A drop of liquid. A pinch of sand. A small scrap of cardboard. That’s all it takes to create the potential for slips, trips and falls. According to the United States Department of Labor’s Bureau of Labor Statistics, more than 602,000 workers were injured by slips, trips and falls to the same level in 2004, and averaged seven to nine lost work days as a result of the incident.
Keeping floors clean and dry is a key factor in preventing these injuries, but that often can be a daunting task. Even the Occupational Safety and Health Administration (OSHA) acknowledges that it isn’t always possible to keep a floor clean and dry. Standard 29 CFR 1910.22(a) states, “The floor of every workroom shall be maintained in a clean and, so far as possible, a dry condition. Where wet processes are used, drainage shall be maintained, and false floors, platforms, mats or other dry standing places should be provided where practicable.”
To help quantify what a clean, dry floor is, the American National Standards Institute (ANSI) and the American Society of Safety Engineers (ASSE) jointly published ANSI/ASSE A1264.2-2001, “Standard for the Provision of Slip Resistance on Walking/Working Surfaces.”
Although this standard is a great reference and provides important details on topics such as coefficient of friction and how to choose the correct slip meter, there are three steps that any facility can do to help increase floor safety – without incorporating high-tech gadgets.
Absorbent socks serve as a barrier to
prevent the spread of spilled liquids.
STEP ONE: CLEAN UP
Just because the floor always has been covered with oil or a workstation always has been messy doesn’t mean that it needs to stay that way. Tulips don’t need to be in bloom to do a little spring housecleaning. Routine facility shutdowns, for example, are a great time to give facilities a thorough cleaning.
In addition to thoroughly cleaning the floors, consider enhancing traction with floor preparations such as etching, scoring, grooving, brushing, appliqués, and non-slip paints or adhesive non-slip strips to help increase safety in wet or slippery areas. After application, be sure to use the proper cleaner to keep those floors at their best.
Placing mats or floor runners at building entrances also will help cut down on both water and dirt being tracked into a facility and enhance safety.
Designating convenient storage areas for all parts and tools also can help keep items out of walkways and help minimize tripping hazards. Securing long power cords or rewiring areas so that long cords are no longer necessary are two other steps that can be taken to help minimize tripping hazards.
Mats absorb overspray that causes walking
surfaces to be slippery.
STEP TWO: LACE UP
Steel toes and metatarsal guards are almost an industry standard in footwear. These features help protect the foot against crushing and puncture wounds. Just as important are the construction and tread pattern of the sole. In wet areas, lugged soles will help increase traction. For oily areas, consider lugged soles made of polymers that are resistant to oil, such as nitrile or butyl.
Smooth soles, commonly found on men’s and women’s dress shoes, are usually not a good choice in an industrial setting. Even if the floor is clean and dry, smooth soles can be very slippery on sealed concrete, linoleum, tile and other smooth, finished surfaces.
For some facilities, adopting a “no smooth-soled shoes” policy for office workers or visitors who enter production areas can help ensure their safety. Posting signs or notices on office doors or at work area entrances also can remind office workers of this potential hazard.
STEP THREE: STOCK UP
Sometimes, adding non-slip coatings to floors isn’t possible or practical. For instance, in some areas, a textured floor may not be desirable because it’s harder to keep clean. In older facilities where oil has saturated the floor, it may be impossible to get a non-slip coating to stick.
Absorbent mats can be used for routine maintenance to make walkways cleaner and safer by absorbing overspray or other liquids that cause walking surfaces to be slippery. Mats also are appropriate in fluid dispensing areas, waste collection stations, around water fountains, coffee areas, sinks and other areas where spills are common.
Absorbent socks are a good fit around the bases of leaky machinery or to surround a puddle of liquid. They also are appropriate for window ledges or areas where leaks penetrate seams, such as building foundations.
Stanchions, signs, warning tape or other forms of barricades also can help workers identify slip hazards, especially when these tools are readily available in spill-prone areas.
Stocking adequate supplies in slip-prone areas and having a dedicated maintenance staff isn’t enough. Training is essential to making sure everyone knows their part in maintaining facility cleanliness.
This training often can be incorporated into corporate HAZCOM (29 CFR 1910.1200) or spill response (29 CFR 1910.120) trainings, and is a great lesson for all employees, not just maintenance or line workers. A coffee spill on the tiled floor in the executive offices can cause an accident just as serious as slipping on an oily floor near a drill press.
CONCLUSION
Taking the time to improve floor conditions now, and training workers to identify and remedy hazards in their work areas, will go a long way toward a reduction in slip and fall injuries. This will save your company money by reducing worker’s compensation costs, and keeping workers healthy and on the job.
Karen D. Hamel is a technical specialist for New Pig Corporation. She is a graduate of the University of Pittsburgh and has nearly 10 years of experience helping customers find solutions to their environmental, health and safety issues. For more information, call 800-HOT-HOGS, visit www.newpig.com or e-mail karensp@newpig.com.
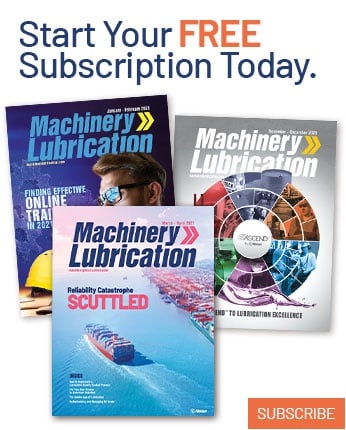