Recently, I volunteered to go to the gemba as an inspector on the weld assembly line for a metal casket manufacturer. After some training, I was left on my own to inspect the welded casket shell for the rest of the shift. It did not take long to find problems in the process.
One non-conformance that caught my attention was a scratch in the same spot on nearly 50 percent of the metal units. Following the established standard work method, I sanded out the scratch and pushed the unit on to the paint department.
The next day, I met with the regular inspector and shared what I observed. He confirmed that this scratch was a pretty common occurrence. Since it was an easy five-second fix, nobody paid much attention to it. Does this sound familiar?
The elimination of this scratch became my new quality mission. I knew I could locate the root cause because it was consistent and easy to see.
To track down the scratch's root cause, I decided to use the 50/50 approach. The technique is pretty simple to use. By dividing the process in half (50/50) between the starting point and the end point, you check to see if the defect appears at the process midpoint.
Depending on whether or not you find the defect at the midpoint, you divide the process in half again, moving either upstream or downstream. By repeating these steps, dividing the process in half each time, you continue looking for the defect until you narrow down the possibilities and discover the source.
Because I knew the scratch could be found at inspection at the end of the assembly line, I went to the front of the line and checked for evidence of the scratch. Finding no scratch on the metal coming into the process, I split the distance between the inspection station and the front of the line. It was there that I found the scratch.
My next move was to split the distance again, between the start and the middle of the line. I found the scratch again. I continued splitting the line and moving upstream or downstream, depending on what I found. After a few rounds, I found the origin of the scratch at a single station.
At this station, I saw what caused the scratch. Ironically, it was the quality check method at this station that caused it. The welder used a metal square to see if the metal casket shell was square. The metal-to-metal contact between the square and the casket created the scratch.
Now that the root cause of the scratch was known, a countermeasure was needed. A simple, homemade plastic cover on the square prevented the metal-to-metal contact. The scratch problem was eliminated.
By using the 50/50 approach, it's easy to zero in on the root cause of a problem, as I did in the metal casket scratch case. Give it a try on your next root-cause quality quest.
About the author
Mike Wroblewski started his lean journey with instruction in quick die change from Shigeo Shingo. Mike is president of Victory Alliance Technologies, a Greensburg, Ind., firm that specializes in lean implementation. Mike can be reached by e-mail at mwroblewski@victory-alliance.com.
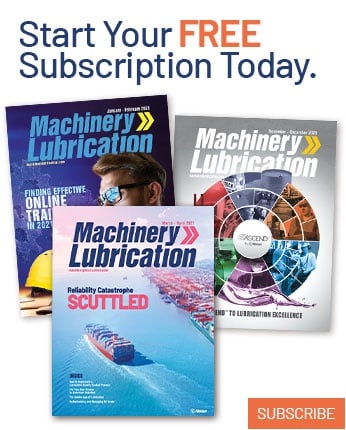