As the demand for new homeland-security technologies continues to increase, so too does the competition among private companies vying for a piece of the market. Accommodating customer demands for fast delivery times often is the key to success – or failure.
One company thriving in the fast-changing homeland-security market is American Science and Engineering, Inc. (AS&E). The company manufactures sophisticated X-ray products used to inspect parcels, baggage, vehicles, pallets, cargo containers and people.
In 2008, AS&E initiated a lean manufacturing initiative that continues to focus on increasing factory output and revenue while improving operational efficiency.
Doug Capri, AS&E’s manufacturing engineering manager, says the lean initiative looks at every aspect of the manufacturing process. One of the low-hanging fruits identified as needing immediate attention was the way the company documented its manufacturing processes. Capri decided it was time to improve the documentation process with a computerized, paperless system.
Capri says each step of manufacturing –including keeping a production record book, test procedures, quality inspections and visual work instructions –was done manually in a paper-based system.
He says the documentation process represented 1.5 personnel headcounts over an eight-hour shift.
“There was tremendous waste of time and paper,” Capri says. “We had to manually maintain, audit and laminate each document on a daily basis before we started a build.”
Additionally, Capri says the paper-based system required several pieces of software to develop the work instructions. “We had to use Word and an editing software package for the digital pictures,” he says. “So we would normally take a picture, crop it and then paste into Word. That was very cumbersome and hard to work with.”
Choosing Sequence
After a review of potential suppliers, AS&E chose FFD, Inc., a Knoxville, Tenn.-based software company specializing inmanufacturing work instructions for paper and electronic applications.
One of the reasons FFD’s flagship software product Sequence was selected by AS&E is because it allows easy capture of AS&E’s core manufacturing knowledge and eliminates the need for an inefficient text editor and a third-party graphics package.
“Sequence is an extremely efficient tool for knowledge capture, organization and management,” says FFD president Barry Lucas. “We have put all of the necessary editing tools for text and graphics right at the user’s fingertips in an attempt to eliminate whenever possible the necessity of using multiple software packages. Additionally, authors of instructions aren’t creating and formatting a document but simply organizing information on a visual process-flow tree. Sequence takes care of the deployment.”
“We were skeptical that the software would do everything we needed,” Capri says. “So we rolled it out as a pilot project on one product line and then on our more simple and stable products. It went better than expected. Now we use it throughout our plant on all three product lines.”
Going Paperless Boosts Efficiency
Today, the 1.5-person headcount once needed to maintain the different work documents has been redeployed elsewhere, supporting the plant’s lean initiatives. Capri says the newfound benefits and efficiencies of switching to a paperless system were immediate, adding that AS&E recouped its investment in the software within the first year.
“From both lean and quality standpoints, we eliminated the need to stop work and wait for an inspector to come to the workstation and sign in,” Capri says. “Now we have a qualified operator verify other assemblers’ work online. So now we have quality accountability that is digitally logged in the production workbook.”
“It is a very functionally specific piece of software designed to mimic the type of information that companies are accustomed to managing in a manufacturing environment,” says Lucas. “Before, it took a lot of time to gather and validate manufacturing information from the different systems. Now it is an integrated part of AS&E’s overall business system.”
Synchronization with ERP
The paperless deployment capability of Sequence allows AS&E to selectively access information in a controlled and validated manner and present it to personnel on the shop floor. Every work order that is released from the company’s MRP system represents a serial number. When a work order is released from MRP, Sequence ties a specific set of instructions to that work order. The work instructions are accessed on the plant floor by work-order number and become the core of their production record book for the customer. In fact, the product will not ship without a report from the Sequence software.
“There are a lot of visual and visual software packages that create nice, pretty pictures and can do all the graphics, but they have no link to MRP,” Capri points out. “So if our MRP changes, if we have a design change and the bill of material changes, our paperless system is able to send us an e-mail and it also shows up in our Sequence bill of materials. That feature has allowed us to become more efficient implementing changes.”
Just as important, AS&E has improved consistent product processes, accountability and traceability with serial numbers to track defects back to root cause quicker.
Reduced Time to Market for New Innovations
AS&E also utilizes Sequence software to document and speed up new product innovations, even at the prototype stage. This is a benefit that dovetails perfectly with AS&E’s goals of developing options and adaptations to meet specific needs of customers.
“Now we can have the framework of a project when we do our first build,” Capri says. “Before we had to wait until the prototype was built and document after the fact.”
AS&E uses solid modeling for new product prototypes. Working in a three-dimensional, virtual world, AS&E can complete work on the model before ordering parts. Photographic images captured within Sequence give engineers the ability to tweak the design as the prototype evolves. As a result, significant time is saved because of concurrent engineering.
“We can determine the manufacturability of a product by using the model,” Capri says. “We can develop a document even in the prototype stage. That has helped reduce deployment and engineering time by 15 percent.”
Enhanced Training
Because of the nature of the homeland-security business, Capri says some customers require an almost impossible delivery schedule.
“Sometimes we have to go to a second shift and bring on new people,” Capri says. “This is highly sophisticated, custom-built equipment that goes to certain locations because of security concerns. Because operators can see everything on a computer monitor, it helps with the learning curve. This has allowed us to also have a more flexible workforce. We now have a consistent process for moving people from one area to another quicker with less training.”
Just-in-Time Learning
Additionally, the paperless system allows AS&E to implement lean changes more quickly than a paper-based documentation system. Capri says if a new way to improve efficiency is found in one assembly cell, it is easily adopted into the Sequence software system.
“We have a value-stream mapping process,” Capri says. “If the guys on the plant floor come up with a new way to do something, we can document that very quickly and release it to the next work group quickly.”
Simplified Reporting
These changes, as well as the entire production record, are instantaneously available to Department of Defense (DOD) inspectors as well.
“The old production record books were handwritten,” Capri says. “Now we’ve implemented barcode readings to record serial numbers right into Sequence. That reduces the chance for error when we get audited by DOD.”
The Bottom Line
Capri says the company’s lean initiative is on track for even more improvements, but the bottom line is this competitive international market oftentimes comes down to cycle times and deployment.
“Sequence is part of the overall process that has helped reduce cycle times by two weeks,” Capri says. “Our customers want the products right away, and if we can’t deliver, they will go to somebody else.”
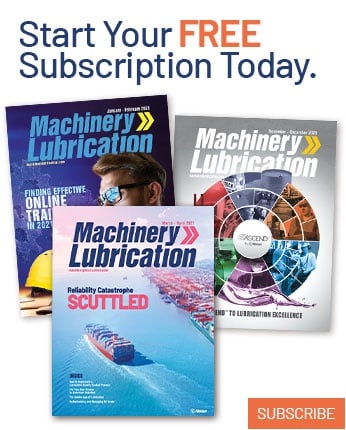