Toyota has succeeded in cutting material losses to 0.05 percent when producing synchromesh clutch hubs in gearboxes using Höganäs’ powder technology.
Toyota is synonymous with the lean production concept, and constantly endeavors to make all production processes as flexible as possible so Toyota always produces exactly what is needed, when it is needed. With fast and frequent realignments, minimizing material losses is even more important.
Toyota had already made a lot of progress in reducing these losses before it started collaborating with Höganäs.
Specifically, it wanted to improve the production of a synchromesh clutch hub in a gearbox. Toyota wanted the final product to have a better surface finish, to reduce post-processing as much as possible, thus cutting waste. This required components being pressed with less variation in final dimensions and with minimal weight differences between units.
Höganäs’ response to this challenge was an innovative approach to binding agents and processing powder during pressing. The concept was based on a new mixing concept, Starmix Boost, thanks to Höganäs’ leading-edge PM resources.
The new powder mix has resulted in a new synchromesh clutch hub that is extremely stable in terms of density and weight. Waste is reduced, and the otherwise frequent adjustment of press settings has been eliminated, saving time. Material losses have been reduced to a twentieth of traditional methods and materials. Thus a sharp reduction in post-processing operations has been achieved.
This collaboration has benefited both parties. Toyota has been able to take another step towards its vision of zero materials losses, while Höganäs has pushed the limits of powder metallurgy further.
Fact box:
Starmix Boost is a new zinc-free, press-ready bonded mix designed to tick all your metal powder performance criteria. Starmix Boost performs, especially when compacting more complex components and parts, such as synchronizer hubs, VVT parts and planetary carriers.
It has been customised for the production environment with productivity and ease of use in mind. The filling behavior enables faster pressing rates and a state-of-the-art lubrication system facilitates the forming and ejection of complex parts. With the exceptional component precision and consistency achieved, it is possible to reduce scatter (weight and height) by more than 50 percent, which can reduce machining, inspection and scrap costs.
Test results:
Component test results against comparable mixes show Starmix Boost to have a significantly better all-round performance across the main parameters of productivity, consistency, lubrication and scrap rates.
Consistency:
· Up to 50 percent reduction in Average Run-Out
· 25 to 50 percent reduction in Weight Scatter
· 25 to 50 percent reduction in Height Scatter
Productivity:
· 10 to 30 percent increase in productivity
Lubrication:
· 15 percent reduction in ejection force
Environment:
· 0 percent zinc
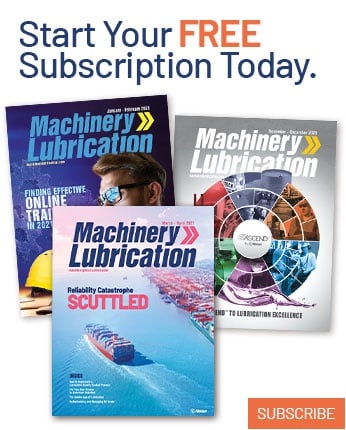