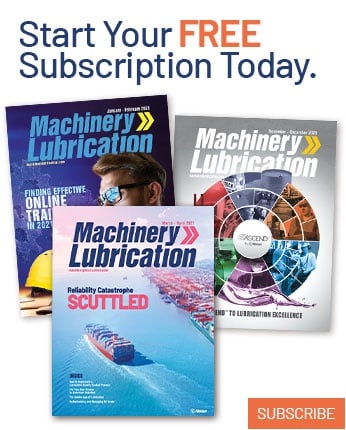