October manufacturing data for Brazil showed a deterioration in business conditions within the sector, following a slight improvement during September. Output and new business fell, while a 13-month period of employment growth came to an end. Despite weaker market demand, firms continued to raise their charges in order to pass on higher input costs to customers – a factor which some firms linked to lower sales levels.
Sinking to 49.5, from 50.4 in September, the headline seasonally adjusted HSBC Brazil Manufacturing Purchasing Managers’ Index (PMI) signaled a slight decline in the health of Brazil’s manufacturing economy. Data have pointed to worsening operating conditions in two of the past three months.
For the third month running, Brazilian manufacturers reported a reduction in new order receipts during October. Although the rate of contraction accelerated, it remained modest. Companies stated that lower demand, strong competition and uncertainty surrounding recent elections all underlay the dip in new business. Some respondents also mentioned that their charges were too high to be competitive. New export orders declined at a faster rate than total new work during the latest survey period.
Backlogs of work across the Brazilian manufacturing industry continued to be depleted in October, and at the fastest rate since June last year. Panel members linked lower levels of unfinished business to another decline in new orders. Work-in-hand has fallen for four straight months.
Brazilian manufacturers halted their intake of new staff in October as workloads decreased further. Consequently, a 13-month period of job creation ended as the vast majority of monitored companies maintained personnel levels since September.
Input acquisitions at Brazilian manufacturers were cut more sharply in October, which panelists linked to a combination of fewer new orders and stock depletion policies. Pre-production inventories fell further as a result, although the rate of decline remained only slight.
Average vendor performance continued to deteriorate at the start of Q4, despite weaker demand for inputs. Firms cited low capacity at suppliers as the main reason for longer lead times.
Both input and output price inflation was moderate in October. Anecdotal evidence suggested that higher input costs largely reflected increased prices for raw materials, particularly cotton, metals and certain food-related items. Meanwhile, reports indicated that firms raised their charges to cover growth in their average cost burdens.
Commenting on the Brazil Manufacturing PMI survey, Andre Loes, chief economist for Brazil at HSBC, said: “Despite the strength of the labor market and the solid expansion of domestic credit, which have supported robust growth in domestic demand, the Brazil HSBC Manufacturing PMI fell below 50 in October, which implies in a small contraction of the manufacturing sector. The headline PMI index is now at 49.5, against 50.4 in September and 53.7 in October of last year, with many component indices falling below the 50 mark. Considering that final domestic demand remains very strong, it seems likely that the combination of weak external demand and growing competition from imports is starting to take its toll on activity in the manufacturing sector, which would explain the weakness in the latest PMI numbers.”
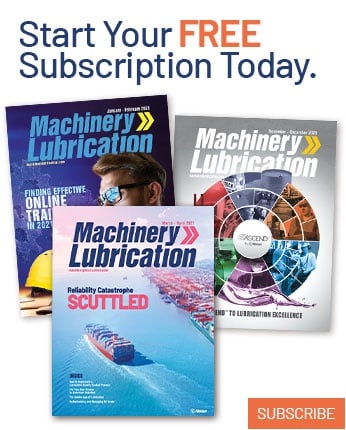