IBM on April 13 announced the opening of a new $30 million manufacturing facility at its Poughkeepsie, N.Y., site to produce the next generation of System z mainframes and high-end Power Systems servers.
The 56,000-square-foot facility, built inside an existing structure at IBM's 400-acre site in Poughkeepsie, features several innovations to conserve energy and improve manufacturing processes.
The facility will produce IBM's next line of System z mainframe computers and high-end Power Systems servers – based on leading IBM technology – that manage business operations from critical banking transactions to Internet workloads to the most demanding emerging new applications for clients worldwide. For example, more than half of Fortune 500 companies use IBM mainframes to execute daily business transactions.
"The new manufacturing facility in Poughkeepsie reflects IBM innovation in the design, testing and assembly of its mainframes and high-end servers," said Mike Desens, Poughkeepsie senior location executive. IBM Systems & Technology Group. "And it underscores our reliance on the skills and talents of our workforce, as well as a long-term commitment to a continuing presence in New York State and the Mid-Hudson Valley."
The new facility, in planning for more than three years, is designed more like a data center than a warehouse, with a strong emphasis on innovation and efficiency. The facility's features include:
- A closed loop system that circulates chilled water throughout the facility for air conditioning, systems cooling and other functions. A similar system is in use throughout the Poughkeepsie site.
- The new facility has a chilled water cooling capacity of 1,700 tons – constantly circulating through pipes, air conditioning, servers and cooling sources – and also uses localized system cooling through IBM's unique "Cool Blue" Rear Door Heat eXchangers. An energy-saving technology offered by IBM, this solution features a passive water-cooled door which mounts to the back of IBM systems to cool computer equipment exhaust air before it re-enters the data center operating environment.
- Thermodynamically-sound hot and cold aisles in the test area, placing systems front to front and back to back to maximize air flow and energy efficiency. The facility is designed so that the systems use fans to intake cool air in the front and then exhaust hot air out the back of the system. This optimizes data center thermal flow dynamics to eliminate hot spots and reduce energy consumption in the facility
- The latest environmental practices in temperature control and lighting, such as high-efficiency fluorescent lighting and occupancy sensors, to further reduce energy consumption.
- The plant also is ergonomically designed and built with noise reduction, cleanliness and material handling features for an improved employee work environment. For example, a new ceiling tile system helps reduce noise with minimal dust retention.
The facility is designed to handle the next generation of systems and the capacity and flexibility to manufacture future products. The first products for customers are expected to roll off the assembly line later this year.
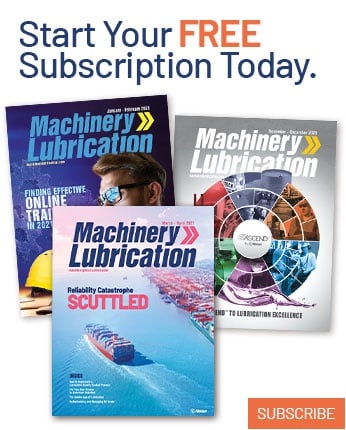