What looks like a harmless speck of sand to one person can be a big nuisance for a new car owner. That is why engineers at Ford Motor Company are working with the same computed tomography (CT) scanners that police and hospitals use to improve vehicle quality.
Much like crime solvers on television, Ford has its own team of “forensic” investigators employing cutting-edge scientific methods to improve the quality of parts such as gears, latches, welds, nuts, bolts, fasteners and sensors before they are assembled into a finished car.
Analysts like Ford’s Vlad Beltran in the past would spend hours, days – and even weeks – sanding an individual part, such as a bolt, one layer at a time until a small scratch or bump was discovered. Now, Beltram uses 3D virtual imaging to target a flaw inside, such as an air pocket or scratch, that may be no bigger than a dust particle.
Beltran’s work keeps Ford quality high by uncovering the air pockets, indentations, and blemishes that mean the difference between acceptable and optimal performance.
The critical tool is a Skyscan Micro-CT scanner that fits on a table-top.
“The CT scanner is an essential tool to help us study why parts aren’t performing at their optimum level,” said Beltran. “It can be used for any number of things – troubleshooting for supplier parts, new parts that engineers are testing or parts from vehicles undergoing durability testing. When a part contains a deficiency, it’s critical to address it right away. We need to find out why. We need to either improve the part or improve the process.”
Ford works closely with its suppliers to understand how parts are made. The CT scanner can help check for internal and structural deficiencies, and verifies that any changes suppliers make do indeed improve the quality and performance of the part.
The remarkably advanced Skyscan works on the same premise as larger CT scanners used in hospitals or crime investigations. Lab analysts take an X-ray of the part being studied and then use the scanner’s software to reconstruct it virtually. The virtual image of the part can be viewed horizontally and vertically in digitized slices. The scanner can detect defects down to 17 microns – smaller than a single particle of sand or one-fifth the diameter of a human hair. That means problems not visible to the naked eye can be seen on the computer screen.
Using the software, analysts also can create a short, three-dimensional video from the data to better explain the situation.
The overall goal is to think and work proactively, said Jeff LaDuke, product development supervisor at Central Laboratory. “There are so many components on so many systems of a vehicle, and if one part is flawed, it can compromise the integrity of the entire vehicle or vehicle system,” LaDuke said. “What we’re doing here is finding problems before they become issues with customers.”
Before the lab obtained the scanner, each component was studied and taken apart by hand. “We’d spend hours sanding it a little, polishing it a little, examining it under a microscope and then take a picture of it, repeating this process several times,” said Beltran. “Even then it was possible that we could go right through a defect and not even know it.”
With the scanner, many issues can be solved within a few hours. Once the mystery is solved, the information is given to a materials engineering group that works with designers and a supplier base to resolve the issue and/or correct the situation.
“Word has spread since we’ve obtained this technology, so we’re increasingly seeing different types of parts from all over the world,” added LaDuke.
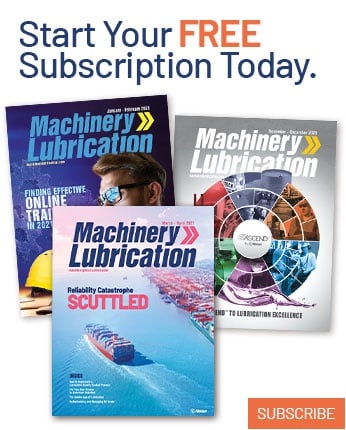