The economic downturn has incited many companies to take a closer look at how they can reduce their day-to-day operating costs. In many instances, a personal protective equipment (PPE) assessment can help maximize a company’s strengths and identify opportunities for improvements that can positively impact the bottom line.
The importance of employee input
Almost any type of assessment should begin with a plant walk through to gain input from the workers and supervisors who perform on-the-job tasks every day. These individuals can provide insight into the various processes involved and whether the PPE used is providing the protection and performance required.
By gathering information from employees, management can learn about the critical factors associated with each task and any concerns that may impede worker productivity. If, for example, employees do not have hand protection that provides the level of cut protection they need, they may perform tasks more slowly because they lack confidence in their ability to safely do the job.
If their hand protection products do not provide sufficient grip to securely grasp wet or oily objects, their performance may be hampered by a concern about dropping and even breaking objects. Many other factors can affect worker productivity, including apprehension about punctures or abrasions or whether PPE will provide the necessary heat or thermal protection.
The comfort factor
A PPE assessment will determine whether workers’ PPE is comfortable enough for them to perform their tasks to the highest level.
An assessment conducted at a white goods manufacturer revealed that workers were wearing their safety gloves for a short period of time and discarding them because they were uncomfortable and did not provide the dexterity needed. This premature disposal was costly for the company as the gloves still had serviceable life.
Based on the results of the PPE assessment, the manufacturer supplied workers with ergonomically designed gloves that were comfortable enough that workers preferred to wear them – and continued to wear them to the end of their expected life. Even though the new gloves cost more initially, the manufacturer was able to save over $100,000 in glove replacement costs during the first year.
Injury prevention
Injury prevention represents another opportunity to impact the bottom line. When companies can reduce injuries, they decrease their medical and indemnity costs and boost productivity because workers have less lost time.
A PPE assessment gives companies the ability to determine if employees are using the optimum solution to protect them in their working environment. By analyzing the critical factors associated with each task, the assessor can make recommendations to eliminate potential injuries and PPE misapplication.
Hand injuries at a metal processor, for example, were costing the company more than $500,000 each year. The company also paid $100,000 to purchase the gloves.
Based on recommendations resulting from the PPE assessment, the company supplied workers with gloves that virtually eliminated injuries. While the resulting solution was more expensive initially, the company saved over $150,000 based on reduced medical costs and related expenses.
Reducing waste
Productivity is directly impacted by the amount of waste a facility produces. Reducing waste in the form of defects or lost time can significantly drive down operating costs. A PPE assessment can identify solutions that can substantially reduce the amount of waste and the associated costs that may be present in the current work environment.
Gloves, for example, may produce lint that flaws the surface of a product and results in the product being reworked or discarded. Workers may drop and break products because their gloves do not provide sufficient grip. Employees may remove their gloves and don them later because they do not provide the dexterity for a specific task, such as recording data on a computer.
All of these scenarios are costly and waste worker time. Even though a process such as donning and removing gloves may require only seconds, when the procedure is repeated several times each day, the amount of wasted time accumulates quickly.
PPE distribution
An assessment will analyze current PPE usage and how companies dispense products to employees. In some cases, employees may have unlimited access, which allows them to acquire the PPE they want any time they choose.
The lack of controlled distribution may result in higher PPE costs because workers discard products prematurely. Employees may also suffer more injuries because they select the wrong glove for the task.
An assessment can help determine the proper control mechanisms, such as vending machines, that manage PPE distribution by requiring workers to use a key card to gain access. Another option may be to designate a central store where employees must sign out PPE products. This alternative allows management to monitor how often workers obtain PPE and provides insight into the specific products and costs associated with the program.
Training
A PPE assessment often shows that companies need to increase their focus on employee education. In many instances, companies conduct some type of PPE training. But, the training may be limited to an hour long session that presents the same information to everyone.
The PPE assessment will help identify training tools that better educate individual employees about the specific tasks they perform every day. When the proper training tools are put into place, workers have no question about what solutions they need for their jobs and the protection and performance characteristics they offer. Companies may employ a variety of mediums to provide this type of information.
Continuous Improvement
While an initial PPE assessment will identify cost saving opportunities and provide specific recommendations for improvements, companies must commit to conducting follow up assessments at regular intervals to determine if the solutions implemented are working.
Follow-up assessments will also allow companies to identify new solutions that can further improve day to day operations and facilitate changes that will make their work environment even more efficient.
About the author:
Mike Kimberley is the director of strategic account development at Ansell Healthcare Inc. Headquartered in Red Bank, N.J., Ansell Healthcare is the leading provider of hand and clothing apparel, along with productivity solutions that enable companies to achieve and surpass their cost and productivity objectives. Working directly with plant personnel, Ansell uses its experience, knowledge and proven products to develop programs that guarantee results in the areas of safety and efficiency. For more information, visit www.ansellpro.com.
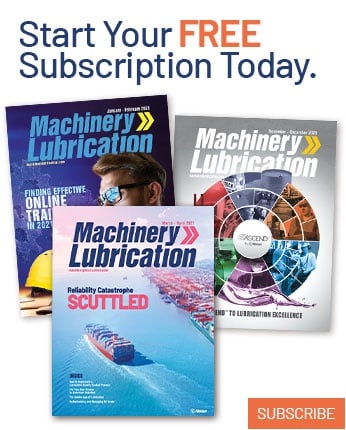