Airbus SAS’s head of operations, Gerald Weber, is taking lessons from his former employers in the car industry to cut production time on the A350 model and avoid the years of delay the plane maker suffered on the A380 program.
Weber, who has worked at Daimler AG, said he helped cut back on customization of the wide-body jet, changed the way internal systems and the fuselage are combined and got designers, engineers and customers to cooperate from the aircraft’s inception to identify potential fixes.
“Everyone is working more closely together on the A350,” Weber said in an interview at his Hamburg office overlooking the northern German city’s port entry. “On the A380, each team would design one part and then throw it over the fence.”
Airbus is seeking to avoid the spiraling expenses of the A380 superjumbo, where production delays pushed development costs beyond $20 billion. The challenge of the A350 is to create Airbus’s first-ever fuselage from composites, a decision the company made after Boeing Co. opted for the material on its 787 Dreamliner. Boeing had to postpone the plane’s entry into service five times.
The composite material’s complexity is compounded by increasingly sophisticated electrical systems to accommodate in- flight communications and custom design requests by airlines, making it harder for jet makers to keep their design targets.
Airbus wants to deliver the first of its A350s to Qatar Airways Ltd. in 2013, and the Toulouse, France-based company has 530 orders from 33 customers for the jet. Boeing’s 787 performed its first flight to Europe yesterday for the Farnborough Air Show, which starts today.
One change Airbus made on the A350 design was to pre-assemble the wiring and tubes for hydraulics, electronics, water and waste, air conditioning and oxygen outside into a so-called crown module and slot it into the fuselage rather than separately carrying every piece into the body. The process aims to shave as much as 20 percent off assembly time, Weber said.
Airbus is studying the jet’s designs on a so-called mock-up of a fuselage section that includes some seats, electrical systems and sleeping compartments for the pilots, to complement the digital master plan. The A350 will be assembled in Toulouse, with the tail section coming from Spain, the wings coming from the United Kingdom and Germany providing large parts of the fuselage.
Weber, who splits his work time between Hamburg, Toulouse and regional production centers in Germany, France and Spain, said he’s taken workers to study production at factories of Porsche AG and Volkswagen AG. Airbus has put more than 2,000 workers at its Hamburg facility through a so-called lean academy to let them study improved production processes.
Among the lessons Airbus can learn from carmakers are lean manufacturing and standardization, Weber said. An A350 typically has more than 45,000 different brackets to fasten cables, a number Weber said he’d like to cut back to 5,000 eventually.
“It’s a brutal act to drive engineers, they always want to be creative,” said Weber, who started his career as a toolmaker in southern Germany making components for the car industry.
Airbus chief executive officer Tom Enders has said the company will have to work hard to meet its deadlines on the A350, a challenge Weber attributed mainly to the lessons the company has to learn from working with composites. Airbus consumed some of its time plan after overhauling the plane’s design plan to include more of the lighter material, he said.
“The decision was good to move to carbon fiber, you have to start and learn,” said Weber. “The tolerances of the parts are another risk ahead of us.”
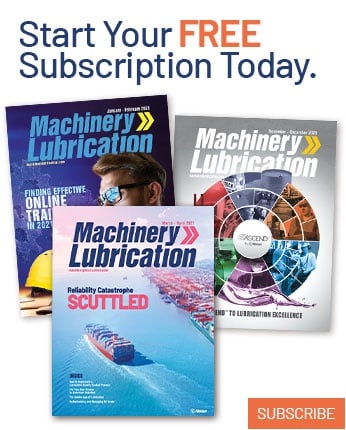