Ford recently launched a new sustainable workforce initiative meant to ensure the long-term health, efficiency and productivity of the company's most important asset – its people.
"Ford could not exist without all of our hard-working employees, so it's important for us to do everything in our power to provide a safe and sustainable work environment," said Jim Tetreault, vice president, Ford North America manufacturing. "Through our sustainable workforce initiative, we're taking a new, holistic approach to fostering growth and well-being amongst our workers, and making sure Ford is a great place to build a career over the long term."
The goal of the initiative is to keep hourly employees healthy and safe throughout their Ford careers. The initiative focuses on four components: high-performance hiring, advanced training, protection and safety, and health and well-being for life.
High-performance Hiring
As part of the initiative, Ford's human resources team will determine which candidates are likely to be high performers based on a comprehensive test that looks at skills, abilities and motivation.
"We look at what candidates can do as well as what they will do," said Tetreault. "Factors associated with motivation – work ethic, conscientiousness and teamwork – are just as important in an effective employee as skills and abilities such as reading, arithmetic, defect spotting and manual assembly. Looking at candidates from both perspectives allows us to better select potential high performers who we want working with us."
Advanced Training
After strategic hiring, training is crucial to ensure new hourly employees are prepared to work safely and efficiently. Base operators receive several weeks of training – a combination of classroom, simulated factory and hands-on factory work. Semi-skilled operators receive up to six months of training, and skilled trades training has increased to more than six months, or up to nine months prior to a model launch.
Simulated factory training, which was developed at Ford's Louisville assembly plant in Kentucky, has expanded to the Flat Rock assembly plant in Michigan in preparation for the start of Ford Fusion production.
"This training process, which provides workers with hands-on training in a real-world work environment, has been so successful that it is now considered a global standard and is being implemented in our plants worldwide," said Tetreault.
Protection and Safety
In 1999, Ford revamped its safety program to create global safety process standards. Employees must "stop, think and plan" before taking on any task, whether it's replacing a light bulb or a production task on the assembly line.
"By having our employees analyze the task before any work begins, we are able to better prevent safety incidents in our facilities," said Tetreault. "Overall injury rates have dropped to one-tenth of the levels of 1999, and our lost-time case rate is just a fraction of what it was in 2000."
To identify ergonomic issues early and reduce the risk of chronic repetitive motion injuries, Ford conducts virtual ergonomic assessments in its virtual factory. Resolving issues before the production of physical parts plays a significant role in keeping employees safe in the workplace.
"Since implementation of our virtual factory, the number of ergonomic issues during physical builds has been greatly reduced," said Tetreault. "So far in 2013, our days away and restricted time rate has fallen to less than one-sixth of where it was in 2001, and we continue to make progress."
Health and Well-being for Life
Ensuring employees' long-term health is the final step in maintaining a sustainable workforce. To improve the health-care experience and outcome for hourly employees with the greatest need, Ford recently announced its Enhanced Care Program. This voluntary two-year pilot program uses a personalized care approach to help eligible participants manage chronic health-care needs and prevent future problems when possible.
"Our hourly worker population tends to be more high risk, to have more chronic conditions like asthma and diabetes, and to use preventive services less often compared with the national average," said Tetreault. "As health-care spending continues to increase, Ford, the UAW and health-care providers continue to work together to develop and promote programs that will maintain or improve employees' health while reducing costs at the same time. We think the goal is imminently achievable."
For more information, visit www.ford.com.
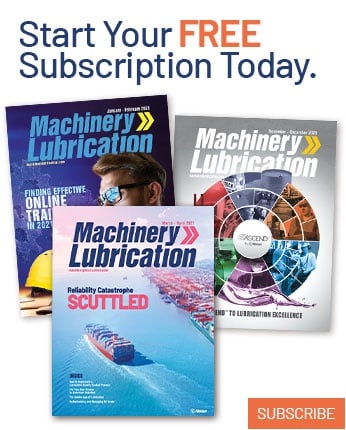