What does training within industry (TWI) have to do with the current economic issues? Well, it can have a very positive impact for firms struggling with the present business conditions. Whether times are prosperous or not, any business can benefit from improving output per employee, resolving people issues quicker and more effectively, drastically trimming the time to train personnel (whether they are a new hire or long-time employee), and improving safety and quality.
So why isn’t every business leveraging TWI to reap these benefits? I don’t know, but they should. TWI is also a foundation for standard work and continuous improvement; that is, it is a foundation for the lean business model.
The United States dropped the ball after World War II by letting TWI go the way of the buggy whip or steam engine. Many Japanese firms picked up that ball and ran with it — and are still running with it today. Toyota runs with it today. In fact, that company could not be as competitive without it.
TWI is not just for manufacturing. It is every bit as applicable in the healthcare and service industries. It was developed by industry for industry (and service), so industry would be crazy not to use and leverage it once again.
In the past couple of years, a growing number of firms have begun to use TWI again, and the ones who are working with it seriously are garnering significant benefits. When combined with a valid business strategy, it can put a business in a position to be very prosperous when times are good, and to be stable and OK when times get tight. Where would you like your firm to be — with the winners or the losers?
Perhaps if TWI had never been dropped manufacturing, especially automotive, would not be in the mess it is in today. It played a significant role in saving the country once. Can it do it again?
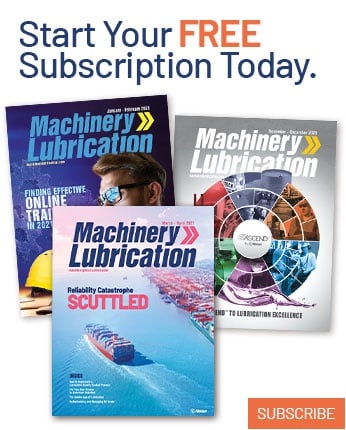