A few weeks ago, someone asked me, “How many hours should a maintenance planner plan for each week?” This is a great question, but I can only give a touchy-feely answer.
I’m hesitant to push maintenance planners into a numerical-type standard or quota. But, let’s first try to analyze this in a quantitative manner. A single maintenance planner should be able to plan for 20 to 30 technicians. Therefore, a planner needs to stay ahead of at least 20 techs on an ongoing basis. As a minimum, there needs to be enough planned work available at the end of the week to enable scheduling for the next week.
This could mean as much as 800 hours planned (20 techs times 40 hours per week). However, the plant’s preventive maintenance program also should be generating work orders that don’t need advance maintenance planning. Presume the plant wants to spend 20 percent of hours on PM tasks. That subtracts 160 hours and suggests each planner should plan 640 hours of work per week.
A variable that would increase the weekly planning hours is if the planner had to plan for more than 20 techs. Variables that would lessen the hours would be: if some techs were on vacation, sick leave, in training or unavailable; and, if plant emergencies or urgent work caused the techs to forsake the schedule to do unplanned work. For simplification, let’s consider these factors are a wash and stick with 640 hours.
At the same time, keep in mind that planners not only plan future work, but also review feedback on completed jobs in order to update job plans and file work orders. Thus, can a planner plan 640 hours of work each week while keeping up with job closeouts? I’m not satisfied with this quantitative analysis. I’d like every job to have someone look at it and examine the history file before any techs are assigned to the work.
Let’s proceed with a qualitative approach to maintenance planner productivity. There is no simple “number of hours planned” answer here. Consider first, the maintenance crews themselves. We want 20 techs (two crews of 10) completing 400 hours of work each week (minus carryovers, training or vacation). We don’t want a crew slowing down or speeding up based on the outstanding backlog. This isn’t the case with planners.
If there is a low backlog, they could spend more time planning each individual job. But if there’s a large unplanned backlog, it’s essential that they plan more work even if the plans aren’t very precise. A simple scope, craft skill, labor hours and list of parts used last time, if any, may be all the planner has time to put on each plan.
I’d push the planners to complete more plans if the unplanned backlog became too high. It’s essential that the scheduler be able to select jobs from the entire backlog even if some jobs only had rudimentary plans with hours.
The biggest improvement opportunity lies in scheduling. If I had to get quantitative, I’d insist that the planners plan all the reactive work each day. I’d look at the lower-priority proactive work in terms of some timeframe. For example, if the priority system dictated that crews complete Priority 3 jobs within two weeks, I’d want the planners to aim for a target of five days. This allows a crew time to schedule the work after planning.
This figure displays a traditional driver of productivity.
These last two figures show productivity driven by planning and
scheduling.
A strict numerical approach to productivity might miss the point of why maintenance planners exist (to promote crew productivity). I want the planner to keep the unplanned backlog under control by adjusting the time spent on the level of detail put into each job plan.
Finally, I’ve worked with slower and faster maintenance planners. Some could only keep ahead of 10 techs while others could plan for as many as 60. These were all good planners. The key was to balance the planners and techs.
All this information doesn’t provide a precise answer to the column’s topic, but at least it’s food for thought.
Doc Palmer is the author of the “Maintenance Planning and Scheduling Handbook.” He is a CMRP and has nearly 25 years of industrial experience as a practitioner within the maintenance department of a major electric utility. From 1990 through 1994, he was responsible for overhauling the existing maintenance planning organization. The resulting success played a role in expanding planning to all crafts and stations owned and operated by the utility.
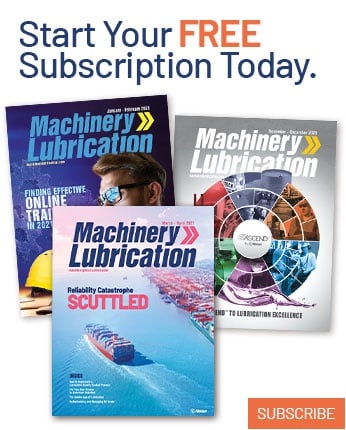