Just as cement is the binding “glue” in concrete production, the U.S. cement industry is the building block of the nation’s construction industry. Cement manufacturing accounts for 1 to 2 percent of U.S. industrial energy use, but more than 5 percent of the nation’s industrial carbon dioxide (CO2) emissions.1 The most energy-intensive step in modern cement manufacturing is the calcination reaction, which requires extremely high temperatures – up to 3,000 degrees Fahrenheit (1,700 degrees Celsius) – in order to transform limestone (calcium carbonate) into lime (calcium oxide), a necessary component of cement. CO2 emissions result from the combustion of fuel used to reach these high temperatures, but they also are produced as a by-product of this calcination reaction. Overall, the resulting emissions are disproportionately large when compared to those produced by other industries. With few viable alternatives currently available and the worldwide demand for cement increasing, investment in energy- and CO2-reducing technologies and processes in the cement industry represents one key opportunity to help the United States attain its energy and climate goals.
Figure 1. The Hoover Dam (background) used 3.25 million cubic yards of concrete to build, while the still-under-construction Mike O’Callaghan-Pat Tillman Memorial Bridge (foreground) will require a further 32,000 cubic yards of concrete.
Significance of the U.S. cement industry
The United States cement industry ranks among the top three manufacturers of cement in the world, behind only China and India. It directly contributes more than 17,000 jobs to the U.S. economy in addition to the hundreds of thousands of jobs involved in construction and infrastructure development.
Industry Stakeholder Workshop
In September 2009, the U.S. Department of Energy’s Industrial Technologies Program (ITP) convened at the Cement Energy and CO2 Reduction Opportunities workshop in San Francisco. The purpose of this collaborative two-day workshop was to help develop a national perspective to identify the opportunities, barriers and pathways to significantly increase energy efficiencies and reduce CO2 emissions from the cement production process. In support of this goal, the workshop gathered representatives of established cement industry leaders, including CalPortland, CEMEX, Lafarge and Lehigh Hanson; emerging cement technology entrepreneurs such as Calera, CalStar Products and Novacem; government entities including the National Institute of Standards and Technology, Environmental Protection Agency, and California Air Resources Board; and several national laboratories. Also invited were representatives from the Portland Cement Association, the National Ready Mixed Concrete Association, and a variety of other representatives from associated industries, academia and venture capital, as well as other interested parties.
Figure 2. Cement Industry Supply Chain (Source: 2008 Industrial Technologies Market Report)
ITP to release report on workshop findings
Based on input from the workshop participants, ITP will be releasing a report in the coming months that identifies:
- Opportunities to increase cement industry energy efficiency and reduce CO2 emissions using established, best-available technologies and policy instruments
- Long-term transformational technologies and supporting policies that have the potential to drastically reduce cement industry CO2 emissions.
More than 90 percent of cement manufacturing CO2 emissions is generated from the calcination reaction process and the combustion of fossil fuel (primarily coal). Overall, for each tonne of cement clinker produced in the United States, approximately 1 tonne of CO2 is released,2 well above the average release of many other countries with more efficient cement industries.3 In addition, U.S. cement producers use more energy per tonne of cement clinker produced than many other industrialized nations.4 While differences in cement kiln technology represent one reason for these disparities, the European Union, Japan and other regions have adopted other strategies to reduce their cement manufacturing energy and CO2 footprints, such as greater use of alternative fuels for kiln heating and broader substitution of cement clinker with less energy- and CO2-intensive materials, such as coal fly ash.
Figure 3. The U.S. cement industry consists of approximately 113 cement plants across 36 states. (Source: The Portland Cement Association)
The to-be-released ITP report will highlight proven actions cement manufacturers can take to make an impact in reducing energy intensity and CO2 emissions in the near term. These proven actions include the adoption of best-available technologies, such as dry kilns with the latest preheater-precalciner technologies, investment in combined heat and power and organic rankine systems, or increased utilization of alternative fuels and clinker substitutes in cement manufacturing. A variety of policies, regulations and financial incentives can help facilitate these options.
In addition to actions that can have near-term impacts, the report will highlight transformational technologies and supporting policies that have the potential to significantly reduce long-term cement production CO2 intensity and contribute to the climate goals. These technologies include the development of alternative cement material systems and material-processing methods, advanced processing agents, and novel carbon capture and storage technologies well-suited for the cement industry. Concerted fundamental science and process research and development (R&D) investigations will need to be concurrently initiated in the near term to allow adequate time for technology maturation and widespread adoption.
Charting a sustainable path forward
Cement will remain vital to infrastructure development for the foreseeable future. Existing cement processing methods will need to be transformed in order to meet the Obama Administration’s ambitious U.S. climate goals. While various programs sponsored by the Portland Cement Association, the Asia Pacific Partnership and the World Business Council on Sustainable Development have begun to address the environmental impacts of cement production, more creative methods and concerted R&D efforts will be required to meet the Administration’s goals. ITP is spearheading these R&D efforts in the cement arena to make cement manufacturing sustainable and the industry viable well into the future.
This article was written for the U.S. Department of Energy’s Industrial Technologies Program and appeared in the DOE’s Energy Matters newsletter. For more information, visit http://www1.eere.energy.gov/industry/.
References
1Department of Energy – Energy Information Agency: http://www.eia.doe.gov.
22007 USGS Minerals Yearbook: Cement: (PDF 241 KB).
3IEA Tracking Industrial Energy Efficiency and CO2 Emissions: (PDF 4.9 MB).
4Ibid.
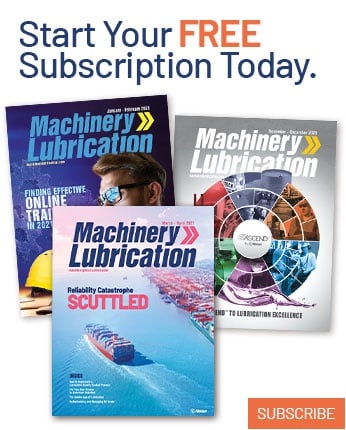