Dangerous debris near rocket launches could be tracked in real time by combining tricks from particle colliders, moon landings and vulture tracking, a new study finds.
In a paper to be published in Acta Astronautica, physicist Philip Metzger of NASA’s Kennedy Space Center and colleagues describe a technique to plot the paths and determine the densities of worrisome detritus kicked up during launch. This method could help flight engineers know instantly which pieces of debris threaten the spacecraft.
“We combined together two different types of software that can do on-site analysis,” Metzger said. “In the future we can take video of the launch environment, and the software can automatically … conclude what were the sources and the makeup of the debris.” The paper was published online at arXiv.org on October 22.
“For manned missions, this is very important. I’m surprised it’s not been done yet,” said Nilton Renno of the University of Michigan, who studies how rocket plumes from Mars landers affect the Martian surface. “It will improve our confidence in the assessment of potential damage, not just for the space shuttle but for any other future spacecraft.”
In 2003, the Space Shuttle Columbia was damaged by a dislodged piece of insulation. The damage caused the shuttle to break apart upon re-entry, killing all seven astronauts on board. The event showed how crucial it is to catch debris damage early.
The need for better tracking systems during launch was highlighted during the Space Shuttle Discovery launch in May 2008, when several thousand bricks blew out the end of the flame trench under the shuttle. Simultaneously, a mysterious piece of debris flew high into the air near the shuttle, apparently from the flame trench. Had the mystery object been a brick, it could have damaged the shuttle and put the crew at risk.
To identify the object, Metzger and colleagues took advantage of NASA’s bird watching system. In 2005, during the first launch after the Space Shuttle Columbia disaster, a shuttle was threatened by another flying menace: a vulture that smacked into the external tank during takeoff.
Since then, engineers have tracked vultures as a routine part of launch by taking pictures of the launch area from two different angles. Combining the pictures gives a three-dimensional view of the region, so moving objects like birds and bricks can be found and followed. Metzger and colleagues have used similar measures to model how a rocket plume could scatter dust and boulders in the low-gravity environment of the moon, threatening nearby lunar outposts.
For the May 2008 Discovery launch, Metzger’s team used images from the vulture-tracking system to plot the mystery object’s trajectory, then did some simple ballistics analysis to figure out the object’s density. Neither technique is complicated or new, but the combination of images and ballistics had never been used for launch analyses before.
“We’re not the first people to study this by a long shot,” Metzger said. “All we’ve done is developed a new technique that seems to be very useful and very fast.”
The object was too light to be a brick, but it was the same density as a piece of foam from a solid rocket booster. “At no point was the orbiter in any danger” from the foam, said Bob Carilli, a co-author of the study and engineer with NASA contractor United Space Alliance.
Now that they’ve shown that the method works, Metzger and colleagues hope to speed the system up with tricks from particle colliders. Particle colliders automatically flag collisions that look interesting and store data for further inspection. NASA could use similar techniques to target only the potentially dangerous launch debris.
“The objective is not to study the individual particles that result from the collision, but rather to burrow down into the originating event,” Metzger said. “That’s our ultimate objective, too.”
The system will be used on the next launch. “We’re using it right away. We’ll use it routinely from now on, whenever we analyze debris,” Metzger said. “Now that the software’s been written and debugged, it only takes a couple hours to do the whole process, which is a big improvement.”
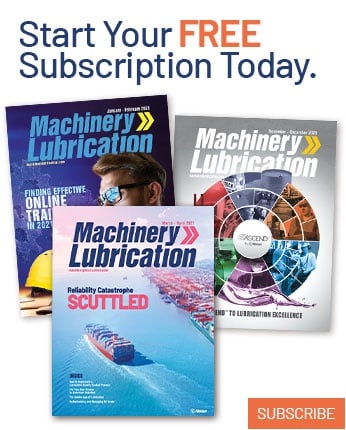