A breakthrough in robot MIG welding that will increase welding speed and, consequently, boost productivity in the metal fabrication sector is the latest investment project for
Robot welding was introduced to manufacturing production lines a number of years ago to improve welding speed and consistency. Greatest interest and uptake occurred in the automotive industry – both vehicle manufacturing/assembly plants and sub-component supplier production lines.
Robot MIG (Metal Inert Gas) or Gas Metal Arc Welding is now widely used across metal fabrication but it requires a significant amount of electricity and uses carbon dioxide (CO2) as a shielding gas. Both contribute to greenhouse gas emissions, which was the catalyst for CEGT’s interest in the technology.
CEGT is to invest $450,000, alongside another strategic investor, into MIGfast Pty Ltd., the company formed to commercialize the new technology. CEGT is a private company established as an initiative of the Victorian Government to invest in the development and demonstration of new sustainable energy and greenhouse gas reduction technologies.
The MIGfast product is a consumable welding contact tip that provides significant benefits in welding productivity, weld quality and fume reduction. It has been developed by the CSIRO and the CRC for Welded Structures.
Jan Dekker, managing director of CEGT, said that MIGfast could reduce the time to make a weld by up to 50 percent, resulting in the use of less energy per weld.
“This means that energy consumption is reduced as is the use of CO2 shielding gas, which are both highly positive outcomes in terms of energy use and greenhouse gas emissions,” Dekker said. “While welding performance improvement is still sought by industry, there have been no substantial advances made in recent times. There have been refinements in robot programming and movement optimization, however most production speed and efficiency benefits of robot welding have been realized. Prior to the development of the advanced energy efficient welding tip, the most recent technological advance was pulsed MIG welding, which is now used in many automotive manufacturing and assembly plant but requires significant capital investment.”
The MIGfast technology allows more efficient welding for such MIG welding applications without the need for capital investment.
The patented MIGfast welding tip has been designed to be interchangeable with existing welding tips to allow simple and cost-effective take-up of the new technology. It allows more efficient welding for both pulsed and non-pulsed MIG welding processes.
Other advantages include reduced weld fumes and spatter, resulting in a cleaner and safer work area and significantly reduced heat distortion in welded parts as half the energy is injected into the weld for the same result.
Trials have been conducted with the MIGfast tip on production lines at two major Australian manufacturing plants. They have shown a substantial reduction in welding time and significant overall production speed improvements. The trials also confirmed that the weld characteristics met the required standard.
Investment funds will be directed to finalizing the technical development, further industry trials and commercialization. In terms of market opportunity, the MIGfast welding tip is a consumable item that needs to be replaced after approximately eight hours of welding (one manufacturing shift).
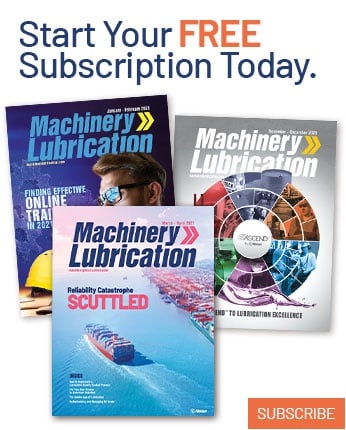