Dear Energy Expert:
My plant is looking for ways to reduce our energy intensity and better manage our energy usage. Can you provide examples of what your company has done to get closer to this goal?
Steve Schultz, the corporate energy manager at 3M and an Energy Expert for the U.S. Department of Energy, provided the response to that question.
As a diversified technology company with operations in more than 65 countries and products sold in nearly 200 countries, 3M’s corporate leaders quickly realized energy management was essential to not only remain competitive worldwide, but to also increase energy efficiency and reduce energy-intensity emissions. At 3M, energy management has quickly been infused into our corporate culture. We have committed to environmental initiatives and sustainability initiatives for several decades. In fact, 3M first established its Pollution Prevention Program (3P) in the 1970s to help prevent pollution at its source.
In an effort to reduce its environmental footprint, 3M devises a new set of corporate environmental goals every five years. The company’s 2005-2010 goals address environmental issues through eco-efficiency and pollution-prevention metrics. These are complemented by individual business unit goals that incorporate product life cycle management within the unit’s strategic plan. Individual plants are tracked on a quarterly basis, and progress toward the corporate energy-reduction goals is evaluated annually. The measurements use targets for percentage reduction in energy use per pound of product produced and the percentage reduction in energy/net sales for a particular time period. Since the inception of 3M’s energy-management program in 1973, British thermal units (Btu) per dollar of net sales have dropped significantly. Realizing energy efficiency can also provide a competitive advantage. 3M’s Corporate Energy Management Team has established a model to provide global leadership by controlling energy costs, improving operation efficiencies, reducing environmental impacts, ensuring availability of reliable energy supplies and implementing a strategic energy-management plan.
Figure 1. Sample 3M Plant Energy Dashboard
In order to meet these goals, an assigned Corporate Energy Management Team annually develops a strategic energy management plan. The team outlines annual energy strategy and prioritizes tactics, setting oversight and guidance for division- and plant-level planning processes and integration into the corporate strategic planning process. For 3M to effectively implement these projects and help identify near- and long-term savings opportunities, five main tools are incorporated: strategic road maps of action; gaps in maps; business and country energy plans; facility energy teams; and facility energy assessments. Following the above plan using the tools for implementation and facility energy assessments has led to the success of several energy-reduction projects. More than 185 projects were completed in 2006, delivering $18.2 million in savings with energy use reduced by 2.9 percent from the previous year.
A key enabler in the implementation process is our Annual Energy Recognition Program, which was internally developed in 2003. We created this program to boost motivation and provide a sense of accomplishment, particularly when taking on challenges of this magnitude. Utilizing the 3M Energy Program Dashboard and EHS scorecards, we issue awards to teams following a four-level rating, ranging from bronze to platinum. We recognize all winning teams through various levels of value, ranging from certificates to dinners with management.
The 3M Energy Program Dashboard considers energy per pound of product, total energy use, cost of energy, world-class energy assessment score and value of energy projects implemented.
Results for each category are calculated on a quarterly basis. A goal for the next year is then determined and used to compare results. At the end of the year, each category’s percent change and value-add is compared to the previous year determining their status rank.
Tier I facilities (the company’s 59 largest energy users) are evaluated on the five criteria listed above. Based on a points system using the dashboard results, they are rewarded accordingly. Tier II locations are self-nominated, and the maximum award is gold level. In 2009, three 3M U.S. plants and six international locations earned the platinum award; 10 other facilities were classified as gold award winners. Regardless of the award level achieved by our facilities, we strongly support and continue to encourage yearly improvement, providing plant energy teams certificates for strides made throughout the year.
Recently, 3M successfully partnered with the U.S. Department of Energy Industrial Technologies Program’s Save Energy Now LEADER initiative, which will assist with 200 additional energy savings assessments of the most energy-extensive 3M plants in the United States. The LEADER program paves the way for 3M to work with diverse partners to create awareness and find energy-saving solutions. Through this campaign, 3M will disseminate energy savings information and tools to more than 200 plants to help reduce natural gas and electricity use. A few of the 3M plants participating include Brownwood, Texas; Nevada, Mo.; Decatur, Ala.; Guin, Ala.; and Austin Center, Texas.
Figure 2.
Having previous partnerships with the Department of Energy, our access to outreach activities has been extended, the number of external resources available has increased, and the benefit of leading by example to reduce energy intensity and carbon emissions while enhancing competitiveness is invaluable.
Investing in Cost-Effective Renewable Energy
Leveraging resources with our partners and continuing our commitment to energy efficiency allows further exploration and investment in cost-effective renewable energy. A 2,000-square-foot solar wall on the south side of the warehouse at 3M’s Perth, Canada, plant has contributed in displacing 329 million Btu of electricity for the site each year and preheats the air, reducing the building transmission loss. 3M is also exploring opportunities to utilize landfill gas, on-site and off-site wind energy, and biodiesel at other 3M locations.
3M has been successful in reducing its energy use and is on track to exceed the present 20 percent efficiency improvement target. 3M has been recognized for its program by being awarded the Energy Star Sustained Excellence Award for Energy Management again in 2010, the company’s sixth time and an industrial record.
This article was written for the U.S. Department of Energy’s Industrial Technologies Program and appeared in the DOE’s Energy Matters newsletter. For more information, visit http://www1.eere.energy.gov/industry/. Ask the Energy Expert is an ongoing column with the intent of providing information and solutions for industry’s most pressing questions.
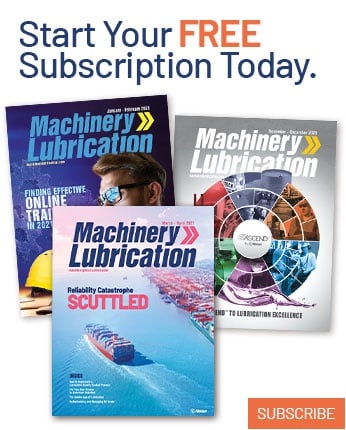