The ultimate goal of an SKF Integrated Maintenance Solution (IMS) is to increase the reliability and profitability of its customer’s plant. In an IMS partnership, SKF becomes an integral member of the plant’s operational team by assuming responsibility for creating and implementing an asset management strategy with the goal of increasing plant reliability and profitability. Backed by its experience and knowledge of mechanical and rotating equipment, SKF is uniquely qualified asset management partner.
Sharing Risks and Rewards
If you’re experiencing difficulty justifying reliability initiative spending, SKF can assist in preparing a customized business case based on your objectives and its proven experience in your industry. SKF IMS can provide documented ROI results in the paper, power, oil & gas, metals & mining, and food & beverage industries. In some instances, payback periods of less than one year have been achieved.
An IMS is a performance-based contract. Terms include a defined cost structure and mutually agreed upon performance metrics. With an IMS agreement, SKF shares the risks, enabling customers to achieve business goals with minimal financial risk. If the solution should exceed the performance goals, SKF shares in these rewards. In addition to engineering expertise and training, SKF assumes responsibility for bearing, lubricant, and seal supply and inventory management. With SKF as a partner, a manufacturer can focus on its core competencies while SKF optimizes the performance of the plant’s physical assets.
Elements of IMS
SKF takes a systematic approach to improving asset efficiency and effectiveness. As an extension of the internal team, SKF leverages its engineering resources to increase machine reliability and uptime, control maintenance costs and reduce total ownership costs.
Assessment of current maintenance practices and MRO parts usage identifies opportunities for improvement which become the basis for the pro-gram’s key performance indicators. On-site SKF personnel are selected to complement and strengthen existing maintenance and technical staffs.
Trouble-free supply involves controlling and reducing the costs associated with purchasing, supply, and inventory management and to assure availability of parts when needed.
Maintenance strategy review centers on understanding the business goals and assessing areas of criticality to ensure maintenance efforts are properly focused.
Proactive reliability maintenance involves establishing key performance indicators and operational review to monitor improvements based on predictive maintenance best practices.
Technology upgrades are part of each IMS contract. Improving machine performance may include machine redesign to incorporate the latest lubrication methods or implementation of on-line condition monitoring tools.
Machine maintenance is either supervised or performed by SKF engineers and includes precision laser alignment, balancing expert bearing installation and advanced lubrication systems are based on proven SKF techniques and industry best practices.
Training is an integral component of an IMS contract. Training is customized to suit the needs of the team. Training options include precision maintenance skills, bearing care, condition monitoring methods, lubrication practices, root cause failure analysis, and maintenance management.
Success in Pulp & Paper
After experiencing greater than of 100 hours of unplanned downtime in a single year, a large paper mill decided to enlist the assistance of SKF. Following the IMS improvement process, SKF experts conducted a mill-wide assessment to identify opportunities for improvement. The mill personnel liked what they heard and signed a five-year IMS performance-based contract. The contract included services for installation of both on- and off-line condition monitoring systems; engineering support; on-site technical support; maintenance staff training; and inventory management of bearings, lubricants and seals. This partnership resulted in incremental production increases of nearly 10,000 metric tons, adding $5.8 million directly to the bottom line over the first four years of the contract and led to a contract extension.
Conclusion
Enterprises are becoming more aware of the savings that asset performance management can yield in maintenance cost reductions, increased production, extension of asset life, and streamlined inventory management. However, conflicting priorities may make it difficult for them to establish priorities and develop strategies. As an objective third party, SKF utilizes its extensive knowledge and experience to establish priorities regarding organizational structure, maintenance strategies, technology, and processes, and instill an asset performance management culture.
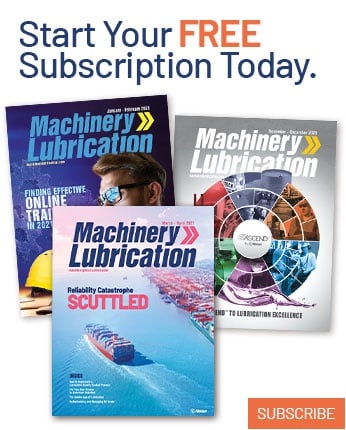