Members of Xerox’s leadership are principal advocates for using Lean Six Sigma to institute change in everyday decision making involving everything from manufacturing to finance. Under visible commitment from former and current CEOs Anne Mulcahy and Ursula Burns, there has been a cultural shift at Xerox toward making Lean Six Sigma inherent in everyday project selection and problem solving.
The solid ink Jetstack operation team in Wilsonville, Ore., is a marked example of the progression from initial adoption of Lean Six Sigma ideas to embedded principles in operations that are driving business results for Xerox. Solid ink technology utilizes solid ink sticks in lieu of fluid ink or toner powder. After the ink stick is loaded into the printing device, it is melted and used to produce images on paper in a process similar to offset printing. Jetstacks are stainless steel plates that route ink from reservoirs to the jets that dispense the ink from the printer. The steps in the manufacturing process of Jetstacks are detailed and precise, and the team has recently completed several Lean Six Sigma projects that optimize the manufacturing process to meet the strict requirements in a more efficient way.
The first project addressed the clean room portion of the Jetstack manufacturing. The team needed to add new equipment to increase capacity, but had little floor space to do so. Increased capacity also created a prime opportunity to identify overall efficiency improvement opportunities. Lean Six Sigma black belts from other Xerox locations visited Wilsonville to lend expertise, providing training and project guidance.
A DMA (define-measure-analyze) blitz, commonly called a kaizen, was used for the project – leveraging Lean Six Sigma tools in a condensed time period to deliver immediate, tangible results. The team began by mapping the Jetstack manufacturing process step by step for a bird’s eye view of constraints and areas of the process which presented opportunities.
After the team was ready to make informed, knowledge-based recommendations, a brainstorm led to approximately 200 improvement ideas. A benefit/effort matrix was used to identify the solutions that would make the most impact. End results included 220 reclaimed square feet of room for new equipment and more than $1 million in capital savings due to reduced cycle times and improved efficiencies.
By the time a second project was initiated, the team had matured to the point of training employees and leading projects independently. The cultural shift toward making Lean Six Sigma “the way of work” had eliminated the need to obtain black belt resources from other locations.
The pre-clean room manufactures a part of the Jetstack system proprietary to Xerox. The Lean Six Sigma project aimed to build on the success of the clean room kaizen by increasing throughput in the pre-clean room without investing in additional equipment. Further goals of the project included reducing opportunities for injury, scrap and waste.
The team was able to reduce scrap, improve organization and create a more efficient use of floor space and labor, saving Xerox approximately $450,000. The project also helped reduce negative impact on the environment by adding recycling efforts and identifying unnecessary power consumption. In addition, the team met the goal of decreasing opportunities for employee injury.
Having Lean Six Sigma expertise in-house at the Wilsonville facility has been a valuable asset, allowing the team to review the operation as a comprehensive system and deliver significantly more efficient and robust processes. Before Wilsonville built a strong, Lean Six Sigma-trained team, these inefficiencies may have fallen through the cracks. But now, they are addressed and optimized.
About the author:
Jeff Rigotti is the Jetstack engineering manager at Xerox Corporation’s plant in Wilsonville, Ore. To learn more about Xerox, visit www.xerox.com.
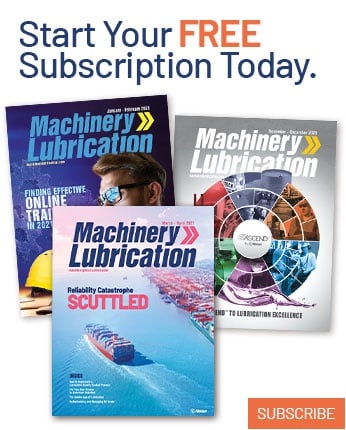