What does a visual workplace have to do with your safety program? Well, it can be one of your best tools for promoting and maintaining awareness among your employees as well as a subtle training program.
Human beings are visual creatures. We are geared to perceive our environment through our primary sense: vision. You see, interpret and catalog enormous amounts of data through your sense of sight every day. A great deal of this is subconscious, but very real. Why not piggy-back onto this completely natural process to teach safety principles, transfer information on safety resources and keep safety in your employees’ daily thoughts?
OK, you ask, “How do I do that with visual aids?” It seems fairly intuitive to me that you think about what you see, so let’s put things into the visual field that promote our safety goals — things like safety slogans, how-to posters, signs that point out hazards or direct you to safety equipment, and informational posters that increase the employees’ knowledge base. Placement is important. It helps to rotate posters so you get more bang for your effort and people don’t get jaded by seeing the same old remark in the same place every day.
Safety Slogans
I like the idea of having a number of these that fit into 8.5-by-11-inch holders on the wall. Rotate the posters every so often between the locations to keep the message fresh. Locations should be where people congregate or pass the most often.
How-to Posters
Lifting techniques, fire extinguisher procedures, CPR instructions, etc., all pass on information that can come in handy.
Hazard Signs
You can get the pre-made stickers showing pinch points, fire hazards, electrical shock hazards, etc.
Personal Protective Equipment Signs
Don’t forget that you can post the personal protective equipment (PPE) requirements in the area, and you can also put up posters that show the proper use of that PPE.
Informational Posters
Lots of things are available that explain material safety data sheets (MSDS). There are also signs that show where to find safety equipment like fire extinguishers and spill response kits.
To get these aids, search the Internet and look under “safety posters.” You’ll find hundreds of sources with many products available for reasonable prices. You don’t have to break the bank up front to get some results. Start where it makes sense to you and expand along the way.
It’s important that you have someone in management that supports and promotes your awareness effort in meetings, in daily discussions and even in e-mails or letters. A simple safety comment at the end or somewhere within the subject makes everyone aware that safety is a priority with management. Every meeting, no matter how small or large, should include safety in some form.
How does this affect the bottom line? Safety pays for itself in reduced insurance rates, in fewer lost work days, and in increased production and reliability.
Reduced Insurance Rates
The average back injury in industry can run about $80,000. That’s not chump-change. Your insurance carrier quotes your rates based on your injury history and the risks inherent in your industry. The risks can be pretty much built into the process without some major re-engineering, but your injury history can be changed. Reduce the opportunities for injury and you reduce the incidence of injury. Once you start reducing those incidences through better knowledge and better methods, you can talk to your carrier about reduced rates.
Fewer Lost Work Days
This seems self-evident. If you reduce your opportunities for injury and you reduce the severity of those injuries, you reduce the days that must be lost. It can be something as simple as fewer days lost to slips, trips and falls or as complicated as fewer days lost because your folks knew the hazards associated with a chemical and avoided exposure. Fewer lost days mean better use of available labor, and that can mean less overtime hours or even reduce the need to hire additional people.
Increased Production
A safe shop is a more productive shop. That sounds like an unsubstantiated cliché, but I have found it to be true. When you approach a job on the safety side, you get an added benefit of better planning for that job. Many times, we find that formatting the job to be safer also makes it more efficient as we do a better job of placing materials, supplying the correct tools and making the work easier for the employee.
Reliability
A safe approach to a task can improve the quality of the result, and that means repairs are performed better, inspections are completed more thoroughly, and equipment operates longer between failures. Technicians that have the proper safety knowledge and equipment, lift properly, have better access to components and tools, and use the proper PPE also do a better job of torquing bolts, leveling or aligning components, and are also more apt to perform a thorough inspection. Safety habits promote a planned approach to the job, and that gets the job done better.
There are lots of little tricks to promote safety, but the most important one is to just get started. Do a little research on the Internet, contact some vendors, ask around among the folks in your professional organizations or industry contacts, and talk to your troops. Do a walk-about at your plant or shop, make a mental inventory of what can be done and then do something. Start small in one area or with one approach and then expand as you go. Safety and reliability are journeys with no end.
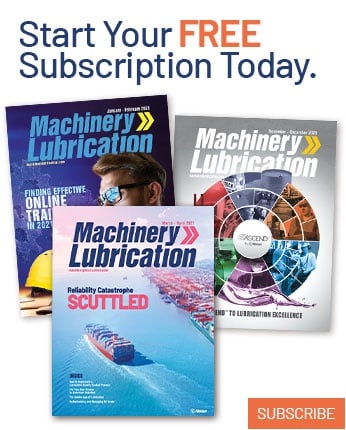