Manufacturing benchmarks achieved by a rural South Australian factory are being shared and instituted across the world by global manufacturing giant Kimberly-Clark.
Based in Mount Gambier, the Millicent Mill produces 85,000 tons of tissue paper each year for the New Zealand and Australia markets.
Recent state-of-the art additions include a co-generation plant, improvement of wastewater quality and introduction of automated guided vehicles (AGVs), all of which have provided the necessary efficiency and productivity advances to compete successfully on the manufacturing world stage.
"It is tough being a manufacturer in Australia at the moment," said Millicent Mill manager Scott Whicker. "We have to be smarter and better than our local and global competitors given the cost of labor, energy and transport to get raw materials to the mill and finished product to market. Some of the things we have been doing here in Millicent are being copied by Kimberley-Clark factories around the world, providing best-practice outcomes."
The $33-million co-generation plant uses clean gas to power a turbine engine and generate electricity for the entire factory. The plant replaced an aging gas-fired boiler, and now all of the mill's steam requirements are provided by the exhaust heat of the turbine engine.
The plant has effectively taken the mill off the local electricity grid as it generates more than 90 percent of the mill's electrical load. This has provided significant savings in energy costs as well as reduced the carbon footprint of the factory, eliminating 80,000 tons of carbon dioxide emissions annually.
The factory's wastewater improvements were also recently lauded by the South Australian Environment Protection Authority, which stated the quality of water included a 95-percent reduction in phosphorus load and an 89-percent reduction in nitrogen levels.
A $2.5-million investment in AGVs replaced the manned forklifts in the distribution center. They handle the task of shuffling more than 2,000 pallets per day in and out of the 26,000-pallet, high-rise automated storage and retrieval system (ASRS) warehouse using rotating laser global positioning systems. On average, the mill dispatches around 26 B-double trucks of product each day.
"While we have to look at our operations from a financial perspective, we also have a set of sustainability goals that we strive to meet," Whicker said. "The new techniques we have employed at the Millicent Mill are setting new benchmarks and are being adopted or adapted for use in other Kimberly-Clark factories around the world. The efficiencies are something we aim to continuously improve on so we can stay ahead of the game and keep manufacturing here in South Australia."
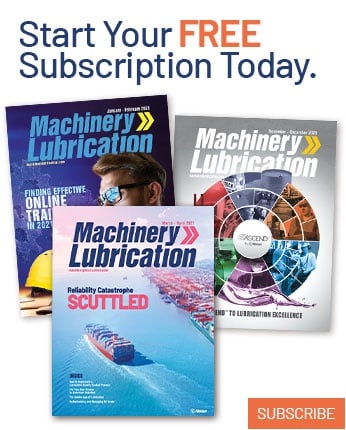