Ethylene oxide exposure levels and monitoring requirements are addressed in the Occupational Safety and Health Administration’s (OSHA) recently published Small Business Guide for Ethylene Oxide. The guidance document helps employers understand the ethylene oxide (EtO) standard and explains how to monitor the air quality in workplaces where EtO is processed, used or handled.
The document includes clarification of the various types of EtO exposure monitoring, lists and explains the exposure levels used by OSHA and provides an outline of what employers should do when monitoring shows EtO exposure levels exceed the allowable limits.
“Because ethylene oxide cannot be detected by sight or smell, workers can be exposed to dangerous levels and not realize it,” said acting Assistant Secretary of Labor for OSHA Jordan Barab. “Understanding OSHA’s EtO standard is vital to ensuring that employers know how to measure exposure levels so that workers are not exposed to potentially serious illnesses.”
The odorless, colorless EtO gas is widely used in hospitals to sterilize surgical equipment. Among other common products, EtO also is found in antifreeze, detergents, adhesives and spices. Short-term exposure to EtO can cause difficulty breathing and nausea, among other symptoms. Long-term exposure can cause more severe conditions such as damage to the nervous system and cancer.
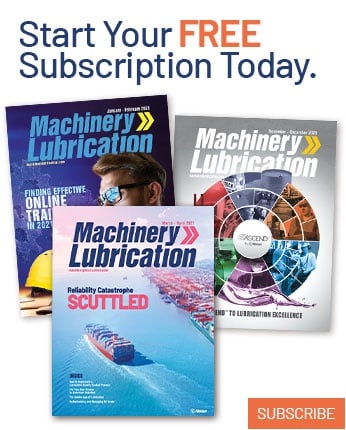