If your backlog is piling up or you feel like you don’t have enough resources in terms of labor and parts, it may be time to work toward lean maintenance.
Lean maintenance is the application of lean philosophies, methods, tools and techniques to maintenance functions. It has the fundamental goals of eliminating waste associated with labor, inventory, procedures and techniques, resulting in improved productivity and reduced costs.
Lean maintenance does not imply a slash and dash approach to cutting costs and jobs. This common method will not reduce waste or lower costs. Instead, lean maintenance philosophy decreases costs by getting rid of waste that can be defined as “anything that doesn’t add value to the maintenance process or service.”
Following are a few areas where wastefulness and sluggishness can crop up in the maintenance department.
Overproduction
Overproduction in the maintenance environment means doing any work that does not add value. Examples include performing preventive and predictive maintenance tasks more often than is necessary and redoing jobs that were not done correctly the first time.
Waiting
Areas of waste in this category include maintenance personnel waiting for equipment availability, job assignments, tools, parts, instructions, other crafts, permit approval, etc. Waiting is not a value-added activity and should be eliminated or reduced as much as possible.
Transportation
Unnecessary travel is the result of ineffective planning and scheduling. This could involve a trip to the maintenance shop to get technical information or to the storeroom for parts and tools. Poorly designed preventive maintenance (PM) routes are also a major contributor.
Process Waste
When performing a breakdown repair, maintenance personnel are typically under a lot of pressure to fix the equipment as quickly as possible and often are not given enough time to fix the equipment properly. This results in a poor repair and a recurring problem. Properly performed repairs can eliminate this process waste.
Most organizations now use some sort of computerized maintenance management system (CMMS) or enterprise asset management (EAM). Process waste also occurs when inefficiencies exist in these systems. For example, a poorly designed system may call for multiple entries of the same data, or a material requisitioning process could require redundant approvals.
Defects
In maintenance, a defect can be defined as leaving an asset in an unreliable condition. There are many causes of defects in the maintenance environment. Defects due to poor workmanship arise from insufficient training, inadequate/outdated procedures and not having the proper tools to do the job.
Spare Parts Inventory
Most storerooms contain a significant amount of obsolete inventory. This ties up capital and consumes management resources. It can easily amount to 10 to 20 percent of annual inventory dollars. Keep in mind that excess inventory is not obsolete but is inventory maintained at unnecessarily high levels. Excess inventory also ties up capital and consumes management resources. In addition, inadequate PM programs cause equipment failures, which in turn results in the need for more parts (consuming working capital) and downtime.
A CMMS/EAM can monitor and control a spare parts inventory. It will keep track of inventory items, vendor performance, parts receipts, issues and returns. In addition, a CMMS/EAM can automate the parts purchasing process. Vendor-managed and stocked inventory can also drastically reduce the parts quantity in the storeroom and save money.
While breakdowns and failures are never planned, they can cause the loss of productivity and money. Finding the root cause of a failure provides an organization with a solvable problem. Once the root cause is identified, a fix can be developed and implemented, preventing a recurring failure situation.
About the Author
Kris Bagadia is the president of PEAK Industrial Solutions in Brookfield, Wisconsin. A longtime consultant and educator, he can be reached by e-mail at krisb@peakis.com or via www.cmmsmadeeasy.com.
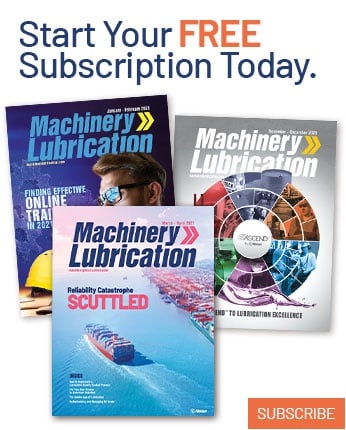