I remember back in my Navy days having a boss who managed under the mantra, “If you aren’t measuring it, you aren’t managing it.” We had metrics for everything, and we briefed them on a regular basis.
I remember countless long hours trying to figure out how to explain and justify the metrics in the “red.” I could just see my fitness report and career going down the drain every time the big red meatball was thrown up on the conference room wall – usually followed by a comment from the boss along the lines of “What’s the problem, lieutenant? You need to get this problem fixed.”
In the traditional world of management, we are enamored with our red, yellow, green metric charts, leading to the ever-present “self-preservation” paranoia about going forward to management “red.” Red is bad, green is good. Knowing that, managers lobby heavily for easily achievable goals so they don’t have to explain why they have “failed.”
In the world of lean management, the mind-set is completely reversed. When the big red meatball goes up, the response from the floor is normally: “Great! Thank you for bringing this to our attention. What can we do to fix the problem?” In lean management, problems are viewed as opportunities – not failures. Lean managers view problems as gold to be mined, and they ruthlessly go after the problem, not the people. They view a “green” board as being worthless – if you are green, where do they focus improvement efforts?
I once took a course from Pascal Dennis who worked for and with Katsuaki Watanabe (now president of Toyota) and other lean masters from North America and Japan at Toyota Motor Manufacturing Canada. He recalled a story of Mr. Watanabe walking into a plant for a visit. The local managers were very excited and proud to show him their metrics – as they were all green. They were devastated by his response: “Ah, no problems; must need no managers ...” His point obviously was that if they are operating in a comfort zone with metrics that aren’t driving them to attack waste, then they aren’t doing their job. What you really want are employees falling over each other to bring problems to the table.
In a lean environment, all efforts are focused on removing waste from the work environment through continuous process improvement. All lean metrics and their concomitant targets should be focused on that waste removal. The waste is the gold.
In the lean world, employees should understand and be able to translate corporate lean strategic goals in the context of the work they do on the floor. They should know that they will be heralded for coming forward with a problem or roadblock that, if removed, will make the organization more efficient.
Management must empower them to fix problems where they can, and go to bat for them in removing obstacles they can’t fix themselves. Many in the traditional world relate this to a “suggestion” program. If it takes a formal program to bring ideas to light, you aren’t a lean organization. Every employee must have the innate desire to attack waste, and a clear path to the person or mechanism that can help them fix it. They must know and accept that tangible and intangible benefits will be returned to the organization – benefits that may or may not directly affect them. I’m not suggesting that employees should not be rewarded for helping break through a waste barrier. I am arguing that employees want to do it for the betterment of the organization, because they have the true sense that in the long run they will benefit. They know that their efforts will help ensure the organization’s long-term viability, thus returning to them the assurance that their jobs are secure well into the future.
So the next time you see a red metric, shout hallelujah, praise the bearer of “good” news, and start digging into the problem to find the waste holding your organization back. And the next green metric you see … send them back to the drawing board.
About the author:
Russell Rhea represents the U.S. Air Force’s OC-ALC Transformation Office in Oklahoma City. This article was first published in the Tinker Takeoff, the newspaper of the Oklahoma City Air Logistics Center.
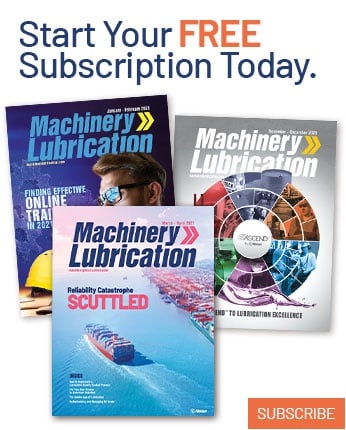