After looking at a photograph of the cracked handle, the commission wryly observed, “In our opinion, it would not have taken much force for the handle to break and cause the head of the hammer to fly off, creating a hazardous condition.”
What makes people ignore the dangers of hand tools? Is it because the tools are not powered, and are, therefore, considered safe in any condition? Is it that we just take the safety of hand tools for granted? We shouldn’t. The Consumer Products Safety Commission says that more than 100,000 injuries requiring hospital treatment due to misuse of common hand tools occur each year.
Stop and think: When was the last time you checked the condition of the hand tools at your workplace? Do your employees regularly turn in defective hand tools for replacement? Do they know what defects to look for?
Rule of thumb
The Hand Tools Institute, an association of hand tool manufacturers and suppliers, says that most hand tool accidents are preventable, if workers just follow basic safety rules. The five main points to remember are:
1) Always use appropriate eye protection to keep flying pieces and parts from injuring your eyes. The Hand Tools Institute suggests keeping your safety goggles in your toolbox for easy access. In addition, consider wearing work gloves to gain a better grip of the tools you work with.
2) Use the right tools for the job. The Institute warns that each tool is designed to perform a specific function. It is dangerous to substitute or use an inappropriate tool.
3) Use tools properly, including proper positioning to avoid musculoskeletal disorders (MSD).
4) Service tools regularly. Follow the manufacturer's recommendations for performing proper maintenance on your tools.
5) Don't use damaged tools. Discard them immediately, fix them or replace them.
Handy tips
Just how do these rules apply to your tools? Here are some examples:
Pliers: Too many people use pliers as wrenches for turning nuts or bolts, which is not their proper function. Actually, they should only be used for cutting wire. Discard your pliers when they have chipped or dulled cutting edges.
Hammers: A hammer blow should be struck squarely and parallel to the surface. Glancing blows can cause injury. Never use a hammer with a loose or damaged head or handle. Look for dents, chips, cracks or other signs of wear and tear. Use riveting hammers for sheet steel, carpenter or claw hammers for driving and pulling nails, and ball-peen hammers for metal work.
Screwdrivers: Never use a screwdriver as a punch, wedge, pinch bar, pry or chisel. Choose the proper size tip for the screw. The wrong size driver can cause a chewed-up screw head, damaged screwdriver and a bloody knuckle.
Wrenches: Don't try to extend the handle of a wrench with a cheater bar to add leverage. Instead, use a wrench with the proper sized handle. Make sure the wrench fits the nut, or it could slip or break. If possible, pull the wrench instead of pushing it. The safest wrench is a box or socket type.
Cutting-edge tools: Dull cutting-edge tools are dangerous, as they require excessive pressure to make them cut. Keep tools sharp. Always cut away from the body.
Safe handling
Make sure your employees are cautious when handling all tools. Workers shouldn’t leave tools lying around where they can be a tripping hazard or where they can fall and injure workers below. Warn all employees not to carry chisels, screwdrivers and other pointy tools in their pockets. They should use a carrying belt with the tools’ pointed end down. Tools should be handed from one worker to another, never thrown. Pass pointed tools with handles first.
Avoid musculoskeletal disorders
Using hand tools, such as screwdrivers, over and over again can cause MSDs, such as Carpal Tunnel Syndrome. Your employees can minimize such injuries by keeping their wrists straight and elbows close to the body. Comfort grips or properly fitted gloves can help reduce the stress on hands and wrists. Employees should also take frequent breaks to rest their muscles. Another excellent way of preventing MSDs is to consider tool design when making purchases. OSHA recommends the following:
- Look for lightweight tools with handles that allow a relaxed grip and that keep wrists straight.
- Tools should be designed for use with either hand and come in various sizes for different-sized hands.
- Tool handles should be shaped so that they contact the largest possible surface of the hand and fingers. Avoid handles with sharp edges and corners.
- Use power tools whenever possible to reduce repetitive movements.
- The weight of the tool should be counterbalanced to make it easier to use and reduce vibration.
Point in the right direction
Of course, the best way to prevent hand tool injuries among employees is to provide training. After reviewing the safety practices discussed previously, try some of these training ideas:
Give the workers a written quiz that requires them to identify the appropriate tools for various job tasks at your worksite.
Bring in damaged tools and have your employees find the defects.
Ask your employees about any problems with the design of their hand tools.
Conduct a contest for best-kept tools and give the winner a prize.
Encourage your employees to report problems with hand tools and to work safely.
Stop them before they use the wrong tool for a job.
Show them how to use the tools safely.
Finally, when they do everything right, give them “two thumbs up!”
About the author:
This article provided by TrainingOnline.com, an e-learning division of Business and Legal Reports Inc. and a publisher of quality compliance, training and productivity tools for the workplace. For more information on the company’s range of products and services, visit www.TrainingOnline.com.
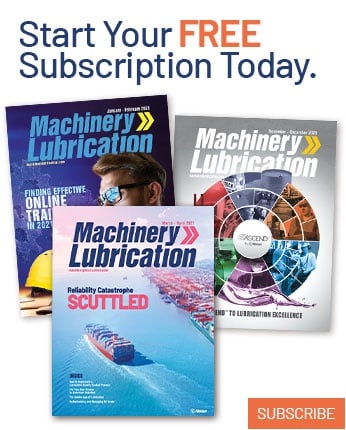