Six cement plants received special recognition for their commitment to improving the environment and their communities at the ninth annual Cement Industry Environment and Energy Awards, presented by Portland Cement Association (PCA) and Cement Americas magazine at PCA's Spring Meeting in Chicago on April 27.
The awards honor individual cement facilities that exemplify the spirit of continuous environmental improvement and support this spirit with action. These plants went beyond government regulations and local laws to ensure that their processes and policies contributed to making their communities better places to live and work.
"The United States cement industry is dedicated to producing a superior product while challenging manufacturing policies and procedures to improve energy efficiency. The companies also recognize their role in making their local communities better places," said Brian McCarthy, PCA president and CEO. "The actions taken by these plants and many others are at the fore-front of manufacturing technology and position the industry as a key contributor to the development of the latest energy expertise."
Six categories recognized plants throughout the United States (listed by category, company and plant location):
- Overall Environmental Excellence: Lafarge North America Inc., Bath, Ontario
- Outreach: Holcim (US) Inc., Theodore, Ala.
- Environmental Performance: Lafarge North America Inc., Sugar Creek, Mo.
- Land Stewardship: CEMEX, Xenia, Ohio
- Innovation: Lafarge North America Inc., Tulsa, Okla.
- Energy Efficiency: CalPortland, Colton, Calif.
Twenty-six cement plants in the United States and Canada were nominated for the awards.
Overall Environmental Excellence: Lafarge North America Inc. – Bath, Ontario
In 2009, the Lafarge Bath plant completed a range of environmental and energy efficiency projects. As part of its climate change and energy efficiency programs, university researchers planted hybridized willow species at the facility and other crops as possible renewable biomass sources. The facility also worked with local farmers to raise crops for a future trial biomass burn, and more than 950 bales of plant material have been collected. The installation of new blower technology allowed the plant to improve kiln operation and increase its utilization of petroleum coke, an oil refinery byproduct. These actions will reduce sulfur and carbon dioxide emissions and lower fuel consumption. With additional kiln operation and quarry changes, the facility has nearly eliminated cement kiln dust (CKD) production. Likewise, the CKD monofills were improved because little to no CKD will be produced in the future. Lastly with the help of 250 local scouts, leaders, and parents, the facility planted 3,000 trees on the plant property for habitat restoration and climate change education and mitigation.
Outreach: Holcim (US) Inc. – Theodore, Ala.
The Holcim plant and its employees in Theodore support a range of environmental projects in their community. In 2009, plant employees were zone captains for cleanup of the Theodore Industrial Canal as part of the 22nd annual Alabama Coastal Cleanup Day sponsored by the Alabama Department of Conservation and Natural Resources. Seventy-one plant and community volunteers removed more than 1.5 tons of debris from the banks and waters of the Canal. The plant also worked with the Alabama Coastal Foundation in the evaluation of the shoreline of the Fowl River and continues to assist with the local Used Electronics Recycling Days. Nearly 200,000 pounds of unwanted electronic devices were collected in 2009.
Environmental Performance Award: Lafarge North America Inc. – Sugar Creek, Mo.
The Lafarge Sugar Creek facility completed a range of projects in 2009 to increase the amount of alternative raw materials and fuels used by the plant while continuing to keep emissions significantly below permit limits. By connecting to a third source in 2009, landfill gas replaced 17 percent of the plant's fossil fuels, which would offset more than 30,000 tons of carbon dioxide from coal combustion. Modifications to its alternative solid fuels facility allowed the Sugar Creek plant to double the percent of fossil fuel replacement--to 20 percent. In 2009, the facility utilized limestone fines from an adjacent quarry to replace more than 14 percent of the limestone needs of the kiln. The plant also substitutes 35.8 percent of its non-limestone raw materials with a range of non-hazardous industrial wastes such as bottom ash, boiler slag, foundry sands, and mill scale.
Land Stewardship: CEMEX – Xenia, Ohio
The CEMEX Xenia facility has approached its land stewardship tasks as a cooperative effort with the community, Cedarville University, and the United States Fish and Wildlife Service. In 2009, the plant and its partners began the first phase of the eradication of a 4.5-acre kudzu infestation, a non-native, invasive vine. After careful evaluation, a plant-specific, systemic herbicide was selected and targeted application completed. The eradication will help to return the area to native vegetation and to educate the local community on kudzu control and elimination. Another project with university student assistance is the monitoring of a 47-acre native grassland habitat at a former clay mine that will foster nesting habitat for grassland birds. The reclamation plan is based on United States Fish and Wildlife Service and Audubon Society guidelines which exceed mining regulations.
Innovation: Lafarge North America Inc. – Tulsa, Okla.
In 2009 the Tulsa Lafarge plant took advantage of an alternative fuel opportunity that builds upon a waste stream the industry has been using for years. Most tire-derived fuel use is based on used tires, but the Tulsa plant worked with Goodyear, Inc., to divert rubber manufacturing waste from landfills and into the cement kiln. The plant accepts bagged scrap rubber and malformed rubber components which are delivered to a mid-kiln injection system by way of a high angle conveyor. In addition, the plant utilizes 100 percent Biogas from a nearby landfill for the drying of raw materials and up to a 20 percent substitution of the kiln fuel needs.
Energy Efficiency: CalPortland – Colton, Calif.
The CalPortland plant in Colton completed several unique energy reduction projects in 2009. The facility has a comprehensive intranet site that displays energy performance information in dollars, energy units, and specific energy. Several new installation upgrades lead to tremendous energy savings. New high efficiency separator, baghouse, and material handling equipment will save nearly 7 million kWh annually for finish cement grinding; the completion of a kiln air leak reduction program will save more 5.7 million kWh; and the installation of a new cement terminal is expected to save more than 3.7 million kWh. These and other initiatives resulted in the plant scoring a perfect 100 through ENERGY STAR's EPI benchmarking tool. In addition, Colton has also established national accounts with suppliers which include energy efficiency as part of their contracts.
History of the Awards
The awards program was created in 2000 by the Portland Cement Association as part of its renewed environment and energy strategic plan for the U.S. cement industry. The awards honor activities conducted during the previous calendar year, and the program is open to any cement manufacturing plant in North America. Judges for the 2010 awards represent independent groups such as National Ready Mixed Concrete Association, U.S. EPA-ENERGY STAR, U.S. EPA-Office of Policy, Economics and Innovation, Cement Association of Canada, Cement Americas, U.S. Geological Survey, World Resources Institute and World Wildlife Fund.
About PCA
Based in Skokie, Ill., the Portland Cement Association represents cement companies in the United States and Canada. It conducts market development, engineering, research, education, and public affairs programs. More information on PCA programs is available at www.cement.org.
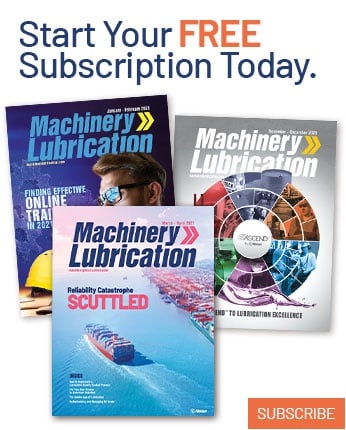