Lean efforts used to be 100-percent directed at the shop floor. What we have seen recently is that lean is moving into non-traditional areas of business. A lot of our recent work has been in maintenance, procurement, distribution, engineering, the office and even the company kitchen.
A friend of mine recently sent me an article about how Starbucks is realizing benefits from lean efforts in its stores. The coffee-shop giant is doing spaghetti charts, videotaping the work effort and working to reduce the time it takes to process an order. If Starbucks can shave 20 to 30 seconds off an order process that takes 1 minute, 45 seconds, that is a 23-percent improvement. Multiply that by 1,000 orders and you have saved nearly seven hours of effort. That’s certainly enough to save overtime, do more with less and spend more time making customers happier.
However, please keep in mind that the goal of lean is never to rush the process and make the quality worse but merely to eliminate the waste.
So many organizations miss the opportunities to improve in almost all aspects of their business. If you can work to shave time here and there through process improvements on menial tasks, the quality of the entire process can improve, since the employee can spend more time on the important tasks at hand, work less overtime (if hourly) or, if salaried, work less hours and be more productive.
We worked with one group that had a fabrication department that received the job packets on the shop floor between 9 a.m. and 10 a.m. when the operation started at 6 a.m. Despite the fact that the orders were printed every day at midnight, the orders sat in queue or on someone’s desk in queue awaiting work for nine-plus hours.
Each day, the company was losing three to four hours of work time due to waiting on paperwork. Although they had work to do and were not idle, with a four-day lead-time, if an order lost nine hours because of paperwork, they were losing 9.4 percent of their time at the front end due to delays. It is no wonder their on-time performance was in the 80-percent range. They were starting off nine hours late just because of paperwork.
I would encourage everyone to review their entire value-stream processes and find areas that are non- traditional to improve the waste. Take off your regular glasses and put on your waste glasses. You will be shocked at the opportunities that you will find.
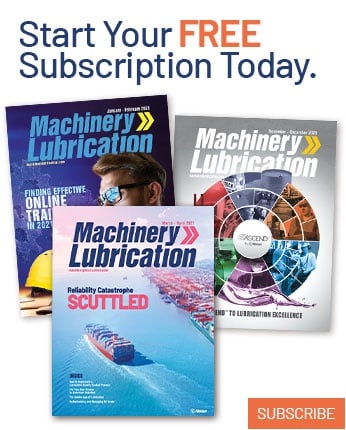