While value stream mapping (VSM) and kaizen events are often the most misused of the lean tools, 5-S is the most misunderstood lean tool. Here are some 5-S thoughts and considerations to review.
Common 5-S issues and mistakes:
- The 5-S’s are about creating a safe, clean and organized work environment which eliminates waste including losses due to unsafe work conditions – there is no sixth S for safety.
- Successful lean implementations occur in organizations where the management team demonstrates leadership. This means starting 5-S in the office first, or at least implementing it simultaneously in the office and factory. There are organizations that say they have been doing lean for years yet have never applied it to the office. These organizations then wonder why they are showing “little or no progress” with their lean implementation.
- Demonstrating leadership also means managers and supervisors never “just walk by” an unsafe or dirty condition. This leadership helps develop a lean culture where no one in the organization would knowingly walk by an unsafe or dirty work condition. This lean culture is the foundation of world-class organizations.
- Organizations generally require their factory associates to clean up their areas during or at the end of their shift. Yet, in the same organization, a third party is brought in or used to clean up the offices of the administrative associates. If we want teamwork, we need one set of rules.
- The 5-S red tagging event is a “one-time” activity, not an annual activity that allows us to make excuses for what our area looks like during the year. If our people are properly trained in 5-S, they will protect “their area” from things that do not belong there and move things to the “5-S parking lot” when they are no longer needed.
- The third S, sweep or shine, also means that we will develop ways to prevent things from getting dirty. It is not just a matter of cleaning up every day. What can we do to prevent things from getting dirty so clean up is not required?
- When 5-S fails, it fails because we did not properly implement the fourth S (schedule/standardize) and there was no follow-up using the fifth S (sustain).
- If you want everyone to clean up, make sure everyone has his or her own cleaning supplies.
- Over time, the business will develop its own 5-S expertise when new 5-S safety, organizing methods, clean-up techniques and other 5-S methods are established. Audit procedures and scoring should be adjusted to these developments, thus raising the bar to the new baseline.
- One of the required measures for the success of your 5-S implementation includes never having to clean up in advance of customer or other special company visitors. Think about it: When we tell our associates they must ”clean up” in advance of a visitor, what are we telling them?
About the author:
Larry Rubrich is the president of WCM Associates LLC. For more information, visit www.wcmfg.com or call 260-637-8064.
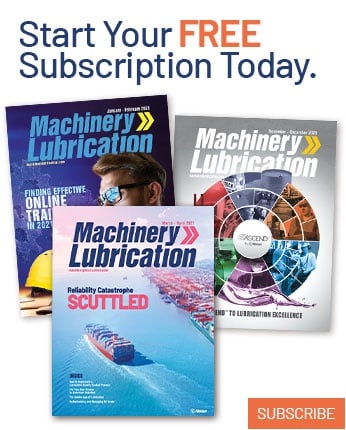