In the true spirit of environmental consciousness, GE Fanuc Intelligent Platforms’ customer Innovative Energy Systems (IES) has developed a clean energy solution that recovers methane gas from landfills and converts it into electricity as an alternative energy source. The solution uses GE Fanuc Intelligent Platforms’ controllers, HMI/SCADA software and operator interface equipment to facilitate the processing of the gas and keep the system running efficiently and effectively, providing Innovative Energy with a sustainable and competitive advantage.
IES, headquartered in New York State, has nine plants in New York and Vermont, producing more than 60 megawatts of capacity with more than 25 additional megawatts coming online over the next two years. In addition to its own facilities, the company also designs and constructs plants using this innovative system for other companies.
“With increasing global demand for more cost-effective, cleaner energy sources, OEMs and energy operators must uncover additional efficiencies to gain and sustain a competitive advantage,” said Maryrose Sylvester, president and CEO of GE Fanuc Intelligent Platforms. “The mix of products used by Innovative Energy Systems is a great example of how GE Fanuc solutions enable control and management of assets in a secure, scalable and integrated environment.”
IES utilizes GE Fanuc controllers on its proprietary gas collection and scrubber unit and other equipment used to collect and process the gas. GE Fanuc’s QuickPanel View and Proficy HMI/SCADA – CIMPLICITY monitor kilowatt-hours produced, display engine diagnostics, fuel flow and quality. This solution also provides an overview of the gas scrubbing system operation. IES plant managers use the system on a daily basis to monitor the engines and gas scrubbing system. This information allows the plant managers insight to complete preventative maintenance, which limits downtime events of the engines. Information includes: generator loading and unloading, alarm history, engine diagnostics including engine hours, oil temp and pressure, jacket water temp and pressure, fuel flow and quality, and exhaust port temperatures.
“We just cannot afford any downtime in our system,” said Peter H. Zeliff, president of IES. “Just one hour of the system not running could cost up to $20,000. Whatever electricity we generate has to get on the grid in order for us to make money as it is sold on the day ahead market. The GE Fanuc system has proved to be very reliable and have helped us to maintain an online availability of 98 percent or more.”
GE Fanuc controllers and I/O systems span the range of automation needs and are designed to meet the demand for versatile industrial solutions and are used in high speed packaging, material handling, complex motion control, water treatment, continuous emissions monitoring, mining, food processing, elevator control, and injection molding.
The QuickPanel View bundled visualization solution provides the tools IES required with a combination of bright touch screen displays, multiple communications options, and Proficy View – Machine Edition software. Acting as the bridge between the enterprise system and the plant floor, QuickPanel View is providing information, not just data, that the operators need to run the machines, and that management needs to run the business. The QuickPanel View is built on the Microsoft Windows CE operating system and features web server access to data and panels using any standard browser.
And, the client/server based visualization and control solution that actually helps visualize operations, perform supervisory automation and deliver reliable information to higher-level analytic applications is GE Fanuc’s award-winning Proficy HMI/SCADA – CIMPLICITY. With the latest features of CIMPLICITY 8.0, including a powerful graphics engine, dynamic time handling and digital graphical replay (DGR) 2.0, operators and engineers have the power and security to precisely monitor and control every aspect of their environment, equipment and resources. The results: faster response, reduced costs and increased profitability.
Making Something Out Of Nothing
Landfill gases are colorless vapors produced at solid waste landfills where trash and garbage are buried in the ground and covered with dirt. Over time, bacteria in the soils will break down organic wastes in the landfill. The by-product of these bacteria breaking down the garbage will produce gases. The amount and type of landfill gas depends on a number of factors such as the amount of garbage buried, the age of the landfill, the depth of the landfill, and the chemical environment inside the landfill.
Landfill gas consists of methane, carbon dioxide, and hydrogen sulfide. Methane is a very potent greenhouse gas that is a key contributor to global climate change, over 21 times more potent than carbon dioxide. Methane also has a short, 10-year, atmospheric life. Because methane is both potent and short-lived, reducing methane emissions from municipal solid waste landfills, the second largest source of methane in the United States, is one of the best ways to achieve a near-term beneficial impact in mitigating global climate change.
It is estimated that a landfill gas to energy projects will capture roughly 60 to 90% of the methane emitted from the landfill, depending on system design and effectiveness. The gas is collected and conveyed using a system of vertical and horizontal wells and a positive displacement blower to the landfill gas to energy facility. Prior to the landfill gas going to the internal combustion engines it is processed through IES’ proprietary gas scrubbing system, which has been designed and developed to provide low maintenance, extended life to the internal combustion engines. The scrubbing system cools the gas and uses dehydration process, which removes particulates and water that otherwise, would have harmed the engines. After the landfill gas is processed through the scrubbing system is it delivered to the internal combustion engines where the captured methane is destroyed, converted to water and a much less potent carbon dioxide, when the gas is burned to produce electricity.
Utilizing methane to produce electricity displaces fossil fuels and avoids carbon dioxide that otherwise would have been released. The electricity can then be distributed to the grid except for a small portion, which is channeled back into operations for reuse in the process.
This innovative company is also using the waste heat generated from jacket water and engine exhaust to heat a 12-acre greenhouse facility that produces vine-ripened, hydroponic tomatoes. The heat generated is transferred in continuous loop from heat exchangers at the company’s power plants to the heat exchangers at the greenhouse. Because of the unique way in which the plants are grown, they have a growth season which lasts approximately eight to nine months, allowing the greenhouse to produce more than 6 million pounds of tomatoes annually.
“Innovative Energy Systems is producing a great example of optimizing a waste source to make something we can all use today and tomorrow,” concluded Sylvester. “Their reuse of methane gas to produce electricity has a direct and positive impact on the environment.”
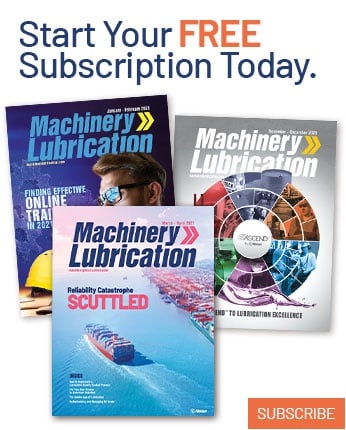