When Harrison Steel Casting Company made the decision to advance its energy-efficiency efforts, the company took stock of the resources available to industry and made a strategic decision to partner with both the U.S. Environmental Protection Agency’s (EPA) Energy Star program and the U.S. Department of Energy’s (DOE) Industrial Technologies Program (ITP) Save Energy Now LEADER initiative.
Harrison Steel joined both of these programs because it allows the company to take advantage of the multitude of resources available from both Energy Star and the Save Energy Now LEADER programs. Harrison Steel’s participation in both programs serves as an example that can be followed by other industrial companies interested in making improvements in energy efficiency.
As Harrison Steel discovered, the programs differ in their scope and resources to provide complementary resources for industry. Where Energy Star focuses on assisting companies in establishing effective energy management teams and corporate energy management programs, Save Energy Now LEADER offers technical expertise and assistance for successfully implementing efficiency improvements to industrial systems and processes. Industrial companies that are interested in reducing energy consumption and the associated costs should examine the results that Harrison Steel has realized by partnering with both the Save Energy Now and Energy Star programs.
Figure 1. Ductile iron is poured into casting molds at the Harrison Steel facility.
Background
Harrison Steel energy manager Jeremy Allyn points to 2006 as the year that Harrison Steel began a clear commitment to energy reduction; that was the year when the company received an energy audit from Jack Staley of Balance Engineering. The audit produced a fairly extensive list of energy conservation measures. Although Harrison Steel did pursue some of the recommendations, the true value of that initial audit was opening the eyes of the company’s leaders and plant staff to the potential of realizing cost savings through the implementation of energy-efficiency projects.
Saving Energy to Improve the Bottom Line
Energy costs at Harrison Steel typically constitute 5 to 8 percent of sales. In 2008, the company was operating at full capacity, and it spent approximately $5 million on electricity and $4 million on natural gas. However, it should be noted that Harrison Steel’s natural gas costs were slightly above average that year due to the higher-than-normal prices at the time. The company’s electricity prices in 2008 were 6.8 cents per kilowatt-hour (kWh) with approximately 73.5 gigawatt-hours (GWh) of usage that year.
In 2008, the average operating profit for steel foundries with more than $25 million in annual sales, such as Harrison Steel, was 6.6 percent of sales. This slim profit margin is typical for steel foundries, and reducing operating costs through energy savings can help increase that margin and provide a competitive edge. Because rising energy costs can negatively affect profits, Harrison Steel understood that every dollar saved on energy spending would go directly to the bottom line. Additionally, the company understood that energy efficiency measures could have a more immediate impact.
For example, a company with a profit margin similar to Harrison Steel’s that cuts energy spending by $66,000 through efficiency measures like lighting or stopping air leaks would have to increase its total sales by $1 million to achieve the same financial impact. Also, an energy-efficiency project is a constant source of savings that a company can continue to experience year after year, while increasing sales volume on a constant basis is much more difficult. Harrison Steel understands these business-side benefits associated with capturing energy savings, in addition to the benefits that increased energy efficiency has for the environment. In fact, the company has even considered creating a different – and higher – internal rate of return (IRR) for energy projects since they include positive externalities and dependable, consistent savings. Nonetheless, even with using the same IRR as for other projects in the company, Harrison Steel has been able to identify and complete projects with high enough savings to justify implementation.
Initiating Energy Projects
The 2006 energy audit helped Harrison Steel to realize the potential savings that were available by upgrading equipment and improving production processes to increase efficiency. The company began to undertake projects with promising energy cost savings based on the audit recommendations. One such project involved an upgrade to the natural gas burners used for preheating ladles that hold molten metal. The burners were old and obsolete, using a less-than-optimal air and gas mixture and producing a poor flame shape. Harrison Steel chose to implement this project because of its capacity to reduce operating expenses while only costing approximately $17,500 to implement. The estimated energy savings from the improved burners is an impressive $73,857 per year, which means the repayment period for this project was less than three months. To achieve the same annual affect on the bottom line through increased sales, Harrison Steel would have had to generate an additional $1,119,045 in revenue.
Since that initial implementation, Harrison Steel has continued to make progress, including activities undertaken during the company’s 2009 Christmas shutdown. Allyn took advantage of the unusually quiet plant to perform his own assessment to locate air leaks. A single 1/16-inch diameter air leak in a compressed air system at 100 pounds per square inch (psi) loses air at 6.5 cubic feet per minute. At a $.06 per kWh rate, based on 24-hour-a-day operation, such leaks can result in added costs of $633 per year. Equipped with nothing but the naked ear, Allyn was able to locate around 100 air leaks. Harrison Steel uses approximately 5,000 standard cubic feet per minute (SCFM) of compressed air – or 2.6 billion standard cubic feet (SCF) annually – with the largest end-use being the pneumatic transportation of sand for making molds. Fixing those air leaks identified by Allyn was believed to have produced approximately $15,000 in annual energy savings.
Another project identified in the 2006 energy audit that Harrison Steel is currently implementing is a variable speed drives project for its well pumps. This upgrade will allow the company to actually slow down the pumps to control the plant’s water pressure rather than using demand valves to throttle the pressure while the machine is running at full speed. This variable speed drives upgrade will cost $25,000 to implement and will save the company approximately $16,800 per year in electricity costs – a payback period of less than 18 months.
Partnering with EPA’s Energy Star
In the fall of 2009, Harrison Steel began its partnership with EPA’s Energy Star for Industry program, a voluntary government partnership program aimed at helping companies develop and improve energy management programs. Harrison Steel became aware of Energy Star through its work in the Energy Star Focus on Energy Efficiency in the metalcasting industry. The Energy Star program offers guidance to its partners focused on strengthening energy management and establishing corporate energy programs and practices.
In making the decision to partner with EPA, Harrison Steel was particularly attracted to the idea of associating the company with the popular Energy Star brand, a national symbol of energy efficiency and environmental protection. Harrison Steel saw joining the Energy Star program as a way of building a sustainable energy management framework for its energy efforts, making them more personal to employees, not just a list of engineering items to complete. The program also provided Harrison Steel access to a network of companies undertaking similar efforts. Under the program, a Strategic Energy Advisor (SEA) was assigned to Harrison Steel; that SEA is now working with the company to help it build an Energy Team.
To date, Harrison Steel has experienced two main benefits from partnering with Energy Star. First, the company has been able to interact one-on-one with its SEA in order to learn from the experiences of other companies in establishing an Energy Team. Second, the company has gained valuable insights from Web conferences that offer the opportunity to network with and learn from other professionals involved in energy management at organizations with similar goals and challenges.
In addition to Energy Star’s partnership for industry, Harrison Steel also values Energy Star as a resource for improving building envelope systems. Energy Star has resources for energy management in buildings such as office and warehouse facilities. For example, the 2006 energy audit had a recommendation for Harrison Steel to upgrade lighting within certain storage and office buildings. Although Harrison Steel had this report for years, it was unable to implement the recommendation until Energy Star assisted in the formation of the Harrison Steel Energy Team. This team has been able to focus on moving ahead with such projects, and Harrison Steel has now approved a lighting project costing around $10,000 for one of the company’s storage facilities. This project will install more efficient lighting in the storage facility, as well as use motion sensor lighting controls, which will compound the cost savings by automatically turning off lights when no one is in certain parts of the building. The lighting upgrade is expected to save the company between $2,500 and $4,500 per year in electricity costs, the equivalent of increasing annual sales by $38,000 to $68,000.
Partnering with ITP’s Save Energy Now LEADER Program
In addition to partnering with the EPA, Harrison Steel decided in the spring of 2010 to partner with ITP’s Save Energy Now LEADER initiative. The company quickly recognized the added value that Save Energy Now offered. Once the company began looking at the Save Energy Now resources online, it realized that ITP offers technical expertise and engineering applied to industrial energy. Harrison Steel appreciated Save Energy Now’s technical tools that could be applied to the company’s systems. This DOE expertise compliments the work the company had begun with Energy Star. Harrison Steel decided it should also join the Save Energy Now LEADER initiative after recognizing ITP’s technical expertise in industrial systems, which are in-depth and detail-specific to industrial processes.
Harrison Steel immediately benefitted from Save Energy Now through the use of the initiative Web site materials like information on improving energy efficiency through upgrading existing standard belts to newer V-belts for belt-driven equipment, such as fans. Standard belts are approximately 95 percent efficient in transferring mechanical energy, but the V-belts improve efficiency by an additional 2 percent since they require less energy to bend and do not slip. Harrison Steel’s energy team also utilized ITP’s online materials to gain insight and instruction that may allow the company to implement a new project dealing with combustion efficiency of heat treatment furnaces. This project would focus on controlling the oxygen level, making sure there is not too much air in the process.
Example for Other Industrial Companies
The complementary nature of the resources provided by the Energy Star and Save Energy Now initiatives is an important take-away concept for other industrial companies interested in advancing energy management programs. As Allyn noted, where Energy Star for Industry shines in terms of its energy management resources, including energy team support and motivating brand, Save Energy Now brings the engineering tools needed to achieve implementation. Companies partnering with both programs will find themselves equipped with the full spectrum of tools needed to plan and achieve energy savings.
About Harrison Steel Casting Company
Harrison Steel Casting Company began as a car coupler company founded in Attica, Ind., by J.W. Harrison more than 100 years ago. Since then, it has grown to become a producer of highly engineered carbon and low/medium alloy steel castings, working with some of the biggest names in the agriculture, heavy equipment, energy, military, mining, and oil and gas industries. For more information on Harrison Steel, visit its Web site at http://www.hscast.com/.
About Energy Star for Industry
Energy Star for Industry is a voluntary partnership to develop an energy management program. It provides guidance on building an energy team and corporate program through a Strategic Energy Advisor (SEA). It offers Web conferences for networking and showcasing successful energy management strategies; assists with communication resources, such as posters and other tools to help drive the change in corporate energy behavior; and, currently offers benchmarking, plant energy guides and tracking tools for 16 manufacturing industries and sub-sectors. For more information, visit www.energystar.gov/industry.
About the Save Energy Now LEADER program
The Save Energy Now LEADER program involves a voluntary pledge to reduce energy intensity by 25 percent in 10 years. It assigns each member company a technical accounts manager for personalized attention. It also provides priority access to DOE Energy Experts and the Industrial Assessment Centers; tailored assistance to determine an energy-intensity baseline and a plan to meet energy-saving goals; and, access to extensive resources, such as software tools, technical publications, training programs and Webcasts. For more information, visit http://www1.eere.energy.gov/industry/saveenergynow/.
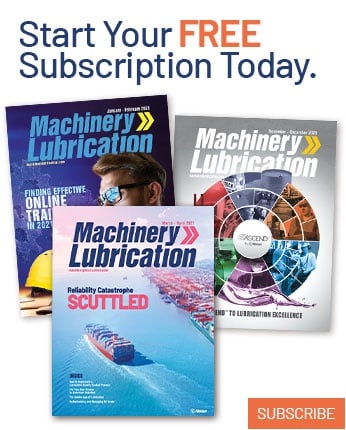