Kaizen events are a powerful, team-based activity for making rapid improvements in an office or manufacturing process. Kaizen events can be focused to improve all of the typical company measurables as shown below.
In review, kaizen is a Japanese word that means to “change for the good.” Doing “little things” better every day defines kaizen – slow, gradual but constant improvement (continuous improvement) – in any area that will eliminate waste and improve customer satisfaction.
The definition of kaizen
Kaizen is what the Japanese did to the ideas they picked up from American manufacturers in the 1950s. The Japanese combined employee empowerment and kaizen and then had everyone in their plants doing “little things” better every day. Kaizen is the most powerful tool in the Japanese business improvement arsenal.
The target of kaizen is cost reduction through the elimination of waste at all levels in the business process.
The definition of kaizen has grown to mean something different in American manufacturing. Most American companies do not recognize the potential of employee empowerment. American culture, in general, struggles with techniques that are gradual and produce small improvements – even if these small improvements occur daily! Americans are innovators, and that means “giant steps” – home runs, not singles!
The difficulty is that some companies that are in a “quick fix” mode inaccurately see and try to use kaizen events as the vehicle to make them world class. Kaizen events may be the tires on that vehicle, but they are not the engine. All of the company’s associates working together are the engine. Their knowledge, skills, ideas and understanding of why the company is doing a world-class enterprise implementation keep the engine running.
Events must be combined with the “Japanese kaizen” method of everybody making small improvements every day if the WCE implementation is to be successful.
What can a kaizen event accomplish? Rapid improvement in the performance of a specific project process, production process, office process or manufacturing cell.
What will a kaizen event not accomplish? Here’s a list:
-
Long-term change at the event work site. If events are used as the sole improvement strategy, backsliding will occur as soon as the event is over. Someone from the event team or the company’s kaizen facilitator must monitor the worksite on a daily basis and must continue to coach and counsel the team on the improvements and why they are necessary.
-
A significant increase in the understanding of world-class enterprise tools, techniques and business reasons for doing lean by the people who work daily in the event area. This applies when events are used as the sole improvement strategy.
-
Changing the culture of the people who work daily in the event area or in the rest of the organization.
When do you use a kaizen event? Here are some notes:
No. 1 Priority – Pre-project/process planning
- Lowest-cost time to make changes
- Goal is to eliminate/reduce engineering or process changes after project/process begins
- Opportunity to orient and train all associates who interface with the process
- Does not add to project time
No. 2 Priority – When the project/process is operating
- Americans always seem to have time to do things over
Lean as a system
A kaizen event is a powerful business improvement tool, but it will just add additional waste to your organization (improve with a kaizen event and then backslide) if it is not used as part of the “lean system” by which a business is run. Lean as a system must include:
- Top-down management leadership commitment and support
- Policy deployment and lean implementation planning
- An organization-wide communication plan
- Associate empowerment and participation
- A customer focus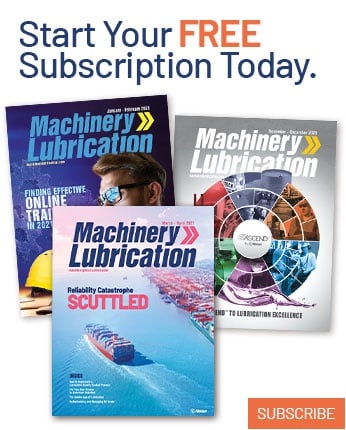