Lean manufacturing and continuous improvement, based on theToyota Production System, is now being applied to factory processes includinganodizing, metalworking fluids, cleaners, surface treatments and finish coatings.
Kaizen or continuous improvement is a never-ending process – there is no finish line.It is natural when applying the principles of continuous process improvement to initiallyfocus on people, equipment and tools,since we can use our basic senses to see what is going on.However, in the spirit of truly striving for perfection,kaizen can be taken to the molecular level.Technology is available to look at things we can’t see, feelor touch.
Using specialized monitoring equipment that looks intoareas of the factory that typically do not get enough attention, many markets includingtransportation, pipe & tube, office furniture, steel, heavy equipment and metalworking jobshops can benefit from this analysis.
One example is in the chemical processes a manufacturing company might use. Forexample, in a tube mill,data can be gathered on the tons of input, tons of goodproduction, scrap, tooling costs, mill utilization, coolant used, water used, man-hoursand energy consumption. Cost savings can be in any of these areas, but energyconsumption, water consumption and wastewater have been hot buttons in recent years.
Many factories get one large bill for gas and/or electricity,and they don’t really trackenergy use by process. For example, one Midwestern manufacturing complex thathas seven five-stage tunnel washers was firing up boilers to bring chemical baths up totemperature without paying great attention what was going on daily. When analyzed, the data indicated that bath temperatures were running at the high end of the controllimits. Also, the data showed that when operators arrived in the morning,theyimmediately fired up boilers and heated baths to temperature on average 30 minutesearlier than required for production. Similarly, at the end of the work day,boilers werenot turned off until the very end of the day when they could have been turned offapproximately 30 minutes earlier. As a result, policies for startup and shutdown wereset for all boilers,saving more thanonehour per day of run time per boiler. Annual energysavings exceeded $200,000.
A process audit can be done over a 30-day period to pinpoint where the problem isprior to making recommendations on how to correct the processes.
Here are the six steps that we have found to be successful when conducting an audit:
Step 1:Senior management approval. The first meeting is with a companypresident, vice president of operations or lean manufacturing champion. The typicaloutcome of this meeting is to identify a factory in the company’s system that mightqualify for an audit.
Step 2:Discovery day at the factory. A technical team visits the candidate factoryto determine if a process audit is appropriate. The objective of this day is to makesure that there is a high probability of success. During discovery day,the technicalteam will plan work that must be done to begin a process audit. This involvesdiscussions with the plant management and the maintenance department.
Step 3:The process audit. Working through the plant maintenance department,controllers, sensors and probes are installed. A phone line or Ethernet connection isrequired so that data can be monitored via the Internet. Installation is completed inone day. The process audit does not interfere with normal factory operations.
Step 4:Continuous improvement proposals. Using data gathered during theprocess audit, several proposals for continuous improvement are suggested. Theseare reviewed with plant management and senior management.
Step 5:Implement and document. The auditor is at thefactory 24x7 via technology gathering hard data, but the client’s workers mustimplement process changes. Typically,the auditorwill meet with the client every 90 days tocheck on progress and review data.
Step 6:Do it again. Continuous improvement is a never-ending process. After aprocess audit, the minimum subscription is aroundsix months. After sixmonths,the relationship continues on a month-to-month subscription,and acontinuous stream of process improvement projects are approved and implemented.
In conducting audits over the past year,we have discovered that a few simpletechniques go a long way toward a successful outcome:
1) Get your Internet connection in place early. Sometimes providing a simplephone line or Ethernet connection so process audit data is readily accessedvia the Internet takes longer than anticipated. Get this done early so the startof a process audit is not delayed. Often,your information technologydepartment wants to getinvolved for security reasons.
2) Have your maintenance department spend time with the audit team duringdiscovery day. They will need to install the controllers and probes thatgather valuable data and should be involved at the front end.
3) Assign a task force at the plant with a leader to meet with the auditorsevery 90 days. An outside auditor can gather data and documentimprovements, but the task force is at the plant every day. They have tomake process changes happen on the shop floor.
4) Keep senior management involved. Have the task force present results tosenior management every 90 days. It is best to have the plant task forcetake ownership and credit for the improvements realized.
About the authors:
Tom Fabekis thegeneral managerand Joe McHenry is the vice president of business development for Profit Finders, a professional auditing firm with headquarters in Strongsville, Ohio. Profit Finders offers a monitoring and data collection program that successfully identifies opportunities to reduce electricity, natural gas, water, waste treatment and chemical consumption.For more information, visit www.profitfinders.net. You may also e-mail Fabek at tfabek@profitfinders.net or McHenry at jmchenry@profitfinders.net.
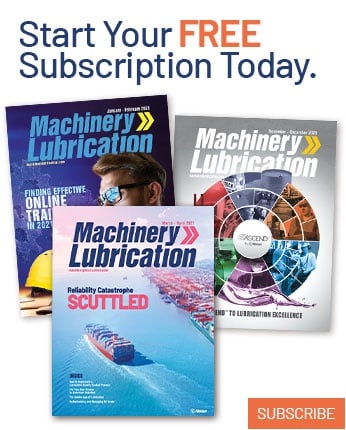