It started as a modest dream between three friends. Recently, the vision became reality with the opening of Green Planet Farms, a $40 million, 195,000-square-foot soy protein isolate (SPI) manufacturing facility in South Sioux City, Neb.
As an ingredient manufacturer, Green Planet Farms’ main focus is to serve organic and non-genetically modified protein isolates to food and beverage producers worldwide. Green Planet Farms is unlike other SPI manufacturers, who begin with partially defatted soy flour and rely on hexane (a gasoline by-product) during the extraction process.
To transform soybeans into healthier, minimally denatured and 100 percent soluble protein isolates, Green Planet Farms begins with soybeans that have been milled into full-fat soy flour. Its patent-pending, warm-water process, known as G2O, then naturally extracts the protein in the flour – separating it from the fiber, fat and sugar. This process pumps the elements along through a network of large stainless-steel vessels, and then drops the extracted liquid protein into a 130-foot tall spray dryer. Once the substance is dried, the isolate is packaged and sent to food processors for a host of products, such as protein shakes and snack foods.
As an ingredient manufacturer, Green Planet Farms’ main focus is to serve organic and non-genetically modified protein isolates to food and beverage producers worldwide.
Due to this organic process, the Green Planet Farms dry soybean protein has a more stable nature – something the market has not previously seen. This means that when drinking a protein beverage, for example, the protein doesn’t sink to the bottom of the glass and require frequent shaking or mixing. The protein also has no detectable flavor, a significant advantage over other proteins that carry a distinct soy aftertaste.
In addition to the quality of the isolate, the company stands out from other producers due to its passion to leverage a highly sustainable production process. Ordinarily, companies talk about a “triple bottom line” – people, planet and profit. But Green Planet Farms does more than just talk about protecting the environment. The three key people who serve as the foundation of the company help keep sustainability a leading principle for every decision that’s made.
As a user of raw materials, the company’s sustainability commitment starts at the beginning, with small farmers who are growing organic produce. These farmers are able to prosper from the land without using artificial fertilizers and chemicals. Instead, the ground gains its strength from proper growing techniques. This commitment to sustainability extends throughout the manufacturing process. All steps, farming through final ingredient processing, are completed using organic methods, which allows for quality products with a minimal footprint on the environment.
“Our entire company – warehouse employees to top management – shares the same core value system when it comes to sustainability,” said Susanne Stoeger-Moore, board chairman and chief marketing officer, Green Planet Farms. “We pride ourselves on partnerships with organic farmers, as well as clean processes and facilities. Sustainability goes all the way from the air we breathe to the energy and methods we deploy for the safety and health of our employees.”
Challenge
Green Planet Farms’ Nebraska facility was only a concept several months ago. Back then, the team of three knew they needed a large facility for their growing business.
“As a pilot, our primary challenge involved migrating from a lab environment to a full-scale, automated manufacturing facility,” said Stoeger-Moore. “There were general ideas for how the production process should run, but as with most pilots, transitioning from a lab environment requires maximum design and manufacturing flexibility.”
“Upon starting this project, we knew that precise process control was important,” said Tim Foster, vice president of engineering, Green Planet Farms. “Our goal was to hire fewer total employees, but more highly qualified individuals. The control system would need to be extremely advanced, yet require minimal training and maintenance so our team members could focus on critical areas of the business.”
Another concern was cost. As a small growing business, Green Planet Farms needed a cost-effective solution, complete with accurate project estimates that proved themselves upon delivery.
The selection process involved two primary phases. One was to select the automation hardware, and the second was to decide who would engineer the system. When selecting the automation system, not only were the instrumentation and control system pieces critical, but the plant also needed wireless capabilities to support the small team.
Solutions
After reviewing bids from a variety of system integrators and automation providers, Green Planet Farms chose ESE Inc. and Rockwell Automation. Headquartered in Marshfield, Wis., ESE Inc. is a Rockwell Automation PlantPAx solution provider for the food and beverage industries.
“We turned to Rockwell Automation and ESE Inc. as they share our strong commitment toward environmental stewardship and have considerable experience implementing innovative manufacturing processes,” said Stoeger-Moore. “Additionally, Rockwell Automation is a recognized leader in corporate responsibility, and that’s important to our company.”
For its new facility, the company chose the PlantPAx process automation system. The PlantPAx system is based on the Rockwell Automation Integrated Architecture platform – delivering a unified process, discrete and information solution. Also, the new process control system centers itself on the Allen-Bradley ControlLogix programmable automation controllers (PACs) from Rockwell Automation. Unlike conventional controllers, these PACs leverage common development tools, network protocol and service-oriented architecture.
Not only does the PlantPAx platform manage more than 100 batch and continuous process phases designed to separate and dry the soybean isolates, but it also integrates with the company’s climate control system, and proprietary equipment and processes. Additionally, the platform’s human-machine interface (HMI) software helps the company meet its track-and-trace requirements.
The tightly integrated relationship between Rockwell Automation and its partners – Endress+Hauser and ProSoft Technology – also solidified the automation solution. Both companies are part of the Rockwell Automation PartnerNetwork program.
“Seeing how well the Rockwell Automation systems integrated with Endress+Hauser instrumentation and ProSoft Technology wireless gave us a high level of confidence in how our plant would function,” said Foster. “The partnerships and experience offered by Rockwell Automation rivaled other vendors because we had more flexibility in the areas we chose to incorporate.”
With preferred integration between Endress+Hauser process instruments and the PlantPAx system, Green Planet Farms received assured interoperability. The relationship provides a wide range of pre-integrated, pretested, standards-based measurement, automation and information solutions – making it an easy decision for the facility to use Endress+Hauser transmitters, meters and sensors.
Wireless was a main concern for Green Planet Farms from the start. However, since this concern was brought up in the early planning stages, ESE and Rockwell Automation were able to implement it across the plant.
“With the ProSoft Technology wireless capabilities, our operators can go anywhere in the plant where there is a problem,” said Foster. “While they are assessing one problem, operators don’t lose the ability to monitor the rest of the process.”
In addition to wireless capabilities, the plant transfers data across three different networks – EtherNet/IP for HMI connections and integration with the proprietary IT system, ControlNet for the processor and I/O platforms, and DeviceNet for the motor control center. These networks are based on a common language called the Common Industrial Protocol (CIP). With no translation, routing or special programming required between networks, Green Planet Farms can get the real-time information it needs throughout the enterprise.
ESE and Rockwell Automation were heavily involved and integrated in this project. They were able to provide training for Green Planet Farms’ personnel, helping them become acclimated to the system and leverage its advanced features.
“On both sides of this project, everyone knew what was going on with the project at all times, and that is the most effective way for a new project like this to be executed,” said Foster. “In addition, the standout customer service by both companies was a huge bonus. The people that we had on-site were highly capable of doing any task that was needed.”
Results
“As far as plant start-ups are concerned, this was the best start-up I’ve ever seen,” said Foster. “ESE Inc. saved two weeks of engineering time just by leveraging Rockwell Automation add-on instructions, and the reusable code will help us as we expand our operation.”
With one platform controlling all segments of the facility, much less training is needed for employees and responsibilities for different processes can be shared by multiple people. This also cuts down on the number of workers Green Planet Farms needs on-site, so more dollars can be allocated to attracting and retaining talent.
“This new system also allows our workforce to leave the control room and be an active participant on the plant floor,” said Foster. “As a result, all members of our team can fully engage in making safety a priority.”
The control system allows Green Planet Farms’ engineers to remotely monitor all elements of the process and very quickly make any necessary modifications. These process control improvement helped the company exceed its production goals by 15 percent. The system’s testing and reporting capabilities confirmed complete product integrity, which includes the protein’s quality, consistency and efficiency. As a result, the plant operates a continuous process for 20 hours per day – leaving the remaining four hours for cleaning.
Additionally, process energy recovery was incorporated into the facility to measure the outgoing waste materials. By-products are now able to be used in later stages of development to shrink the carbon footprint. Sustainability wasn’t forgotten in the building structure, either. Computer-controlled lighting systems and energy-efficient roofing have helped reduce energy costs, and recycled concrete and steel were used as building materials. Office furniture purchased was even checked to be green and environmentally friendly.
“At the end of the day, ESE Inc. and Rockwell Automation really exceeded our expectations,” said Stoeger-Moore. “Both companies share our core values and were our real partners in this project. That is so refreshing in a world where customer service is often forgotten.”
Based on the success of this plant, which opened in November 2008, Green Planet Farms plans to expand its facility and open another organic soy processing plant in 2011. The second facility is also going to be built on the PlantPAx process automation system.
For more information on Rockwell Automation products and services, visit the company’s Web site at www.rockwellautomation.com.
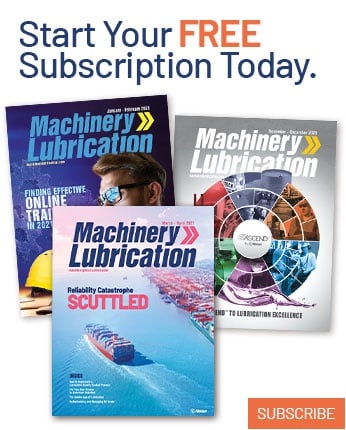