Eliminating process waste is essential to reducing operating costs. There are many ways to train employees about operational wastes and how to recognize them out on the shop floor. Training for waste elimination can be a fun exercise that employees from all levels of the organization can use in their everyday lives, making the workplace a little more effective each day.
Removing operational waste requires a group of employees working together who fully understand the different types of waste and what to do about them when uncovered. When there is discussion about removing waste, it is common for employees from all levels to be suspicious about the possible changes and how they will affect daily activities. Educating as many people as possible about eliminating operational waste reduces these concerns. Some jobs will be different; some materials may be delivered differently; or there could be a change to the physical layout of the machines.
Without knowing the waste that is in the current process, no one can accurately predict where the changes will occur. There could be many changes to an operation just to eliminate a costly waste that has been identified as eroding profits or some other significant contribution.
Without doing the waste analysis of the current procedures, no one can tell what changes will make strategic sense. For example, consider two pieces of equipment that are dependent on one another to produce a product. They are determined to be out of synchronization, and one produces at a rate of 2:1 compared to the other. If this has been determined to be a product that will be run at a high enough volume in the future, then the time and effort to make changes to the process and operations is warranted. If this is a one-time run or a product that is sold infrequently, solving this equipment issue may not be high on the priority list. Each example of waste that has been identified will have to be compared with other ideas to prioritize the smartest changes.
These are typical categories of operational waste that will reduce profits and erode productivity:
- Overproduction
- Delay
- Transport
- Processing
- Inventory
- Intellect
- Wasted Motion
- Making Defects
Training employees to identify the waste and understand the root cause is essential before making improvements. In just a few hours of training, employees can capture the basics of each type of waste and begin generating ideas on how to reduce or eliminate each one.
A great way to teach the subject in a fun format with high retention is by playing a game. Simulating an assembly process will bring the textbook information to life. Even if your business is not an assembly site, the lessons are transferable.
The Waste Identification Game is designed to be simple but effective. It can be played in two or three rounds with smarter and smarter processes each round.
The game should be run a minimum of two times for five minutes each. The first run is loaded with wastes in a typical layout. After the first run, have a discussion about the different wastes that were observed. Redesign the activities to optimize the process first and the individual operations second. Run the game a second time and see the difference in quality, production volume and organizational cost per unit.
Scenario 1.
For the first run, use plain cups as the raw material being converted into finished goods. Set up a six-man work cell all lined up on an 18-foot-long table. Establish a series of marks on the cups to be done per station as they go down the assembly process. In the first scenario, set up uneven assignments, build up unnecessary stock, make the last guy deliver the finished goods away from the work area, provide more raw cups than they need for the order, provide fine-line markers to make thick markings, provide vague quality standards, make each person reach for their incoming pieces from their in-box, and allow some cups into the first position with quality defects. Measure the time per station and the total volume produced. Also, count the rejects or defects.
Supplies include: Large paper cups, large and small tipped markers (10 green, 10 black), 12-inch round paper mats (to use as an inventory holding area on each person’s table in the first round), five stopwatches, notepads and writing pens, five tables (three to get started with assembly and two for inventory stocks), stencils, six chairs, dry erase board (optional).
Scenario 2.
The second round of the game should be established after the process and operations have been optimized. For processing improvements, set up clear directions per station, set up inspections per station (quality control), eliminate in-boxes for work-in-process storage, and reduce the transportation to finished goods. Shrink the overall footprint of space being used. For operational improvements, assign evenly timed tasks per station, provide stencils for the markings, and assure the markers are the best tool for the job. Teach each operator how to spot quality issues at the source. As the process is running, measure the time per station again and total volume produced while counting defects.
Takt time from the customer demand should be part of the formula for success. Even though this is a simulated exercise, impose a drastic swing in demand and tell everyone that they only need to make 400 cups by the end of the day and see what recommendations they have to adjust the operation. Observe the estimated cost per unit.
Don’t be afraid to stop your factory line and discuss what you are seeing. A third round could easily be adopted by taking the improvements even further. The time spent playing a few scenarios will be time well spent. Switch the observers taking notes with those people conducting the process each round to keep all perspectives engaged.
From classroom to operations
Time and time again, when these lessons about flow and waste removal are presented to companies and supported by leadership, incredible ideas begin to surface. Company after company finds thousands of dollars in real savings while improving quality in the product or service and improving relations with the employees. For example, in a beef packing plant, workers typically boxed up finished cuts of meat, tossed in some dry ice and double-banded the heavy-gauge boxes as a finishing step before palletizing and sending it to the cooler or truck.
Discussions with the customer uncovered that they have to throw dry ice away to determine the real weight of the meat. This has been a variable in their side of the business for years. After careful review, it was determined that the meat company often put too much dry ice in the boxes and caused the variation in box weights. Also, due to the superior box strength, it was determined that the customer would prefer to only remove one band, not two, from each box, creating less work and less trash. Making those two changes made the customer happy, increased quality and saved the beef packaging facility $150,000 per year in purchased materials. They replaced the shovel that used to scoop the dry ice to a hand-held scoop, standardized the amount going in to each box, and used one strap vs. two from then on.
At another company, a precooked meat plant, the grease/water run-off had always been treated as waste, and the site had a long-term agreement with the local waste treatment facility to accommodate the waste product. After careful review of the entire operation, it was discovered that the run-off could be sold as an animal food additive. Between the sales dollars from the customer and the savings with the local water treatment, the site recovered more than $900,000 a year. The environmental impact was also significant.
At a third site, where they assembled and packaged small aftermarket car parts, one area of the business had always struggled with quality, production volume and employee retention. An operational waste analysis revealed that the employees were often missing one or two assembly components that they needed to start building their piece. This forced the employee to find a supervisor who would have to search around for the final component to get started. Also, the employees were typically not experienced in the specific part due to the large variety of assemblies with which they worked. To solve both problems, supervisors were asked to build the first piece in front of the employee that would be working at that station. This assured all the assembly components were there; and, one finished example of what was supposed to be built was right there. These changes improved quality (28 percent reduction in defects) and improved throughput by 45 percent, resulting in $470,000 of additional product built correctly the first time with the same employees and capital investment.
At a pharmaceutical business, the waste assessment discovered unusual amounts of waiting by the operators. A root cause analysis revealed that the drying process had an unusually high variance in its ability to get the medicine in and out of the dryers in a timely manner. A chart was developed that showed the planned use of the dryer per the production plan in black and the actual usage in green. If the lot ran over and was not pulled out on time, it was marked in red.
The lots run for multiple days and it was easy to forget when a product needed to be switched. By instituting this level of information into the daily decision making, this area of the business no longer restricted production, and the new open capacity allowed for one dryer to be regularly available for maintenance. The additional throughput resulting from the shorter cycle time of the product was impressive.
All of these stories represent employees working with their new knowledge of operational waste and seeking smarter ways to get the job done. Continuous improvement is within the reach of any organization. Training and mentoring employees in an operational waste reduction program is a great way to get started.
Conclusion
Training associates at all levels on how to identify and eliminate waste is smart business. Spread the word and see what positive ideas surface for your business. It’s up to management to spearhead continuous improvement until it is part of everyday life. The upfront investment in training will pay for itself many times over.
About the author:
Joe Mikes, CMRP, is a senior consultant for Life Cycle Engineering (LCE). Joe has been training companies to improve their overall performance since 1996. He specializes in generating and sustaining continuous improvement programs for both service and product-based organizations. You can reach Joe at jmikes@LCE.com. For more information about Life Cycle Engineering, visit www.LCE.com.
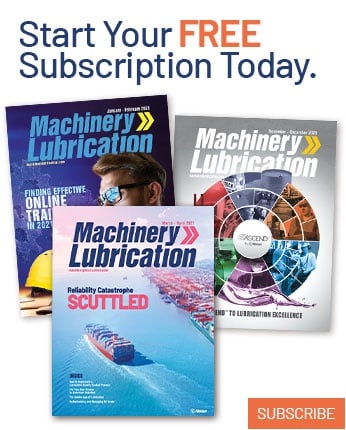