Ask the Energy Expert is an ongoing column with the intent of providing information and solutions for some of industry's most pressing questions. This issue's Energy Expert is Richard Miller, corporate energy manager at Mannington Mills. Miller's role involves developing, coordinating and implementing the aims and objectives of Mannington Mill's strategies and policies to reduce the company's energy consumption.
Dear Energy Expert:
I work as a facilities engineer for a mid-sized manufacturing firm and recently assumed the unofficial title of energy manager for our production unit. Lately, we have been experiencing communication gateway issues within our sub-metering system. What challenges has your company faced with its sub-metering system, and how can we capitalize on this experience at our facility?
Mannington Mills is a manufacturer of residential and commercial resilient, laminate, hardwood and porcelain tile, as well as commercial carpet and rubber floor covering. In business since 1915 and family-owned for four generations, Mannington Mills operates under the mission of being “the best people to do business with in the flooring industry.” We take extreme pride in our dedication to our products, our customers and our values.
As a leader in product innovation and environmental stewardship, our organization regards energy as a critical company resource. We view efficiency as an important element of corporate sustainability and effective energy-management strategies. As such, we have developed a rigorous energy-management plan and energy-use and intensity baselines that strengthen our commitment to energy efficiency and place heightened importance on the reduction of industrial energy intensity. In partnership with the U.S. Department of Energy's Industrial Technologies Program, we have committed to ambitious energy intensity reduction goals.
Metering System
Industrial organizations utilize sub-metering systems to account for and monitor the energy use of their individual facilities. Properly maintained systems allow an organization to establish metrics for these facilities and to gauge their overall energy performance. Most importantly, though, these systems facilitate the establishment of energy documentation and management systems, capable of handling data from multiple and distinct facilities, and set a precedent of explicable granularity in data reporting.
In 1995, our corporate facility in Salem, N.J., was seeking to implement a metering system that would provide us with a picture of our overall and individual facility energy use. We installed 40 Schneider Electric POWERLOGIC Series 2000 Circuit Monitors throughout our campus. These multi-purpose control monitors featured real-time and demand readings, as well as energy readings and power analysis values.
However, the system was only set up as a means of performing cost summaries for budget allocation and was owned and operated by our accounting department. Sub-meters were not monitored for energy use or data collection, and software upgrades were not maintained. As a result, the meters fell into disrepair.
By 2008, though, were we beginning to look more closely at our corporate energy-management systems and identified our metering system as problematic. We conducted a comprehensive review of the system and quickly discovered that various control devices on four of our sub-meters were malfunctioning.
Addressing the Issues
We decided to take immediate action to address these issues. We began taking regular, manual meter readings and ran server reports once a week to identify any possible defects in our sub-meters. We contacted United Electric, a local distributor, whose sales staff assembled our original system. They assisted us with a system assessment and partnered with us in a one-year system-support program to provide remote troubleshooting and onsite support for our meters.
These efforts continue today. We properly maintain our meters with a preventive maintenance plan that involves our staff recording real-time data and reporting any abnormalities. Another part of our maintenance plan is keeping current with upgraded series software versions.
Our corporate management would also like to ensure that the metering system is addressed as a whole. We are currently in the process of verifying that each wire in the system is functioning and interacting with the system properly. This is being done to ensure that communication gateways and systemic network issues are also addressed. We have also identified the Schneider Electric POWER LOGIC Series 3000 meters as part of our system upgrade. Each unit will cost around $1,000 and will include all communications software and wiring.
Conclusion
Mannington Mills recognizes that our metering system is vital to our operations and that sub-meters are necessary to maintaining reporting granularity and system accuracy. We feel that the system enables us to communicate to facility managers where they are, what our expectations for them are, and where we need them to go in terms of their performance. Our sub-metering system also helps us to understand energy use patterns and trends. It also helps us evaluate the performance of our facilities’ equipment and systems to determine improvement potential as we move farther into the 21st century.
This article first appeared in the Winter 2010 issue of the Energy Matters newsletter. For more information, visit the http://www1.eere.energy.gov.
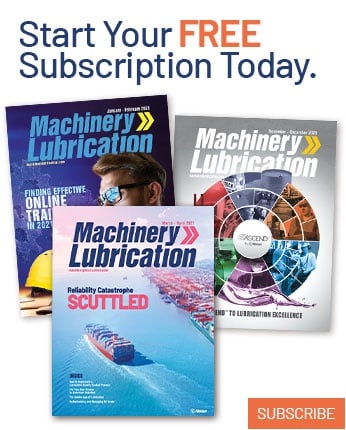