Zero-waste operations from SABMiller breweries is now becoming a possibility.
Much of our waste can be a valuable resource for farmers and food producers, as well as be a potential energy source. We aim to minimize the amount of waste we send to landfill, and in doing so are saving money and reducing its environmental impact.
The issues
The increasing costs, and in some cases scarcity, of raw materials across the globe has led companies such as SABMiller to focus on the efficiency of their resource usage and maximize the value extracted from their raw material supplies. To date, research has investigated the alternative uses for solid wastes either within our manufacturing process or by selling them to other industries that are able to utilize it.
At the same time, growth in population coupled with economic growth, has led to a notable increase in the amount of waste being generated globally. These two aspects, in conjunction with the pursuit of improved living standards, the dwindling availability of landfill sites and increasingly punitive legislation, have led to a situation where it is becoming prohibitively expensive to dispose of solid waste streams.
Consequently, there is a strong incentive for SABMiller to minimize the amount of waste produced during the production process and to reuse or recycle the wastes that are unavoidable. In regard to breweries, the majority of wastes that are produced are recyclable or reusable to some extent.
Why this is a priority
We aim to use our resources efficiently and limit the disposal of waste to landfill. We follow the principles of the waste hierarchy to reduce, reuse and recycle our waste in a more efficient and ultimately value-enhancing way. We believe that there is an opportunity for us to use more of our waste as a valuable resource, particularly as energy sources to reduce our dependence on fossil fuels.
The approach
Just under two-thirds of our waste is organic material produced as a by-product of the brewing process. This includes spent grains, waste yeast and trub (a residual created from brewing). The remaining waste is made up of damaged packaging (broken bottles, caps, cardboard and so on), kieselguhr (a filtration medium), effluent sludge from wastewater treatment, boiler ash and other non-recyclable waste.
We strongly believe we should manage the materials that other companies regard as waste. For example, segregated broken glass bottles can be recycled and turned into new bottles, while some organic waste can be used as animal feed or fertilizer.
We believe that organic by-products from brewing can be used as a resource and are constantly looking for new opportunities in this area.
Performance 2010
Increasing recycling: Last year, we generated 2.8 million tonnes of waste, of which 96 percent was recycled. The proportion recycled has increased slightly from last year and remains a high level. At MillerCoors, 99 percent of all brewery waste – including glass, paperboard, plastics, metals and by-products – is recycled or reused. This has largely been achieved through the commitment of MillerCoors’ employees.
Making the most of our waste: Spent grains are often sold as a relatively low-value animal food. However, we believe these grains could be better used as a source of energy for the brewing process through direct combustion, the generation of biogas or the production of fuel alcohol.
We’ve invested in a public-private partnership to fund the BBSRC Sustainable Bioenergy Center. Research at the center will cover several stages of bioenergy production – from widening the range of production sources to growing source crops more efficiently. The center also will analyze the life cycle and distribution of potential sources to ensure their economic and social viability. The research will look in particular at lignocellulosic conversion to ethanol (LACE) from spent grains.
There are further opportunities to use waste agricultural biomass as a fuel for boilers. SABMiller India leads the group in this area. It now has three breweries in which boilers are entirely or partly fired by a range of agricultural wastes including rice husks. In addition, some breweries in the group are already achieving 10 percent energy self-sufficiency by using energy generated from waste water treatment.
USA snapshot: Achieving zero waste at MillerCoors
MillerCoors has set itself a challenging target to find new opportunities to reuse, reduce and recycle brewery waste. In a single year, the business reduced the total amount of waste sent to landfill by more than 20 percent and met its 2015 waste goal in 2009.
Three breweries – at Elkton in Virginia, Trenton in Ohio, and Irwindale in California – achieved their goals of zero waste to landfill during this past year. The breweries have reduced solid waste by reducing usage, recycling or finding reuse streams for a broad spectrum of materials ranging from spent brewery grains to filter powders such as kieselguhr (a filtration medium). The Elkton brewery recycles or reuses 99.6 percent of its wastes. The remaining 0.4 percent goes to the waste-to-energy facility.
Global snapshot: Nearing zero waste to landfill in Panama
In 2004, a total of 17 percent of the solid waste – such as cardboard, paper, plastic, PET bottles, wood pallets, aluminum cans, paper and plastic bags, and various metals various – produced at Cervecería Nacional’s brewery in Panama was sent to municipal solid-waste landfills.
With a target to achieve zero percent of waste being sent to landfill, Cervecería Nacional embarked on a campaign to further reduce, reuse and recycle the waste produced by their brewery. This began with an inventory of the brewery which helped to identify the recyclable potential of waste produced. This helped to reveal the quantities, the types of wasted product, the size and the site for collection of the materials.
Following the inventory, a strategy was formulated to help minimize the amount of waste sent to landfill. This included purchasing baskets, tanks and carrying carts to assist with the collection and classification of recyclable products. In addition, a number of activities were undertaken to help raise employee awareness of recycling and waste management.
The main result of this initiative has been the significant reduction of waste produced at the brewery. In 2009, only 1.05 percent of the waste produced was sent to the municipal landfill (compared to 17 percent in 2004). This is estimated to equate to a reduction of 1000 tonnes of landfill waste a year. In addition to landfill savings, the initiative has also helped the creation and growth of the recycling industry in Panama and has allowed Cervecería Nacional to gain additional income from selling recyclable materials.
Reviewing progress on our sustainable development priorities
Download Sustainable Development report PDF (2.32MB)
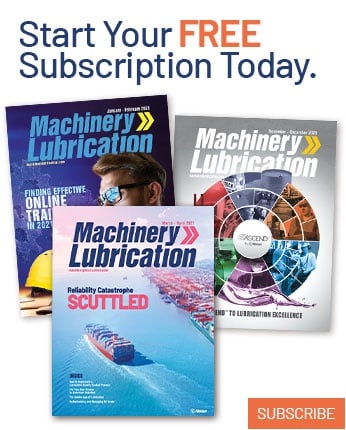