A Grand Rapids, Mich., company has installed a massive milling machine that can cut the entire fuselage of a fighter jet within a hair's width of tolerance, the largest machine of its type in the world.
Paragon D&E has installed the largest double gantry 5-axis FIDIA milling machine about the size and length of a car wash that can easily cut the entire fuselage of an F-22 Raptor fighter jet within a hair's width of tolerance.
"Our new FIDIA milling machine represents a significant leap forward for Paragon D&E as we supply industries that demand highly precise molds and machined parts that are also very large," said David Muir, president of the Grand Rapids-based company that serves the aerospace, alternative energy, automotive, heavy truck, nuclear and other industries.
In addition to cutting large three-dimensional shapes from aluminum, steel, composite, or other materials, the FIDIA can be fitted with sensors so that it can precisely measure the shape of very large objects – allowing Paragon D&E to help customers reverse engineer existing parts such as helicopter cockpits and airplane tail structures to produce replacements.
Purchased and installed a cost of $3.5 million, the double gantry 5-axis milling machine has a table 60 feet by 12 feet with virtually unlimited weight capacity. As a five-axis machine, the FIDIA precisely controls the position of cutters as they move along the length, width, and depth of the material, but also as the machining head is rotated along two additional axis. The machine was built by FIDIA S.p.A., San Mauro Torinese, Italy.
"The capabilities of the FIDIA will allow us to fabricate very large parts and molds with very sophisticated shapes," said Muir. "This is particularly important in the aerospace, automotive and any other industries that require curved surfaces to accommodate the aerodynamics of their products." He said that same manufacturing capability has direct application to make components for heavy-duty machinery used in alternative energy, mining, agriculture, large-scale metal casting, and marine industries.
Paragon D&E has spent much of the winter preparing a foundation for the machine at its plant at 5225 33rd St. SE. The company had to first dig a rectangular trench 75 feet long, 30 feet wide and 8 feet deep, which was then filled with a mixture developed by Michigan State University of concrete and small metal fibers to give extra rigidity as the base for the machine tool, allowing for its remarkable tolerance of only .0015 inch over a 60-foot distance. The thickness of the finest human hair is about .0015 inch.
But the cost of site preparation and the FIDIA is only part of the investment that Paragon D&E has made in the new technology, Muir said. "We've also made a significant investment in our Paragon team members. We have a very deep pool of machining knowledge here, so we are really leveraging the team approach to projects. That team approach is making a huge difference with our customers."
Since the company was purchased in 1962 by Muir's grandfather, Fred M. Keller, Paragon D&E has established a strong reputation as a full-service mold supplier with engineering and build capability that has consistently invested in new technology. With annual sales of approximately $30 million, Paragon D&E employs about 140 skilled toolmakers, machinists and support staff in Grand Rapids. The trade publication Plastics News ranked Paragon D&E as one of the top 20 mold makers in North America in terms of sales in 2007.
"In a very real sense, the investment in equipment like the FIDIA and the organizational changes we have made over the past few years are really going back to the Paragon's roots as a leader of cutting edge technology," he said. "My grandfather was known in this industry as an innovator, and the Paragon team has taken this to the next level."
Paragon D&E can successfully complete complex jobs with tight deadlines, Muir said. For instance, one advantage of the FIDIA is that it can operate both gantry heads simultaneously using the same program, which means it can precisely position two milling heads to cut on the same job. That capability makes it possible for the FIDIA to machine both sides of an aircraft fuselage at the same time or for one cutter to perform rough milling, followed immediately by a second cutter that performs finish milling. The result: some jobs can be performed in half the time it takes other companies.
"We do have some projects now for the U.S. Defense Department that are slated for this machine," Muir said. In addition to being AS9100 certified for the manufacture of aerospace components, Paragon D&E is ISO certified and also registered under International Traffic in Arms Regulations (ITAR) as a secured facility for defense component manufacturing.
As part of its program to break into new markets, the company is seeking NQA-1 qualification so that it will be able to work on materials and components used by the nuclear power industry.
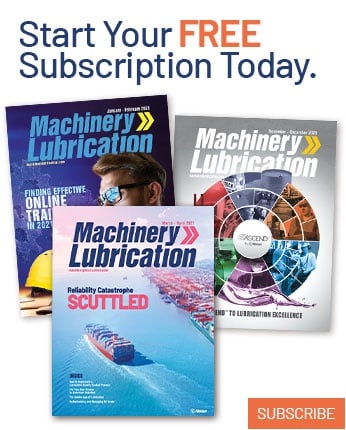